فرایند تولید ورق روغنی
در این مقاله به فرایند تولید ورق روغنی پرداخته می شود و به شما کمک می کند که در زمان بسیار کوتاه به بررسی موضوع مقاله پرداخته و دانش خود را در این حوزه ارتقا دهید. این مقاله بر اساس آخرین ژورنالهای صنعت فولاد گردآوری شده و تلاش شده که با بیان خلاصه و روان به موضوع پرداخته شود.
فرایند تولید ورق روغنی
فرایند تولید ورق روغنی که به آن نورد سرد نیز میگویند، یک عملیات پیچیده و مهندسیشده است که با استفاده از فولاد خام، معمولاً به صورت تختال یا اسلب، آغاز میشود. این فرآیند شامل مراحل متعددی است که در نهایت به تولید ورقهای نازک، صاف و با کیفیت بالا منجر میشود. این نوع ورقها در صنایع مختلفی نظیر خودروسازی، لوازم خانگی، ساختوساز و تجهیزات صنعتی بسیار پرکاربرد هستند. در ادامه، به بررسی جزئیات این مراحل میپردازیم.
تأمین ماده اولیه در فرایند تولید ورق روغنی
تأمین ماده اولیه در فرآیند تولید ورق روغنی، نقطه شروع و یکی از مراحل اساسی در زنجیره تولید محسوب میشود. برای تولید ورق روغنی، تختال فولادی یا اسلب (Slab) به عنوان ماده اولیه اصلی استفاده میشود که از فرآیندهای پایهای تولید فولاد به دست میآید. این تختالها اغلب با ذوب آهن خام یا قراضه فولادی در کورههای قوس الکتریکی یا کوره بلند تولید شده و پس از ریختهگری به صورت مستطیلهای ضخیم (معمولاً با ضخامت ۱۵۰ تا ۲۵۰ میلیمتر) شکل میگیرند. اسلبها معمولاً از فولاد کمکربن یا فولادهای کمآلیاژ ساخته میشوند تا خواصی مانند شکلپذیری، استحکام و قابلیت جوشپذیری مورد نیاز در مرحله نورد سرد را داشته باشند. ترکیب شیمیایی این اسلبها به گونهای تنظیم میشود که در نورد سرد و فرآیندهای بعدی، کیفیت مطلوب سطحی و ساختاری ورق حفظ گردد. درصد کربن غالباً پایین نگه داشته میشود تا انعطافپذیری ورق افزایش یابد و در کاربردهایی مثل بدنه خودرو یا قطعات صنعتی استفاده شود. تأمینکنندگان اسلب ممکن است کارخانههای فولاد داخلی یا وارداتی باشند. بسته به کیفیت و قیمت، برخی کارخانههای نورد سرد ممکن است از اسلبهای وارداتی بهره ببرند، به ویژه زمانی که قیمت جهانی اسلب کاهش یافته یا کیفیت خاصی از اسلب در بازار داخلی موجود نباشد. کارخانههایی که به صورت یکپارچه فعالیت میکنند، ممکن است بخش تولید اسلب را خود داشته و نیازشان را از تولید داخلی تأمین کنند. پس از تأمین اسلب، این قطعات فولادی باید قبل از ورود به نورد سرد، به شکل مناسب برش داده و در صورت نیاز پیشگرم شوند تا برای اسیدشویی و مراحل بعدی آماده شوند. هرگونه نقص در اسلب اولیه – چه از نظر ترکیب شیمیایی یا کیفیت سطحی – میتواند مستقیماً بر کیفیت نهایی ورق روغنی تأثیر بگذارد. به همین دلیل، انتخاب و تأمین ماده اولیه باید با دقت بالا و با رعایت استانداردهای بینالمللی انجام شود. به طور کلی، موفقیت و کیفیت نهایی ورق روغنی به شدت وابسته به کیفیت ماده اولیه آن است. تأمین صحیح، کنترل ویژگیهای متالورژیکی و سطحی اسلب و انتخاب مناسبترین نوع فولاد پایهای محکم برای تولید یک محصول با کیفیت فراهم میکند.
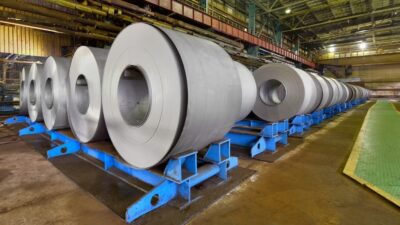
فرایند تولید ورق روغنی
اسیدشویی ورق روغنی
فرآیند اسیدشویی یکی از مراحل اساسی و ابتدایی در تولید ورق روغنی محسوب میشود که به بهبود کیفیت سطحی و آمادهسازی ورق برای نورد سرد کمک میکند. در این مرحله، ورقهایی که از نورد گرم به دست آمدهاند، دارای لایههایی از پوستههای اکسیدی و ناخالصیهای سطحی هستند. این لایهها در دمای بالا طی فرآیند نورد روی سطح فولاد شکل میگیرند. اگر این لایهها به درستی حذف نشوند، نهتنها کیفیت سطحی ورق کاهش مییابد، بلکه ممکن است به غلتکهای نورد سرد آسیب وارد کنند و دستیابی به ضخامت و همواری مطلوب را دشوار سازند. در فرآیند اسیدشویی، ورقهای فولادی از حمام اسید، که اغلب شامل اسید کلریدریک یا اسید سولفوریک است، عبور میکنند تا رسوبات اکسیدی را کاملاً از سطح ورق بزدایند. انتخاب نوع اسید بر اساس شرایط تولید، نوع فولاد، زمان فرآوری و معیارهای زیستمحیطی صورت میگیرد. اسید با واکنش شیمیایی، اکسیدها را حل کرده و سطح فولاد را تمیز و صیقلی میسازد. برای اجرای دقیق این فرآیند، دمای حمام، غلظت اسید و مدت زمان قرارگیری ورق در اسید باید بهدقت کنترل شود. پس از عبور از حمام اسید، ورقها معمولاً با آب شسته میشوند تا بقایای اسیدی را از سطح پاک کنند. سپس مرحله خشککردن انجام میشود تا از زنگزدگی زودهنگام جلوگیری به عمل آید. در برخی خطوط پیشرفته، پس از اسیدشویی، ورقها با یک لایه روغن سبک محافظ پوشیده میشوند تا از اکسید شدن دوباره در مراحل بعدی مانند انبارداری یا حملونقل جلوگیری شود. اسیدشویی به پاکسازی فیزیکی سطح کمک کرده و ورق را از نظر متالورژیکی برای نورد سرد آماده میکند. سطح یکنواخت و با کیفیتی که پس از اسیدشویی به دست میآید، تأثیر مهمی بر عملکرد نهایی ورق روغنی دارد که شامل ویژگیهایی مانند رنگپذیری، جوشپذیری و شکلپذیری است.
نورد سرد در فرایند تولید ورق روغنی
مرحله نورد سرد در فرآیند تولید ورق روغنی بسیار حیاتی است. در این مرحله، ضخامت ورق فولادی به دقت کاهش یافته و سطح آن به شکلی براق، صاف و بسیار یکنواخت تبدیل میشود. برخلاف نورد گرم که در دمای بالا انجام میشود، نورد سرد در دمای محیط صورت میگیرد و به دلیل عدم تغییرات فازی در ساختار فولاد، دقت ابعادی و کیفیت مکانیکی بالاتری را ارائه میدهد. در این فرآیند، ورقهایی که پیشتر اسیدشویی شدهاند و در صورت نیاز روغنزنی اولیه شدهاند، از میان مجموعهای از غلتکهای بسیار سخت و دقیق عبور میکنند. این غلتکها بهتدریج ضخامت ورق را کاهش میدهند؛ برای مثال، ضخامت اولیه از حدود ۲ میلیمتر ممکن است به کمتر از ۰.۵ میلیمتر برسد. برای جلوگیری از پاره شدن یا ترک خوردن ورق، این کاهش ضخامت به شکل مرحلهای و با عبور مکرر ورق از غلتکها انجام میشود. در طی نورد سرد، ساختار کریستالی فولاد فشرده و کشیده میشود، که منجر به افزایش سختی و استحکام ورق شده، اما در عین حال قابلیت شکلپذیری آن کاهش مییابد. بنابراین، پس از نورد سرد، برخی کاربردها نیاز به بازپخت دارند تا انعطافپذیری ورق بازگردد. یکی از ویژگیهای عمده نورد سرد، افزایش کیفیت سطحی است. چون ورق در این فرآیند با غلتکهای صیقلی تماس مستقیم دارد، سطح نهایی آن بسیار صاف و براق بوده و از پوستههای زبر یا ناهمواری عاری است. این ویژگی برای صنایعی نظیر خودروسازی، لوازم خانگی و ساخت قطعات تزئینی یا قابل رنگآمیزی بسیار مهم است. علاوه بر این، دقت ابعادی در نورد سرد بسیار بالاست و ضخامت نهایی با تلورانس بسیار پایین (در حد صدم میلیمتر) به دست میآید. این دقت بالا سبب میشود ورقهای روغنی حاصل، انتخابی ایدهآل برای کاربردهایی باشند که نیازمند مونتاژ دقیق یا پرداخت سطحی هستند. در نهایت، نورد سرد نه تنها یک مرحله فنی مهم محسوب میشود بلکه بر کیفیت نهایی محصول تأثیر تعیینکنندهای دارد. کنترل دمای محیط، کیفیت غلتکها، سرعت نورد و یکنواختی ماده اولیه در این سطح نقشی حیاتی در تولید ورقی دارد که از نظر فنی و تجاری بتواند در بازار رقابت کند. برای مشاهده ورق سیاه کلیک کنید.
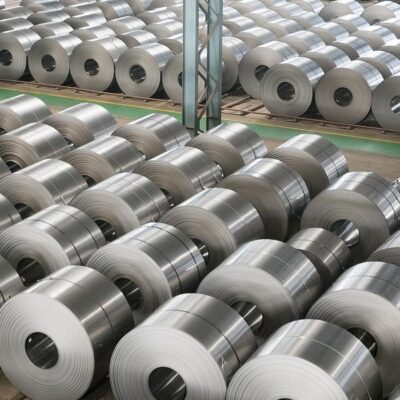
فرایند تولید ورق روغنی
آنیلینگ در فرایند تولید ورق روغنی
مرحله آنیلینگ یا بازپخت یکی از مراحل کلیدی در تولید ورق روغنی است که پس از نورد سرد انجام میشود و وظیفهاش بازیابی خواص مکانیکی و بهبود شکلپذیری ورق است. در طول نورد سرد، ورق در اثر فشار غلتکها به تغییر شکل پلاستیکی شدیدی دچار میشود، که این منجر به افزایش سختی و کاهش انعطافپذیری آن میشود و تنشهای داخلی در ساختار فلز به وجود میآید. فرآیند حرارتی آنیلینگ به رفع این مشکلات کمک کرده و ورق را برای استفادههای نهایی آماده میکند. در این مرحله، ورقها به شکل کلاف یا شیت وارد کوره آنیلینگ میشوند و در محیطی کنترلشده، اغلب با گازهای بیاثر مثل نیتروژن یا هیدروژن، و در دمای ۶۰۰ تا ۷۰۰ درجه سانتیگراد عملیات بازپخت صورت میگیرد. با این روش، ساختار کریستالی فلز تعادل خود را بازمییابد، دانههای فلزی بازسازی میشوند و تنشهای داخلی از بین میروند. نتیجه این است که ورق مجدداً خاصیت انعطافپذیری خود را به دست میآورد، ضمن حفظ برخی از استحکامهای مکانیکی. کورههای آنیلینگ به دو نوع اصلی تقسیم میشوند: کورههای پیوسته: در این مدل، کلافها به طور مداوم از داخل کوره عبور کرده و عملیات بازپخت همزمان صورت میگیرد. این روش برای تولیدات انبوه و یکنواخت ایدهآل است. کورههای دستهای: در این روش، کلافها به صورت گروهی درون کوره قرار داده میشوند و فرآیند حرارتی به طور ناپیوسته انجام میشود. این مدل کنترل بیشتری بر کیفیت محصول نهایی دارد و برای تولیدات خاص استفاده میشود. در طول آنیلینگ، حفظ تمیزی سطح و جلوگیری از اکسیداسیون بسیار حائز اهمیت است زیرا کوچکترین آلودگی میتواند ظاهر و ویژگیهای ورق را تغییر دهد. از این رو از محیطهای گازی پاک و تجهیزات دقیق بهره گرفته میشود. نتیجه فرآیند آنیلینگ، یک ورق فولادی نرمتر، یکنواختتر و با خواص مکانیکی متعادلی است که برای کاربردهایی مثل خمکاری، کشش عمیق، پرسکاری و رنگآمیزی بسیار مناسب خواهد بود. این مرحله اطمینان میدهد که ورق روغنی تولیدشده نه تنها در سطح بلکه از نظر عملکرد مکانیکی نیز در سطح بالایی از کیفیت قرار دارد.
پوسته زدایی نهایی و روغن کاری
در بخشهای پایانی تولید ورق روغنی، پس از فرآیند آنیلینگ، مرحله پوستهزدایی نهایی و روغنکاری آغاز میشود که نقش مهمی در ارتقای ویژگیهای سطحی و ظاهر ورق دارد و همچنین از آن محافظت میکند. این مرحله با هدف آمادهسازی برای استفاده یا بستهبندی صورت میگیرد. بعد از آنیلینگ، حتی با وجود بهبود خواص مکانیکی، ممکن است سطح ورق هنوز شامل موجهای ریز یا علائم ناشی از عملیات باشد. برای بهبود سطح به طور کامل، ورق وارد مرحلهای به نام اسکینپاس یا پوستهزدایی نهایی میشود. در این فرآیند، ورق با فشار ملایم از میان غلطکهای دقیق عبور میکند تا اصلاحات سطحی نهایی انجام شود. این عمل موجب حذف چینخوردگیها و افزایش صافی سطح شده، همچنین از پدیدههایی مثل فلوت مارک در حین شکلدهی جلوگیری میکند. یکی دیگر از اهداف اسکینپاس ایجاد یک الگوی بسیار جزئی روی سطح ورق است که به افزایش اصطکاک سطح در فرآیندهایی مانند رنگپذیری و شکلدهی کمک میکند. به عبارت دیگر، این عملیات علاوه بر جنبه زیبایی، عملکردی نیز دارد. پس از اسکینپاس، ورقها تحت فرآیند روغنکاری سطحی قرار میگیرند. در این مرحله، یک لایه نازک از روغن صنعتی مخصوص – که معمولاً ضدزنگ، تبخیرشونده یا قابل شستشو است – روی سطح ورق پاشیده میشود. هدف اصلی این کار جلوگیری از اکسید شدن و زنگزدگی ورق در حین حمل و انبارداری یا طی فرآیندهای بعدی مثل برش و خمکاری است. نوع روغن مصرفی بسته به کاربرد نهایی متفاوت است. به عنوان مثال، برای ورقهایی که بلافاصله وارد فرآیند رنگپاشی یا جوشکاری میشوند، از روغنهای سبک با قابلیت پاکشوندگی بالا استفاده میشود. در برخی موارد خاص، ممکن است ورقها بدون روغن نیز عرضه شوند اما با بستهبندی ویژه برای جلوگیری از زنگزدگی صورت میگیرد. در پایان، ورقهای روغنی آماده شده یا به صورت کلاف پیچیده میشوند یا در صورت نیاز، به شکل شیت برش خورده و بستهبندی میگردند. تمامی این مراحل پایانی با دقت بالا انجام میشود تا محصول نهایی از نظر فنی و ظاهری آماده ورود به بازار یا استفاده صنعتی خاص باشد. برای مشاهده تیرآهن کلیک کنید.
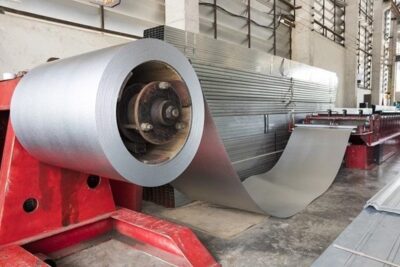
فرایند تولید ورق روغنی
برش و بسته بندی در فرایند تولید ورق روغنی
در مرحله پایانی تولید ورق روغنی، فرآیندهای برش و بستهبندی انجام میشود تا محصول مطابق نیاز مشتری آماده تحویل گردد. این مرحله بسیار مهم است زیرا بهطور مستقیم بر سهولت استفاده، حملونقل، نگهداری و حتی ایمنی کاربر نهایی تأثیر میگذارد. ورقهایی که به صورت کلاف (کویل) تولید شدهاند، بر اساس سفارش مشتری یا به همان شکل عرضه میشوند یا به شیتهای مسطح و برشخورده با ابعاد مشخص تبدیل میگردند. در صورت نیاز به شیت، ورق از دستگاههای برش عرضی (Cut to Length) عبور داده میشود؛ در این دستگاهها، کلاف باز شده و به ورقهایی با طول دقیق برش میخورد. دقت در این برشها بسیار حیاتی است، زیرا کاربردهای صنعتی مانند تولید قطعات خودرو یا لوازم خانگی به دقت بالا نیاز دارند. در مواقع دیگر ممکن است مشتری بخواهد ورق به صورت نوار باریک (Slit Coil) باشد. در این حالت، ورق وارد دستگاه اسلیتر (Slitter) میشود و به نوارهایی با عرض مورد نظر برش داده میشود که برای استفاده در صنایع ساخت لوله، پروفیل یا قطعات فرمدار بسیار مناسب است. پس از برش، مرحله بستهبندی انجام میشود که معمولاً شامل پیچیدن تسمههای فولادی یا پلاستیکی به دور کلاف یا شیتهاست تا آنها در حین حملونقل ثابت بمانند. روکشهای ضدآب، پلیمری، مقوا یا نایلون ضخیم نیز به کار میرود تا از زنگزدگی، پارگی یا خش جلوگیری شود. لبههای برشخورده نیز با محافظهای خاص پوشانده میشوند تا هم از آسیب به محصول جلوگیری شود و هم از خطرات احتمالی برای افراد کاسته شود. در نهایت، بستهها با برچسب مشخصات شامل نوع فولاد، ضخامت، عرض، شماره ذوب، وزن کلاف یا تعداد شیتها، تاریخ تولید و نام تولیدکننده علامتگذاری میشوند. این اطلاعات برای رهگیری محصول در زنجیره تأمین و تضمین کیفیت بسیار ضروری است. فرآیند برش و بستهبندی نهتنها باید دقیق و ایمن باشد بلکه مناسب با استانداردهای صنعتی و نیاز بازار انجام شود تا کیفیت نهایی ورق روغنی تا لحظهی تحویل حفظ گردیده و رضایت مشتری تضمین شود.