نحوه ساخت مخزن استیل
در این مقاله به نحوه ساخت مخزن استیل پرداخته می شود و به شما کمک می کند که در زمان بسیار کوتاه به بررسی موضوع مقاله پرداخته و دانش خود را در این حوزه ارتقا دهید. این مقاله بر اساس آخرین ژورنالهای صنعت فولاد گردآوری شده و تلاش شده که با بیان خلاصه و روان به موضوع پرداخته شود.
نحوه ساخت مخزن استیل
در دنیای کنونی که صنایع به سمت تولید ایمن، بهداشتی و بادوام پیش می روند، نحوه ساخت مخزن استیل به عنوان یکی از اصلی ترین تجهیزات ذخیره سازی و فرآوری، اهمیت ویژه ای پیدا کرده است. این مخازن در طیف وسیعی از صنایع نظیر مواد غذایی، دارویی، شیمیایی، نفت و گاز، و آب و فاضلاب مورد استفاده قرار می گیرند و در حفظ کیفیت مواد اولیه و محصولات نهایی نقش بسیار مهمی ایفا می کنند. ویژگی های برجسته ای همچون مقاومت بالا در برابر خوردگی، پایداری در شرایط دمایی و فشاری مختلف، و امکان شست وشوی آسان و ضدعفونی دقیق، مخازن استیل را از سایر مخازن متمایز می کنند. فرآیند ساخت مخزن استیل به یک عملیات مکانیکی ساده محدود نمی شود. این فرآیند شامل طراحی مهندسی دقیق، انتخاب مواد اولیه مناسب، رعایت اصول تخصصی جوشکاری و انجام آزمون های کنترل کیفیت مطابق با استانداردهای بین المللی است. طراحی و تولید صحیح این تجهیزات، علاوه بر تضمین عملکرد بهینه، تأثیر قابل توجهی بر ایمنی فرایندها، افزایش طول عمر دستگاه ها، و کاهش هزینه های نگهداری و تعمیرات دارد. در این مقاله، مراحل طراحی و ساخت مخازن استیل را گام به گام بررسی خواهیم کرد؛ از انتخاب نوع مناسب استیل و طراحی اولیه تا فرآیندهای برش کاری، جوشکاری، پولیش، تست های نهایی و نکاتی مهم در بهره برداری و نگهداری. هدف این است که دیدگاه جامع و کاربردی در خصوص ساخت یک مخزن استیل استاندارد ارائه شود تا تولیدکنندگان و مصرف کنندگان بتوانند با اطلاعات دقیق تر تصمیم بگیرند و انتخاب های هوشمندانه تری داشته باشند. برای مشاهده ورق استیل کلیک کنید. در این مقاله به نحوه ساخت مخزن استیل پرداخته می شود.
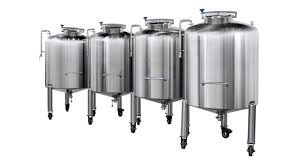
نحوه ساخت مخزن استیل
انواع مخازن استیل و کاربردهای آن
مخازن استیل بسته به نوع کاربرد، شرایط عملیاتی و الزامات بهداشتی یا فنی، در مدل ها و ساختارهای متنوع طراحی و ساخته می شوند. این تنوع به صنایع اجازه می دهد تا متناسب با نیازهای فرآیندی خاص خود، بهترین گزینه را از میان انواع مختلف این تجهیزات انتخاب کنند. یکی از مهم ترین دسته بندی ها بر اساس فشار کاری مخزن صورت می گیرد. مخازن استیل می توانند تحت فشار (Pressure Vessels) یا غیر فشاری (Atmospheric Tanks) طراحی شوند. مخازن تحت فشار معمولاً به منظور ذخیره یا انجام واکنش های شیمیایی در دما و فشار بالا در صنایع شیمیایی، پتروشیمی و دارویی به کار می روند. در مقابل، مخازن غیر فشاری برای نگهداری مایعاتی چون آب، روغن، شیر، عصاره های گیاهی یا مواد اولیه غذایی مورد استفاده قرار می گیرند. از دیگر تقسیم بندی ها می توان به ساختار جداره ها اشاره کرد که این مخازن را به دو نوع تک جداره و دوجداره تفکیک می کند. مخازن تک جداره برای نگهداری مواد در دمای محیط مناسب هستند، اما زمانی که کنترل دما ضروری باشد (مثل نگهداری شیر یا مواد حساس دارویی)، از مخازن دوجداره استفاده می شود. در این نوع تجهیزات، فضایی میان دو جداره برای جریان آب گرم، بخار یا ماده سردکننده وجود دارد که کمک به تنظیم دمای محصول داخل مخزن می کند. در برخی کاربردها نیز از مخازن سه جداره که دارای لایه ای جداگانه از عایق حرارتی هستند، استفاده می شود. نوع دیگری از مخازن استیل که کاربرد گسترده ای دارد، مخازن همزن دار یا میکسرها هستند. این مخازن مجهز به همزن های مکانیکی یا پنوماتیکی بوده و برای ترکیب، حل کردن یا همگن سازی مواد درون مخزن استفاده می شوند. صنایع دارویی، غذایی، آرایشی و شیمیایی از این نوع تجهیزات بهره گیری فراوان دارند. طراحی مخازن همزن دار باید به گونه ای باشد که همزن در موقعیت مناسب نصب شده و بازده مطلوب با کمترین مصرف انرژی حاصل شود. از نظر نصب و قرارگیری، مخازن استیل ممکن است به صورت ایستاده (عمودی)، خوابیده (افقی) یا مدفون ساخته شوند. مخازن عمودی رایج ترین کاربرد را دارند و اغلب در محیط هایی با فضای محدود یا خطوط تولید عمودی استفاده می شوند. مخازن افقی مناسب مکان هایی با محدودیت ارتفاع یا نیاز به پایداری بیشتر هستند، در حالی که مخازن مدفون برای ذخیره سازی بلندمدت آب، سوخت یا فاضلاب طراحی می شوند. کاربردهای مخازن استیل بسیار متنوع هستند و بسته به طراحی آن ها در صنایع مختلف نقش کلیدی ایفا می کنند. در صنایع غذایی برای نگهداری موادی نظیر شیر، آبمیوه، رب گوجه فرنگی، روغن و حتی عسل استفاده می شوند. در صنایع دارویی برای تولید، فرآوری و نگهداری محلول ها، سرم ها، عصاره های گیاهی و ترکیبات حساس به کار می روند. همچنین در حوزه شیمیایی و آرایشی برای ذخیره و مدیریت ترکیباتی همچون اسیدها، قلیاها، رنگ ها، شوینده ها و مواد نیمه ساخته مناسب هستند. در صنایع نفت، گاز و پتروشیمی نیز از این مخازن برای ذخیره گازهای مایع، نفت سفید، مواد قابل اشتعال و خورنده استفاده می شود؛ خصوصاً زمانی که مقاومت در برابر خوردگی و شرایط جوی شدید اهمیت بالایی دارد. در مجموع، انتخاب نوع مناسب مخزن استیل نیازمند بررسی دقیق شرایط فنی از جمله نوع ماده ذخیره شده، دما، فشار و الزامات بهداشتی یا صنعتی است. این گستره متنوع از طراحی ها و کاربردها امکان ساخت محصولی دقیقاً متناسب با نیاز مصرف کننده را فراهم می کند.
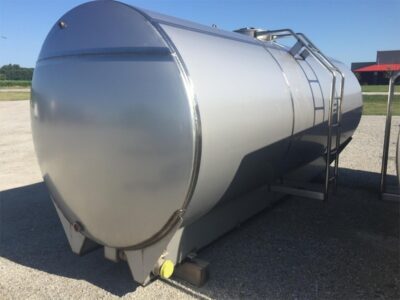
نحوه ساخت مخزن استیل
مراحل طراحی مهندسی مخزن استیل
طراحی مهندسی مخازن استیل از مراحل بسیار حیاتی در فرآیند ساخت این تجهیزات به شمار می رود و تأثیر مستقیم بر ایمنی، کارایی و ماندگاری مخزن دارد. این مرحله پیش از شروع هرگونه عملیات فیزیکی ساخت انجام می شود و نیازمند تحلیل های دقیق فنی، شناخت شرایط عملکرد مخزن و رعایت دقیق استانداردهای معتبر بین المللی است. اولین گام در طراحی، تعیین ظرفیت مخزن بر اساس نیاز پروژه است. از حجم های کوچک چند لیتری در کاربردهای آزمایشگاهی تا ظرفیت های چند هزار لیتری صنایع بزرگ، طراح موظف است بر اساس ظرفیت مورد نیاز، فضای موجود و روش نصب (مانند ایستاده، افقی یا زمینی)، ابعاد اولیه را مشخص کند. در مرحله بعد، شرایط کاری مخزن شامل فشار و دمای عملیاتی معین می شود. در صورت استفاده مخزن تحت فشار (مانند سیستم های بخار یا ذخیره مواد واکنش زا)، طراحی باید مطابق استانداردهای معتبری همچون ASME Section VIII یا EN 13445 انجام شود. این استانداردها جزئیاتی مانند ضخامت جداره ها، درب ها و سرها، نحوه جوشکاری و الزامات آزمایش های ایمنی را مشخص می کنند. اگر مخزن برای ذخیره مواد با دمای خاص طراحی شده باشد (به عنوان مثال مواد گرم، مایعات سرد یا فرآورده های حساس)، نیاز به طراحی دوجداره یا استفاده از لایه های گرمایشی/سرمایشی مطرح می شود. انتخاب نوع استیل مرحله مهم دیگری در فرآیند طراحی است. به طور معمول از استیل ضدزنگ گرید ۳۰۴ یا ۳۱۶ استفاده می شود. گرید ۳۰۴ برای مصارف عمومی مناسب بوده و گرید ۳۱۶ به دلیل داشتن مولیبدن مقاومت بالاتری در برابر خوردگی، به ویژه در محیط های حاوی کلرید (مانند صنایع غذایی یا شیمیایی) دارد. انتخاب دقیق آلیاژ تأثیر بالایی بر جلوگیری از زنگ زدگی، افزایش طول عمر مخزن و کاهش هزینه های تعمیر و نگهداری دارد. در ادامه فرآیند طراحی، محاسباتی برای ضخامت ورق ها، نوع عدسی ها (مانند بیضوی، تخت یا نیم کروی)، محل نازل ها و نحوه اتصال پایه ها انجام می شود. علاوه بر تحمل فشار داخلی، ضخامت ورق ها باید به گونه ای باشد که مقاومت کافی در برابر فشار خارجی، ضربه ها، لرزش یا جابه جایی داشته باشد. همچنین نقاط نصب تجهیزات جانبی مانند فشارسنج، دماسنج، شیرهای ورودی و خروجی، دریچه های بازدید و در صورت وجود همزن باید با دقت در نقشه گنجانده شوند تا هم سهولت در تعمیرات و دسترسی فراهم شود و هم ایمنی عملیات حفظ گردد. یکی دیگر از بخش های مهم طراحی به نوع جوش و محل قرارگیری درزها اختصاص دارد. تنظیم دقیق مسیرهای جوشکاری و نوع جوش (مانند لب به لب یا فیلت) در این مرحله انجام می شود. همچنین طراحی مسیرهای جریان برای سیستم های تمیزکاری (CIP) یا استریلیزاسیون (SIP) بسیار حائز اهمیت است، به ویژه در صنایع دارویی یا غذایی که رعایت اصول بهداشتی الزامی است. در انتها، تمامی اطلاعات طراحی در قالب نقشه های مهندسی دو بعدی و سه بعدی، لیست متریال و دستورالعمل های ساخت مستند می شود. این مستندات پایه ای برای فرآیند ساخت و کنترل کیفیت در مراحل بعدی محسوب شده و در برخی پروژه ها نیاز به تأیید ناظران فنی یا مراجع استاندارد پیش از ورود به مرحله اجرا دارد. برای مشاهده اتصالات استیل کلیک کنید و یا برای اطلاع از نحوه ساخت مخزن استیل به ادامه مقاله رجوع فرمایید.
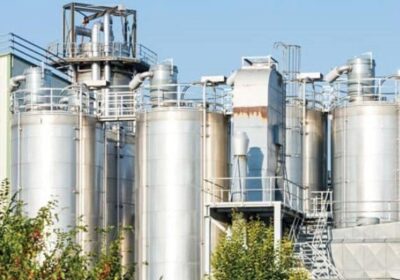
نحوه ساخت مخزن استیل
فرآیند ساخت گام به گام مخزن استیل
فرآیند ساخت مخزن استیل پس از تکمیل طراحی مهندسی و تأیید نهایی نقشه ها آغاز می شود و شامل چندین مرحله دقیق و هماهنگ است که اجرای صحیح آن ها به کیفیت نهایی محصول منجر می شود. ابتدا مواد اولیه تهیه و بازرسی می شوند. ورق های استیل مورد نیاز (مانند استیل ۳۰۴ یا ۳۱۶) از تأمین کنندگان معتبر خریداری شده و گواهی مواد (Mill Test Certificate) بررسی می شود تا خلوص، یکنواختی ضخامت و سلامت سطحی آن ها تضمین گردد. پس از تأیید مواد، برشکاری طبق ابعاد مشخص شده در نقشه ها انجام می شود. این عملیات با استفاده از دستگاه های برش دقیق نظیر پلاسما، لیزر یا واترجت انجام شده و شامل برش بخش های مختلف مانند بدنه، سرها (عدسی ها)، کف، نازل ها و دیگر اجزا است. دقت در این مرحله برای کاهش ضایعات و بهبود کیفیت اتصال اهمیت ویژه ای دارد. در مرحله نوردکاری، ورق ها شکل دهی شده و به صورت استوانه یا مخروط درمی آیند. سپس لبه های آن ها تنظیم شده تا برای جوشکاری آماده شوند. به طور هم زمان، سرها و عدسی ها نیز با استفاده از دستگاه های مخصوص مانند پرس هیدرولیکی، بر اساس شعاع و انحنای طراحی شده شکل می گیرند. جوشکاری قطعات اصلی در مراحل بعدی انجام می شود. ابتدا درز طولی بدنه جوش داده شده و سپس سرها و کف به آن متصل می شوند. روش های TIG یا MIG به دلیل دقت بالا و کیفیت مطلوب برای این کار به کار می روند. عملیات جوشکاری در چند پاس انجام شده و هر مرحله با تمیزکاری و بازرسی همراه است تا کیفیت جوش مطابق استانداردهای معتبر نظیر ASME یا DIN کنترل شود. پس از جوشکاری، اجزای جانبی نظیر فلنج ها، شیرها، پایه ها، همزن ها، نازل های ورودی/خروجی، دریچه های بازدید و نقاط سنجش بر اساس موقعیت های مشخص در طراحی نصب می گردند. این مرحله نیازمند دقت بالا است تا عملکرد کلی مخزن مختل نشود. بسته به نوع کاربرد مخزن، عملیات پولیش کاری داخلی و خارجی اجرا می گردد. برای کاربردهای دارویی یا غذایی، سطح داخلی مخزن باید به صورت آینه ای یا با زبری کمتر از ۰.۸ میکرون پرداخت شود تا از رشد میکروارگانیسم ها یا باقی ماندن مواد جلوگیری شود. این پرداخت ممکن است به روش مکانیکی، الکتروشیمیایی یا ترکیبی صورت گیرد. در ادامه، مخزن تحت تست های کنترل کیفیت قرار می گیرد. آزمایش هایی نظیر نشتی و فشار (هیدرواستاتیک یا پنوماتیک) برای اطمینان از استحکام و آب بندی مخزن اجرا می شوند. همچنین ممکن است تست رادیوگرافی برای بررسی وضعیت داخلی جوش ها انجام شود. در مخازن بهداشتی نیز آزمون هایی مانند پاکیزگی سطح جوش ها (Weld Seam Passivation) و قابلیت شست وشو با سیستم CIP/SIP ضرورت دارند. در نهایت، مخزن پس از مونتاژ نهایی بسته بندی شده و تمام مدارک فنی، گزارش های تست، دفترچه راهنما و گواهی نامه های لازم تحویل مشتری می گردد. در صورت نیاز، تیم سازنده ممکن است حمل و نصب مخزن را نیز بر عهده بگیرد.
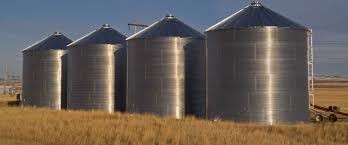
نحوه ساخت مخزن استیل
روش های جوشکاری در ساخت مخزن استیل
جوشکاری در فرآیند ساخت مخازن استیل به عنوان یکی از حساس ترین مراحل، نقش کلیدی در ایمنی، دوام و عملکرد نهایی این تجهیزات دارد. کیفیت اتصال قطعات مستقیماً بر کارایی مخزن تأثیر می گذارد و بنابراین، انتخاب روش جوشکاری باید با دقت و با توجه به نوع آلیاژ، ضخامت ورق ها، شرایط کاری مخزن (مانند دما و فشار)، ضرورت رعایت بهداشت سطح داخلی و استانداردهای طراحی انجام شود. یکی از متداول ترین روش ها، جوشکاری TIG (Tungsten Inert Gas) یا جوش آرگون است که در آن از الکترود تنگستن غیرمصرف شونده و گاز محافظ آرگون برای ایجاد قوس و جوش استفاده می شود. این روش به دلیل دقت بالا، کنترل حرارت مناسب و تولید جوشی صاف و تمیز، مخصوصاً برای استیل های ضدزنگ مناسب است. صنایع غذایی و دارویی که نیاز به رعایت ملاحظات بهداشتی بالایی دارند، اغلب از این روش بهره می برند. استفاده از جوش TIG عمدتاً در قسمت های حساس چون درزهای داخلی، نازل ها و نواحی دارای دسترسی محدود صورت می گیرد. روش دیگر، جوشکاری MIG (Metal Inert Gas) یا GMAW است که در آن از سیم جوش مصرف شونده به همراه گاز محافظ (معمولاً آرگون با درصدی CO₂) استفاده می شود. در مقایسه با TIG، این روش سرعت بالاتری دارد و برای مواردی که نیاز به حجم بالا یا زمان کم باشد، مناسب است. با این حال، کیفیت سطحی و دقت جوش MIG معمولاً پایین تر بوده و به همین دلیل برای نواحی داخلی مخازن بهداشتی کمتر استفاده می شود. برای پروژه های بزرگ تر یا مخازن با ضخامت قابل توجه، از جوشکاری قوسی زیرپودری (SAW) استفاده می شود. این روش که در آن جوش تحت لایه ای از پودر خاص انجام می گیرد، از ورود اکسیژن و آلودگی به محل جوش جلوگیری کرده و مناسب برای ایجاد درزهای طولی با نفوذ عمقی بالا است. البته این روش به دلیل ساختار خود برای بخش های پیچیده یا ظریف کاربرد ندارد. صرف نظر از روش انتخابی، آماده سازی دقیق محل جوش، پیش گرمایش در صورت نیاز، انتخاب فیلر مناسب و انجام دقیق پاس های جوش اهمیت بسیاری دارند. پس از هر پاس جوش نیز تمیزکاری سطح الزامی است تا آلودگی یا باقی مانده ها بر کیفیت جوش اثر منفی نگذارند. در بسیاری موارد، پس از اتمام فرآیند جوشکاری، عملیات پسیواسازی سطح جهت حذف تنش های داخلی و پیشگیری از خوردگی بین دانه ای توصیه می شود. تمام جوش ها باید تحت تست های غیرمخرب (NDT) نظیر رادیوگرافی (RT)، ذرات مغناطیسی (MT)، نفوذ مایع (PT) یا اولتراسونیک (UT) بررسی شوند تا کیفیت و سلامت آن ها تأمین گردد. بسته به استانداردهای پروژه، ممکن است آزمایشاتی مانند تست فشار یا نشتی نیز ضروری باشد. در نهایت، انتخاب روش جوشکاری باید با توجه به عوامل مختلفی نظیر نوع کاربرد، استاندارد ساخت، محدودیت بودجه، الزامات بهداشتی و تجربه نیروی اجرایی انجام شود تا مخزن نهایی ضمن برخورداری از ایمنی و دوام بالا، عملکرد مطلوبی ارائه دهد. برای مشاهده میلگرد استیل کلیک کنید و یا برای اطلاع از نحوه ساخت مخزن استیل به ادامه مقاله رجوع فرمایید.
کنترل کیفیت و تست های نهایی مخزن استیل
کنترل کیفیت و انجام تست های نهایی از مراحل بسیار کلیدی در ساخت مخازن استیل به شمار می رود. این مرحله نقشی حیاتی در تضمین عملکرد صحیح، ایمنی عملیاتی و تطابق محصول با استانداردهای فنی و بهداشتی دارد. کنترل کیفیت تنها به پایان فرایند ساخت محدود نمی شود، بلکه در طول مراحل تولید نیز بازرسی های دوره ای متعددی صورت می گیرد تا از بروز اشکالات احتمالی در مراحل بعدی جلوگیری شود. در گام نخست، مواد اولیه پیش از آغاز فرایند ساخت تحت بازرسی قرار می گیرند. این مرحله شامل بررسی گواهی نامه های مواد مانند Mill Test Certificate، تطابق آلیاژها، ضخامت ورق ها و سلامت سطحی مواد است. در این بررسی هرگونه آلودگی، خراش، ترک یا خوردگی شناسایی و رفع می شود. همچنین، تجهیزات جانبی مانند فلنج ها، نازل ها و شیرها از نظر ابعاد و کیفیت ساخت مورد بررسی دقیق قرار می گیرند. در جریان ساخت، کیفیت جوشکاری به صورت مرحله به مرحله کنترل می شود. این کار ابتدا با بازرسی بصری آغاز می گردد که شامل ارزیابی پیوستگی، یکنواختی و عدم وجود ترک یا حفره است. سپس با توجه به نوع پروژه، جوش ها تحت آزمون های غیرمخرب قرار می گیرند که از جمله آن ها می توان به موارد زیر اشاره کرد: تست رادیوگرافی برای شناسایی حفره های داخلی، ترک ها و ناپیوستگی جوش، خصوصاً در نقاط حساس همچون درزهای طولی. تست نفوذ مایع جهت تشخیص ترک های سطحی یا ناپیوستگی های ریز بر روی سطح جوش. تست اولتراسونیک برای تعیین عمق و یکنواختی جوش به روشی غیر مخرب. تست ذرات مغناطیسی که برای شناسایی ترک های سطحی در موارد خاص استفاده می شود، اگرچه برای استیل های ضدزنگ کاربرد محدودی دارد. پس از اتمام جوشکاری و نصب نهایی تمامی قطعات، مرحله آزمایش های عملیاتی آغاز می شود. رایج ترین روش در این بخش، تست فشار هیدرواستاتیک است که طی آن مخزن با آب پر شده و تحت فشاری بالاتر از فشار طراحی آزمایش می شود تا از عدم وجود نشتی و استحکام کلی اطمینان حاصل شود. در برخی پروژه های ویژه، آزمایش پنوماتیک با استفاده از هوا یا گازهای بی اثر انجام می گیرد که مستلزم احتیاط بیشتری به دلیل مخاطرات ایمنی است. در صورتی که مخزن برای کاربردهای دارویی یا غذایی طراحی شده باشد، تست پاکیزگی سطح برای سنجش میزان زبری داخلی انجام می شود؛ معمولاً زبری داخلی باید کمتر از ۰.۸ میکرون باشد. افزون بر این ممکن است آزمایش هایی مانند تست غیرفعال سازی شیمیایی برای افزایش مقاومت به خوردگی و یا تست شست وشوی CIP/SIP جهت تأیید قابلیت شست وشو در محل نیز اجرا شوند. در انتها، تمامی تست های انجام شده به همراه گزارش کامل آن ها در مستندات کنترل کیفیت ثبت می شوند. این مستندات شامل نقشه های نهایی، گزارش بررسی مواد اولیه، جوشکاری، آزمایش های غیرمخرب، فشار، ابعاد نهایی و مشخصات سطح هستند. در صورت لزوم، گواهی نامه های بهداشتی و انطباق با استانداردهای بین المللی نیز باید ضمیمه شوند. پس از تأیید نهایی تمامی مراحل توسط واحد کنترل کیفیت، مخزن برای بسته بندی و ارسال تحویل داده خواهد شد.
نکات مهم در بهره برداری و نگهداری از مخزن استیل
نکات کلیدی در بهره برداری و نگهداری مخازن استیل، به عنوان یکی از مراحل حیاتی پس از ساخت و نصب، تأثیر قابل توجهی بر طول عمر، عملکرد و ایمنی سیستم دارد. رعایت اصول بهره برداری صحیح و انجام نگهداری مناسب از مهم ترین گام ها در حفظ کیفیت و کارایی این تجهیزات است. در ادامه به موارد مهم در این زمینه پرداخته می شود. یکی از نخستین نکات در بهره برداری از مخزن استیل، توجه به کنترل شرایط عملیاتی است. مخزن باید در محدوده فشار و دمای طراحی شده عمل کند. تغییرات بیش از حد فشار یا دما می تواند به ساختار مخزن آسیب برساند. برای مخازن تحت فشار، نظارت مداوم بر فشار داخلی و شرایط دمایی اهمیت ویژه ای دارد. استفاده از تجهیزات دقیقی مانند فشارسنج، دماسنج و سیستم های هشدار مناسب نقش مؤثری در حفظ ایمنی مخزن ایفا می کند. پرهیز از بارگذاری اضافی نیز یکی دیگر از اولویت های مهم در بهره برداری است. هرگونه افزایش بیش از ظرفیت در حجم یا فشار می تواند باعث آسیب های جدی به بدنه و اتصالات مخزن شود. به عنوان مثال، اضافه کردن مایعات فراتر از حداکثر مجاز یا افزایش زیاد دما، ممکن است به ایجاد نشتی، ترک های ساختاری یا تغییر شکل جوش ها منجر شود. بنابراین، رعایت ظرفیت طراحی شده برای مخزن ضرورت دارد. تمیزکاری منظم از جمله اصولی است که خصوصاً در صنایع غذایی و دارویی اهمیت بالایی دارد، چرا که پاکیزگی و رعایت استانداردهای بهداشتی در این صنایع حیاتی است. استفاده از سیستم های تمیزکاری یا استریلیزاسیون در محل (CIP و SIP) برای شست وشوی سطوح داخلی مخزن توصیه می شود. همچنین، انتخاب مواد تمیزکننده مناسب و تنظیم دقیق دما و فشار شست وشو می تواند به حفظ سطح استیل و استانداردهای بهداشتی کمک کند. بازرسی های دوره ای و تعمیرات پیشگیرانه نیز از دیگر نکات برجسته در نگهداری مخازن استیل محسوب می شوند. به طور منظم باید بدنه مخزن از نظر وجود ترک، خوردگی یا تغییر شکل بررسی شود. این بازرسی ها باید شامل ارزیابی جوش ها، اتصالات، فلنج ها، نازل ها و شیرها باشد. عملکرد تجهیزات جانبی نظیر همزن ها و سیستم های کنترلی نیز باید بررسی شود. انجام تعمیرات پیشگیرانه قبل از وقوع مشکلات بزرگ می تواند هزینه های سنگین و توقف غیرمنتظره فرآیندها را کاهش دهد. مبحث خوردگی نیز در نگهداری مخازن استیل بسیار حائز اهمیت است. اگرچه استیل ضدزنگ مقاومت بالایی دارد، اما در مواجهه با مواد شیمیایی خاص یا محیط های مرطوب و دماهای بالا مستعد خوردگی است. استفاده از پوشش های ضد خوردگی یا لایه های محافظ می تواند عمر مفید مخزن را افزایش دهد. علاوه بر این، اجتناب از استفاده مواد شیمیایی شدیداً خورنده و بهره گیری از مواد ملایم برای تمیزکاری به حفظ کیفیت مخزن کمک می کند. در نهایت، آموزش کارکنان نقش کلیدی در بهره برداری ایمن و مؤثر ایفا می کند. آشنایی کامل پرسنل با روش های صحیح استفاده و نگهداری مخزن باعث کاهش ریسک ها و بهبود عملکرد کلی سیستم خواهد شد. همچنین، آموزش نکات ایمنی، نحوه استفاده از تجهیزات جانبی و انجام آزمون های نظارتی برای ارزیابی شرایط مخزن امری ضروری است. برای مشاهده ورق سیاه کلیک کنید و یا برای اطلاع از نحوه ساخت مخزن استیل به ادامه مقاله رجوع فرمایید.
جمع بندی
ساخت و بهره برداری از مخازن استیل یکی از مراحل کلیدی در بسیاری از صنایع محسوب می شود. با توجه به مقاومت بالای این نوع مخازن در برابر عوامل مختلفی نظیر فشار، دما و خوردگی، انتخاب دقیق مواد اولیه، طراحی مناسب، فرآیند ساخت باکیفیت و نگهداری مداوم می تواند به طور چشمگیری عمر مفید و کارایی این تجهیزات را افزایش دهد. در روند ساخت این مخازن، از طراحی اولیه تا جوشکاری و تست های نهایی، رعایت دقت و کیفیت در تمامی مراحل الزامی است. بهره گیری از روش های مناسب جوشکاری مانند TIG و MIG که بر اساس نوع کاربرد و نیاز فنی انتخاب می شوند، تضمین کننده استحکام و دوام کافی اتصالات مخزن است. علاوه بر این، استفاده از مواد اولیه باکیفیت مانند آلیاژهای ضدزنگ ۳۰۴ یا ۳۱۶ به دلیل مقاومت بالا در برابر خوردگی و فشارهای مختلف ضروری است. پس از اتمام مراحل ساخت، کنترل کیفی و انجام آزمایش های نهایی نظیر تست های فشار، تست های غیرمخرب (NDT) و تست های بهداشتی بسیار حائز اهمیت بوده و نقش بسزایی در اطمینان از ایمنی و عملکرد صحیح مخزن ایفا می کند. این آزمون ها به ویژه برای صنایع حساس مانند داروسازی، غذا و مواد شیمیایی اهمیت مضاعفی دارند تا از مشکلات احتمالی در آینده پیش گیری شود. در زمان بهره برداری، رعایت نکاتی همچون کنترل شرایط فشار و دما، تمیزکاری و نگهداری منظم، انجام بازرسی های دوره ای و تعمیرات پیشگیرانه، و مقابله با خوردگی می تواند عمر مفید مخزن را افزایش داده و عملکرد مطلوب آن را در بلندمدت تضمین کند. همچنین آموزش کارکنان برای استفاده صحیح و ایمن از مخازن یکی از اجزای مهم نگهداری به شمار می آید که نباید مغفول بماند. برای تضمین دوام و عملکرد بهینه مخزن، استفاده از استیل ضدزنگ باکیفیت و آلیاژهای متناسب با کاربرد ضروری است. رعایت استانداردهای بین المللی نظیر ASME و API در تمامی مراحل طراحی، ساخت و بهره برداری اهمیت بسزایی دارد. همچنین انجام بازرسی ها و تست های دوره ای شامل آزمون های غیرمخرب (NDT) و تست های فشار باید به طور منظم صورت گیرد. علاوه بر این، توجه به عملیات تمیزکاری، انجام تعمیرات پیشگیرانه و اقدامات لازم برای جلوگیری از خوردگی می تواند عمر مفید مخزن را تا حد قابل توجهی افزایش دهد. آگاه سازی کارکنان در خصوص نحوه صحیح استفاده از مخازن نیز نقشی تعیین کننده در پیشگیری از خرابی ها و آسیب های احتمالی دارد. با رعایت این اصول، امکان بهره برداری بهینه و طولانی مدت از مخازن استیل در صنایع مختلف فراهم شده و از ایجاد مشکلات پرهزینه و خطرات ایمنی پیشگیری خواهد شد. در این مقاله به نحوه ساخت مخزن استیل پرداخته شد.