برشکاری ورق سیاه
در این مقاله به برشکاری ورق سیاه پرداخته می شود و به شما کمک می کند که در زمان بسیار کوتاه به بررسی موضوع مقاله پرداخته و دانش خود را در این حوزه ارتقا دهید. این مقاله بر اساس آخرین ژورنالهای صنعت فولاد گردآوری شده و تلاش شده که با بیان خلاصه و روان به موضوع پرداخته شود.
برشکاری ورق سیاه
ورق سیاه به عنوان یکی از اصلی ترین محصولات فولادی، از طریق فرایند نورد گرم تولید می شود و به دلیل برخورداری از مقاومت بالا، قیمت مقرون به صرفه و قابلیت شکل پذیری مناسب، در صنایع متعددی مانند ساختمان سازی، خودروسازی، تولید ماشین آلات سنگین و مخازن تحت فشار کاربرد گسترده ای دارد. پس از تولید این ورق ها، نیاز است تا بر اساس مشخصات پروژه ها، ابعاد و اشکال خاصی از آن تهیه شود. در این مرحله، عملیات برشکاری نقش اساسی دارد و تأثیر مستقیمی بر کیفیت نهایی قطعات می گذارد. برشکاری ورق سیاه به معنای جدا کردن بخش هایی از ورق از طریق روش های حرارتی یا مکانیکی مختلف است. انتخاب هر روش وابسته به عواملی چون ضخامت ورق، نوع کاربرد، دقت مورد نیاز، سرعت تولید و هزینه های مرتبط است. با توجه به جایگاه کلیدی این عملیات در زنجیره تولید، آشنایی کامل با روش های گوناگون برشکاری، نقاط قوت و محدودیت های آن ها، و رعایت الزامات ایمنی هنگام کار، برای فعالان این حوزه امری ضروری محسوب می شود. این مقاله با هدف ارائه یک بررسی جامع درباره انواع روش های برشکاری ورق سیاه، تحلیل مزایا و معایب هر روش، و معرفی معیارهای مناسب برای انتخاب شیوه مطلوب تهیه شده است. همچنین تلاش شده تا نیازهای علمی و فنی دانشجویان، مهندسان و صنعتگران به صورت کاربردی پاسخ داده شود. برای مشاهده ورق سیاه کلیک کنید. در این مقاله به برشکاری ورق سیاه پرداخته می شود.
تعریف ورق سیاه
ورق سیاه به ورق فولادی تولید شده از فرآیند نورد گرم اطلاق می شود. در این روش، فولاد در دمای بالا (معمولاً بیش از ۹۰۰ درجه سانتی گراد) شکل داده می شود و به ضخامت های مختلف تبدیل می گردد. این فرآیند منجر به تولید ورقی با سطحی نسبتاً زبر و رنگ تیره مایل به خاکستری می شود. این ویژگی ظاهری دلیل نام گذاری آن به «ورق سیاه» است. از لحاظ خواص مکانیکی، این نوع ورق مقاومت بالایی دارد، از شکل پذیری خوبی برخوردار است و جوش پذیری مناسبی ارائه می دهد. بااین حال، به دلیل نداشتن پوشش محافظ مانند گالوانیزه یا رنگ، در برابر رطوبت مستعد زنگ زدگی است. به همین دلیل، کاربرد آن بیشتر در پروژه هایی است که ظاهر زیبا چندان اهمیت ندارد یا پس از فرآیند برشکاری و فرم دهی، روی ورق پوشش محافظ اعمال می شود. ورق سیاه عموماً در دو نوع اصلی تولید می شود: ۱. ورق سیاه معمولی (ST37): مناسب برای استفاده های عمومی و ساختمانی ۲. ورق سیاه صنعتی (مانند ST52): با مقاومت کششی بالاتر، که بیشتر در موارد صنعتی و تخصصی مانند ساخت قطعات خودرو و تجهیزات سنگین کاربرد دارد. این ورق ها بسته به نیاز، در اشکال مختلفی نظیر رول (کویل) یا شیت (برش خورده) عرضه می شوند. ضخامت های متفاوت آن ها تعیین کننده کاربردهای گسترده ای از اسکلت سازی و سوله سازی گرفته تا ساخت مخازن و سازه های سنگین است.
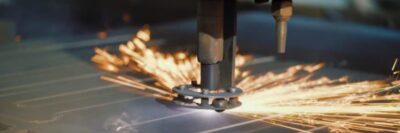
برشکاری ورق سیاه
برش مکانیکی ورق سیاه
برش مکانیکی ورق سیاه یکی از کاربردی ترین روش ها در صنعت فلزکاری است که با اعمال نیروی فیزیکی و بدون استفاده از حرارت انجام می شود. در این فرآیند، ابزارهایی مانند تیغه ها یا قالب های فلزی برای برش ورق در خطوط مشخص به کار می روند. به دلیل سهولت، سرعت بالا و هزینه اقتصادی، این روش به ویژه در کارگاه ها و تولیدات انبوه بسیار محبوب است. از ویژگی های بارز برش مکانیکی این است که هیچ حرارتی به ورق اعمال نمی شود و بنابراین ساختار متالورژیکی فولاد حفظ شده و خواص مکانیکی آن بدون تغییر باقی می ماند. در میان روش های مکانیکی، قیچی گیوتین به عنوان یکی از ساده ترین و رایج ترین دستگاه ها شناخته می شود. عملکرد این دستگاه شامل حرکت عمودی تیغه ای است که ورق را به صورت مستقیم و در طول مشخص برش می دهد. این شیوه بیشتر برای ورق هایی با ضخامت کم تا متوسط و برش های خطی مناسب است. نوع دیگری به نام قیچی غلطکی یا چرخشی، در تولیداتی که ورق ها به شکل رول یا کویل ارائه می شوند، کاربرد دارد. در این روش، دو تیغه دایره ای چرخنده، ورق را در حین عبور از دستگاه با دقت برش می دهند. برای برش های دقیق تر و ایجاد اشکال پیچیده، از دستگاه های پانچ CNC استفاده می شود. در این فناوری ورق طبق برنامه ای عددی در نقاط مشخص پانچ شده و قطعات با اشکال دلخواه تولید می شوند. این سیستم ها امکان ساخت قطعات با هندسه های پیچیده را فراهم می کنند، اما نیازمند قالب های مخصوص هستند و عمدتاً برای ضخامت های پایین تر مورد استفاده قرار می گیرند. در کارگاه های کوچک تر، ابزارهای ساده تری مانند قیچی های دستی یا اهرمی نیز رایج اند که عمدتاً برای برش های سبک و غیرحرفه ای استفاده می شوند. این روش ها هرچند ارزان و آسان هستند، اما دقت و توان کمتری دارند. با وجود مزایای متعدد برش مکانیکی، از جمله هزینه کمتر، عدم نیاز به تجهیزات گران قیمت و نگهداری کیفیت متالورژیکی ورق، این روش دارای محدودیت هایی نیز هست. از جمله نمی توان از آن برای برش منحنی ها یا اشکال بسیار پیچیده استفاده کرد، همچنین اغلب موجب ایجاد پلیسه یا لبه های خشن می شود و برای ورق های بسیار ضخیم مناسب نیست. بنابراین انتخاب این روش باید متناسب با نوع قطعه، ضخامت ورق و میزان دقت مورد نیاز انجام گیرد. برای مشاهده ورق روغنی کلیک کنید.
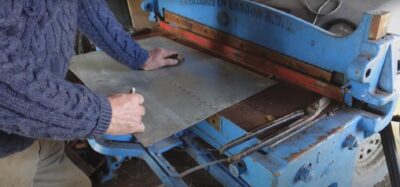
برشکاری ورق سیاه
برش حرارتی ورق سیاه
برش حرارتی یکی از مؤثرترین و پرکاربردترین روش های برش در صنعت فلزکاری به شمار می رود. این روش با استفاده از گرمای شدید، فلز را به نقطه ذوب یا احتراق رسانده و سپس با بهره گیری از گاز یا فشار هوا بخش مورد نظر را جدا می کند. برش حرارتی به ویژه برای ورق های فولادی نورد گرم با ضخامت های متوسط تا زیاد مناسب است و در پروژه هایی که نیازمند سرعت و قدرت بالا هستند، راهکاری اقتصادی و کارآمد محسوب می شود. یکی از قدیمی ترین و همچنان رایج ترین تکنیک های برش حرارتی، برش هواگاز یا اکسی استیلن است. در این روش، ترکیب گاز استیلن و اکسیژن شعله ای با دمای بالا ایجاد می کند که در ابتدا فلز را تا دمای احتراق گرم کرده و سپس با دمش اکسیژن خالص، فلز اکسید شده و فرآیند برش آغاز می شود. این روش برای ضخامت های بالا، حتی تا ۲۰۰ میلی متر، بسیار کارآمد است. با این حال، دقت پایین و نیاز به پرداخت لبه ها از معایب آن به شمار می آید. همچنین ناحیه حرارتی وسیعی که در این تکنیک ایجاد می شود، ممکن است برخی از خواص مکانیکی فلز اطراف ناحیه برش را تغییر دهد. روش دیگر، برش پلاسما است که در آن گازی مانند هوا، نیتروژن یا آرگون تحت فشار بالا از نازل عبور می کند و همراه با یک قوس الکتریکی به پلاسما تبدیل می شود. به دلیل دمای بسیار بالای پلاسما، این روش برای برش ورق های فولادی تا ضخامت حدود ۳۰ میلی متر گزینه ای سریع تر و دقیق تر نسبت به هواگاز است. برش حاصل تمیزتر و یکنواخت تر بوده اما تجهیزات مورد نیاز آن پیچیده تر و گران تر هستند و نیاز به منبع برق قدرتمندی دارند. دقت متوسط آن برای بسیاری از کاربردهای صنعتی که به سرعت تولید بالا نیاز دارند، یک انتخاب ایده آل است. در بین تمامی روش ها، برش لیزری دقیق ترین و پیشرفته ترین تکنیک برش حرارتی محسوب می شود. در این روش، پرتو نور لیزر بسیار متمرکز و پرفشار روی سطح فلز تابانده شده و آن را ذوب یا تبخیر می کند. نتیجه کار، برش هایی کاملاً صاف، تمیز و بدون پلیسه است که معمولاً نیازی به پرداخت نهایی ندارند. دقت بالا و امکان برش اشکال پیچیده از دیگر مزایای این روش هستند. با این حال، هزینه بالای تجهیزات و نگهداری آن باعث شده بیشتر برای ورق های با ضخامت کم تا متوسط (معمولاً تا ۲۰ میلی متر) مورد استفاده قرار گیرد. علاوه بر این، عواملی نظیر کیفیت سطح ورق و نبود آلودگی تأثیر مستقیمی بر عملکرد دستگاه دارد. انتخاب روش مناسب بسته به عواملی چون ضخامت و نوع ورق، دقت مورد نظر، هزینه تجهیزات و میزان تولید متفاوت خواهد بود. برای پروژه هایی که سرعت و امکان برش ضخامت بالا اولویت دارند، هواگاز گزینه مناسبی است. برای برش هایی با دقت بیشتر و سرعت قابل قبول، پلاسما ارجحیت دارد. اما برای تولید قطعات پیچیده، ظریف و با ظاهری بی نقص، برش لیزری بهترین گزینه است، اگرچه هزینه بالاتری دارد. در نهایت، برش حرارتی اگر به درستی انتخاب و اجرا شود، تأثیر بسزایی در افزایش کیفیت و بهره وری خواهد داشت.
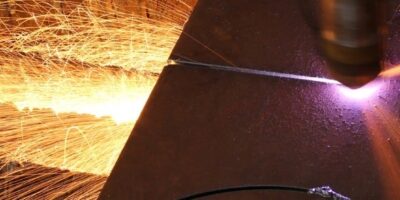
برشکاری ورق سیاه
برش واترجت ورق سیاه
برش واترجت یا برش با آب پرفشار یکی از روش های پیشرفته و دقیق در صنعت برشکاری است که طی آن از جریان متمرکز آب با فشار بسیار بالا، گاهی همراه با مواد ساینده ای مانند گارنت، برای برش مواد مختلف از جمله فلزات استفاده می شود. این شیوه برخلاف روش های حرارتی عمل می کند، زیرا حرارتی تولید نمی کند و به عنوان یک روش برش سرد شناخته می شود. همین ویژگی باعث شده واترجت در صنایعی که دقت بالا و حفظ خصوصیات متالورژیکی مواد اهمیت ویژه ای دارد، جایگاه مهمی پیدا کند. در فرآیند برش واترجت، آب توسط پمپ های مخصوص تا فشار بسیار بالا، معمولاً حدود ۴۰۰۰ تا ۶۰۰۰ بار، فشرده شده و سپس از نازل کوچکی با سرعت فوق العاده زیاد عبور می کند. در برش فلزاتی مانند ورق سیاه، به طور رایج از واترجت ساینده بهره گرفته می شود که در آن ذرات ساینده به جریان آب اضافه شده و قدرت برش را افزایش می دهند. این ذرات تحت فشار بالا همراه با آب باعث ایجاد سایش روی سطح فلز شده و برشی دقیق و تمیز به جا می گذارند. یکی از مزایای برجسته واترجت این است که هیچ گونه منطقه تحت تأثیر حرارت (HAZ) ایجاد نمی کند، بنابراین ساختار داخلی و ویژگی های مکانیکی فلز تغییر نمی کنند. همچنین لبه های ایجاد شده توسط این روش کاملاً صاف و بدون پلیسه هستند و نیازی به ماشین کاری یا پرداخت اضافی ندارند. از دیگر مزایای این فناوری می توان به توانایی برش اشکال پیچیده، عدم تولید دود یا گازهای مضر، و امکان برش مواد متنوع اشاره کرد. با وجود کیفیت و دقت بالای واترجت، این روش معایبی نیز دارد. یکی از اصلی ترین محدودیت ها هزینه های بالای تجهیزات و مصرف انرژی آن است. این سیستم ها به پمپ های قدرتمند و قطعاتی با مقاومت بسیار بالا در برابر سایش نیاز دارند که تعمیر و نگهداری آن ها نیز هزینه بر است. همچنین سرعت برش در مقایسه با تکنولوژی هایی مانند پلاسما یا لیزر پایین تر بوده، به خصوص زمانی که ضخامت ماده افزایش می یابد. در برش ورق سیاه، واترجت اغلب برای قطعاتی کاربرد دارد که نیازمند دقت بسیار بالا، کیفیت سطح عالی و حفظ خواص فیزیکی هستند. به عنوان مثال، در صنایعی مانند هوافضا، خودروسازی پیشرفته، تجهیزات پزشکی یا ساخت قطعات تزئینی ظریف، واترجت انتخابی ایده آل به شمار می آید. با این حال، برای برش های ساده و تکراری که به دقت بالا نیاز ندارند، استفاده از روش های مکانیکی یا حرارتی معمولاً اقتصادی تر است. در کل، علی رغم هزینه های بالای این روش، دقت بالا، انعطاف پذیری و کیفیت منحصر به فرد لبه های برش باعث شده واترجت در کاربردهای پیشرفته و حساس جایگاه ویژه ای داشته باشد. این فناوری به عنوان بخشی از زنجیره تولید مدرن در بسیاری از صنایع پیشرفته نقش کلیدی ایفا می کند. برای مشاهده ورق آلیاژی کلیک کنید.
انتخاب روش مناسب برشکاری برای ورق سیاه
انتخاب روش مناسب برای برشکاری ورق سیاه به عوامل گوناگونی بستگی دارد و نمی توان تنها با تکیه بر یک معیار، یک روش را برتر دانست. هر پروژه باتوجه به نیازهای فنی، محدودیت بودجه، حجم تولید، سطح دقت لازم و شرایط محیطی ممکن است به رویکرد خاصی احتیاج داشته باشد. بنابراین، در انتخاب روش برش، باید چند مؤلفه کلیدی به صورت هم زمان مدنظر قرار گیرند. یکی از مهم ترین عوامل، ضخامت ورق است. برای برش ورق های بسیار ضخیم، روش هایی مانند برش هواگاز مناسب اند؛ چراکه قابلیت برش ورق هایی با ضخامت بالای ۱۰۰ میلی متر را دارند. درحالی که برای ضخامت های کم یا متوسط که نیاز به دقت بالا نیز مطرح است، برش لیزری یا واترجت گزینه های بهتری محسوب می شوند. همچنین، روش پلاسما برای ضخامت های متوسط (تا حدود ۳۰ میلی متر) در شرایطی که سرعت و دقت نسبی به طور هم زمان مهم هستند، عملکرد مناسبی ارائه می دهد. عامل دیگر، دقت مدنظر و کیفیت لبه های برش است. اگر قطعات نهایی نیاز به پرداخت سطحی نداشته باشند و دقت ابعادی بالا اهمیت داشته باشد، برش لیزر یا واترجت پیشنهاد می شود. لیزر با ایجاد لبه های صاف و دقیق برای قطعات صنعتی حساس بسیار ایده آل است. واترجت نیز به علت عدم ایجاد حرارت در زمان برش، از تغییرات متالورژیکی جلوگیری کرده و سطحی تمیز و عاری از پلیسه ایجاد می کند. در مقابل، برش هواگاز معمولاً دقت پایین تری دارد و لبه های بریده شده آن نیازمند پرداخت ثانویه هستند. حجم تولید یا همان تیراژ کاری نیز عاملی تعیین کننده در انتخاب روش مناسب برشکاری به شمار می آید. برای تولیدات انبوه، روش هایی که از نظر سرعت و هزینه مقرون به صرفه باشند، ارجحیت دارند. به عنوان نمونه، برش مکانیکی با استفاده از گیوتین یا قیچی غلطکی در خطوط تولید با تیراژ بالا عملکردی سریع و مقرون به صرفه دارد. برش پلاسما نیز در محیط های صنعتی جهت تولید انبوه گزینه ای کارآمد است. در مقابل، روش واترجت بیشتر در پروژه های خاص یا تولیدات محدود به دلیل سرعت کمتر و هزینه بالاتر کاربرد دارد. هزینه تجهیزات و بهره برداری نیز نکته مهم دیگری است. زمانی که بودجه پروژه محدود باشد یا نیاز به ابزاری ساده و قابل حمل وجود داشته باشد، روش هایی نظیر برش مکانیکی یا هواگاز اولویت پیدا می کنند. درمقابل، دستگاه های پیشرفته ای مانند لیزر یا واترجت به مهارت اپراتورهای متخصص و نگهداری دقیق نیاز دارند که طبیعتاً هزینه بیشتری را به همراه دارند. علاوه بر این، جنس و کیفیت سطحی ورق تأثیر مستقیمی در تصمیم گیری ها دارد. برای مثال، ورق های دارای روکش یا حساس به حرارت نباید با روش های حرارتی نظیر پلاسما یا هواگاز برش داده شوند. همچنین برای طرح های قطعات پیچیده یا دارای انحناهای زیاد، روش هایی مانند CNC، لیزری یا واترجت که از قابلیت برنامه ریزی و حرکت دقیق برخوردارند، بهترین انتخاب محسوب می شوند. در مجموع می توان نتیجه گرفت که هیچ روش برشکاری به طور مطلق بر سایرین برتری ندارد. بلکه انتخاب صحیح باید با توجه به شرایط خاص هر پروژه شامل نوع و ضخامت ورق، میزان دقت موردنیاز، سرعت مطلوب و بودجه موجود انجام شود. این انتخاب درست می تواند کاهش هزینه ها، بهبود کیفیت محصول نهایی و افزایش بهره وری در فرآیند تولید را به همراه داشته باشد. برای مشاهده ورق گالوانیزه کلیک کنید.

برشکاری ورق سیاه
نکات ایمنی در برشکاری ورق سیاه
برشکاری ورق سیاه، همانند دیگر فرایندهای صنعتی، با خطرات بالقوه ای همراه است که در صورت بی توجهی می تواند منجر به آسیب های جدی جسمی یا حتی حوادث مرگبار شود. رعایت اصول ایمنی نه تنها برای حفظ سلامت کارکنان ضروری است، بلکه به بهبود راندمان کاری و کاهش توقف های ناخواسته نیز کمک می کند. بسته به نوع روش برش (مکانیکی، حرارتی یا واترجت)، مجموعه ای از نکات ایمنی باید رعایت شود که در ادامه به مهم ترین آن ها پرداخته خواهد شد. اولویت نخست در این حوزه، استفاده از تجهیزات حفاظت فردی (PPE) است. کارکنان باید از عینک ایمنی مناسب به ویژه در برش هایی مانند لیزری، پلاسما و هواگاز، لباس کار نسوز، دستکش مقاوم در برابر حرارت یا بریدگی، کفش ایمنی و محافظ گوش برای محیط های پرصدا استفاده کنند. این تجهیزات از تماس مستقیم با جرقه ها، ذرات داغ یا تیغه های متحرک جلوگیری می کنند و نقش حیاتی در پیشگیری از حوادث ایفا می کنند. در برش های حرارتی نظیر هواگاز، استفاده از گازهای قابل اشتعال مانند استیلن ممکن است خطر آتش سوزی و انفجار را افزایش دهد. لازم است که اتصالات گازها از سلامت کامل برخوردار باشند و هیچ نشتی وجود نداشته باشد. روشن کردن شعله مشعل باید فقط با استفاده از فندک های ایمنی انجام گیرد و شعله نباید در نزدیکی مواد اشتعال پذیر یا مخازن تحت فشار قرار گیرد. همچنین، تهویه مناسب برای تخلیه گازهای سمی و دود حاصله از برش ضروری است. در فرآیند برش لیزری، تابش پرتوهای مادون قرمز و فرابنفش ممکن است آسیب هایی به چشم و پوست وارد کند. ازاین رو، دستگاه باید مجهز به حفاظ نوری و سنسورهای ایمنی بوده و کاربران آموزش کافی جهت کار با دستگاه های CNC و لیزر را دریافت کرده باشند. رعایت دستورالعمل های مشخص سازنده نیز الزامی است. برش پلاسما با جریان برق ولتاژ بالا و درجه حرارت زیاد کار می کند. برای کنترل ایمنی این روش، اتصال صحیح کابل ها، بررسی سلامت تجهیزات برقی، استفاده از عایق مناسب، و پرهیز از تماس دست های مرطوب با دستگاه ها ضروری است. همچنین به دلیل خطر بالای پاشش فلز مذاب و جرقه های تیز، استفاده از ماسک محافظ کامل توصیه می شود. در روش هایی مانند گیوتین یا قیچی مکانیکی، احتمال گرفتار شدن انگشتان یا بخش هایی از لباس در تیغه وجود دارد. برای پیشگیری از این خطرات باید سیستم های حفاظتی مناسب اطراف تیغه نصب شوند و اپراتور از نزدیک کردن دست یا اعضای بدن به محدوده خطر اجتناب کند. وجود دکمه توقف اضطراری (Emergency Stop) در دستگاه ها یکی دیگر از الزامات این روش است. در روش برش واترجت اگرچه حرارت تولید نمی شود، اما فشار بسیار بالای آب می تواند خطراتی جدی ایجاد کند. تماس مستقیم حتی کوتاه مدت با جریان واترجت می تواند سبب بریدگی های عمیق شود. بنابراین تنظیمات و تعمیرات دستگاه تنها زمانی مجاز است که سیستم کاملاً خاموش بوده و فشار آن تخلیه شده باشد. همچنین استفاده از محافظ کامل صورت، لباس ضدآب و کفش ایمنی برای کاربران الزامی است. با وجود تنوع در روش های برش، رعایت نظم در محیط کار و آموزش مداوم کارکنان از اهمیت ویژه ای برخوردار است. ابزارهای اضافی نباید به صورت پراکنده در اطراف دستگاه ها قرار گیرند و نگهداری منظم دستگاه ها مطابق با دستورالعمل های سازنده باید صورت پذیرد. پیش از شروع اقدامات برشکاری نیز مرور چک لیست ایمنی می تواند از وقوع بسیاری از حوادث جلوگیری کند. در خاتمه، آگاهی نسبت به خطرات احتمالی، اعمال اصول ایمنی و تقویت فرهنگ ایمنی در محیط کار از مهم ترین عوامل جلوگیری از حوادث ناگوار در فرایند برشکاری ورق سیاه است. توجه به ایمنی نه به عنوان یک انتخاب، بلکه باید به عنوان یک ضرورت غیرقابل جایگزین در تمامی مراحل کاری مورد توجه قرار گیرد. در این مقاله به برشکاری ورق سیاه پرداخته شد.