تولید زنجیر فولادی
در این مقاله به تولید زنجیر فولادی پرداخته می شود و به شما کمک می کند که در زمان بسیار کوتاه به بررسی موضوع مقاله پرداخته و دانش خود را در این حوزه ارتقا دهید. این مقاله بر اساس آخرین ژورنالهای صنعت فولاد گردآوری شده و تلاش شده که با بیان خلاصه و روان به موضوع پرداخته شود.
تولید زنجیر فولادی
زنجیر فولادی از جمله ابزارهایی است که از فولاد ساخته شده و به دلیل ویژگی هایی مانند استحکام بالا، مقاومت در برابر سایش و خوردگی، و دوام طولانی، کاربرد گسترده ای در صنایع مختلف دارد. این زنجیرها از حلقه های فولادی متصل به یکدیگر تشکیل شده اند و در انتقال نیرو، حمل بار یا اتصال بخش های گوناگون به کار گرفته می شوند. کاربرد اصلی زنجیرهای فولادی در صنایع سنگین، معدن، کشاورزی، حمل ونقل و ساخت وساز مشاهده می شود. همچنین، از این زنجیرها در تجهیزات مختلفی مانند جرثقیل ها، ماشین آلات کشاورزی، سیستم های انتقال مواد و ابزارهای باربری استفاده می شود. به لطف ساختار محکم و مقاوم خود، این زنجیرها توانایی تحمل وزن بالا، فشار شدید و شرایط سخت محیطی را دارا هستند. برای مشاهده ورق سیاه کلیک کنید. در این مقاله تولید زنجیر فولادی مورد بررسی قرار می گیرد.
ترکیب و خواص فولاد مورد استفاده زنجیر فولادی
در فرآیند تولید زنجیر فولادی، انتخاب نوع فولاد تأثیر مستقیمی بر کیفیت و ویژگی های نهایی محصول دارد. ترکیب شیمیایی فولاد باید به گونه ای انتخاب شود که خصوصیات مطلوبی همچون استحکام، انعطاف پذیری، مقاومت در برابر سایش و دوام بالا را برای زنجیر فراهم آورد. به همین منظور، فولاد زنجیر اغلب از آلیاژهای ترکیبی ساخته می شود که اساس آن آهن است، اما برای بهبود خواص آن، عناصر آلیاژی مختلفی نظیر کربن، منگنز، سیلیکون، کروم، نیکل و مولیبدن به ترکیب اضافه می شوند. کربن یکی از اصلی ترین عناصر آلیاژی مورد استفاده در فولاد است که مستقیماً بر استحکام آن تأثیر می گذارد. میزان کربن تعیین کننده سختی و مقاومت کششی فولاد است. فولادهای پرکربن استحکام و مقاومت به سایش بیشتری دارند، اما انعطاف پذیری کمتری از خود نشان می دهند. در تولید زنجیرهای فولادی معمولاً از فولادهای با کربن متوسط (در حدود ۰.۲ تا ۰.۶ درصد) استفاده می شود، زیرا این میزان تعادل مناسبی میان استحکام و انعطاف پذیری ایجاد می کند. منگنز نیز یکی دیگر از عناصر کلیدی در ترکیب فولاد است که علاوه بر افزایش استحکام، از تشکیل ترکیبات مضری نظیر گوگرد و فسفر جلوگیری کرده و باعث بهبود مقاومت ضد سایش و ضربه پذیری فولاد می شود. سیلیکون نقش مهمی در افزایش مقاومت فولاد در برابر اکسیداسیون و خوردگی ایفا می کند. این ویژگی به ویژه در مواقعی که زنجیر در معرض دمای بالا یا رطوبت قرار می گیرد اهمیت پیدا می کند. به طور مشابه، کروم و نیکل نیز موجب ایجاد خواص ضد زنگ و افزایش مقاومت در برابر خوردگی می شوند. برای زنجیرهایی که در محیط های خاصی همچون مکان های مرطوب یا اسیدی کاربرد دارند، حضور این عناصر ضروری است تا زنجیر بتواند دوام بیشتری داشته باشد. مولیبدن نیز جهت افزایش مقاومت فولاد در دماهای بالا و کاهش آسیب های ناشی از حرارت و سایش نقش قابل توجهی دارد. این قابلیت برای زنجیرهای صنعتی که در شرایط کاری دشوار همچون تجهیزات انتقال مواد داغ به کار می روند بسیار حائز اهمیت است. میزان و نوع دقیق ترکیب این عناصر، تعیین کننده ویژگی های مکانیکی و شیمیایی زنجیر است و بر این اساس طراحی هر نوع زنجیر براساس شرایط کاربردی خاص صورت می گیرد. زنجیرهای فولادی باید ویژگی هایی همچون استحکام بالا، مقاومت در برابر فرسایش، انعطاف پذیری مطلوب و قدرت جذب ضربه را دارا باشند. این زنجیرها باید قادر به تحمل بارهای سنگین و فشارهای شدید باشند و در عین حال به دلیل شوک ها یا فشارهای ناگهانی دچار شکستن یا ترک نشوند. مقاومت در برابر خوردگی و سایش نیز از دیگر مشخصاتی است که به ویژه در محیط های صنعتی با تماس مستقیم با رطوبت یا مواد خورنده اهمیت زیادی دارد. علاوه بر این، قابلیت تحمل دماهای بالا نیز از ویژگی های ضروری برای عملکرد مطمئن زنجیرها در محیط های صنعتی سخت یا شرایط با نوسانات دمایی زیاد است. سختی فولاد نیز باید به گونه ای باشد که ضمن حفظ مقاومت در برابر سایش، شکنندگی آن را به حداقل برساند. ترکیب دقیق آلیاژ فولاد باید توازنی مناسب میان سختی و انعطاف پذیری ایجاد کند تا محصول نهایی بتواند تمامی نیازهای عملیاتی در محیط های پیچیده صنعتی را برآورده کند. به طور کلی، زنجیر فولادی با ارائه ترکیبی از استحکام بالا، انعطاف پذیری مناسب، مقاومت در برابر سایش، خوردگی، ضربه و تحمل دماهای بالا باید عملکرد طولانی مدت خود را تضمین کند تا در کاربردهای مختلف صنعتی کارآمد باشد.
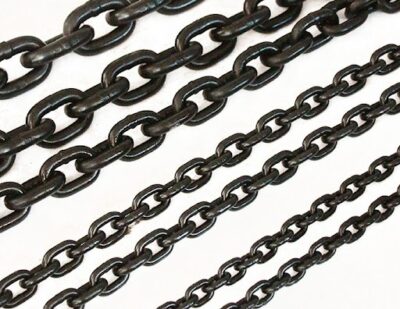
تولید زنجیر فولادی
فرآیند تولید زنجیر فولادی
فرآیند تولید زنجیر فولادی مجموعه ای از مراحل دقیق و فنی است که هدف آن تولید محصولی باکیفیت و بادوام برای کاربردهای مختلف صنعتی است. این فرآیند از انتخاب مواد اولیه آغاز و با تولید زنجیرهای با استحکام بالا به پایان می رسد. در ادامه، مراحل مختلف این فرآیند شرح داده شده است: اولین مرحله، انتخاب مواد اولیه مناسب است. فولاد خام به شکل میلگرد، سیم یا قطعات مشابه وارد کارخانه می شود. نوع فولاد باید از ویژگی های مکانیکی و شیمیایی مشخصی برخوردار باشد تا برای تولید زنجیر مناسب باشد. معمولاً فولادهای آلیاژی با درصدهای معین کربن و عناصر دیگر استفاده می شوند که ترکیبی از استحکام، انعطاف پذیری و مقاومت به سایش را تأمین می کنند. پس از تأمین مواد اولیه، فولاد وارد مرحله شکل دهی می شود. در این بخش، فولاد به حلقه های کوچک یا قطعات اولیه زنجیر تبدیل می شود. این کار عموماً با دستگاه های فورجینگ یا کشش انجام می گیرد که گاهی نیازمند گرمایش فولاد تا دمای بالا نیز هست تا فرآیند شکل دهی تسهیل شود. در مرحله بعد، حلقه ها با دقت زیادی برش داده شده و به اندازه ها و اشکال هندسی استاندارد تبدیل می شوند. این برش ها توسط دستگاه های پیشرفته ای صورت می گیرند که امکان دستیابی به ابعاد دقیق را فراهم می کنند. در برخی موارد، عملیات حرارتی مانند آنیلینگ یا تمپرینگ برای بهبود خواص مکانیکی حلقه ها انجام می شود. سپس، حلقه های آماده باید به هم متصل شوند تا زنجیر کامل شکل گیرد. روش اتصال ممکن است شامل جوشکاری، لحیم کاری یا حتی پیچش دستی باشد. در هر صورت، اتصال باید به گونه ای انجام گیرد که زنجیر تحت شرایط مختلف از استحکام کافی برخوردار باشد. مرحله بعدی مربوط به پرداخت سطح و عملیات نهایی زنجیر است. این بخش شامل اعمال پوشش های مقاوم به خوردگی مانند گالوانیزه کردن یا دیگر پوشش های محافظتی است. این کار علاوه بر محافظت سطح زنجیر در برابر زنگ زدگی، سبب افزایش طول عمر و کاهش اثرات مخرب محیطی مانند رطوبت و سایش می شود. در برخی موارد، عملیات پولیش نیز برای بهبود ظاهری و کاهش اصطکاک انجام می شود. در آخرین مرحله، زنجیر باید تحت آزمایش های کنترل کیفیت قرار گیرد. شامل بررسی های دقیق کشش، سایش، مقاومت به خوردگی و سختی است تا اطمینان حاصل شود که زنجیر تولید شده مطابق با استانداردهای صنعتی و بین المللی است. محصولات نهایی پس از موفقیت در آزمایش ها بسته بندی شده و برای ارسال به بازار آماده می شوند. به طور کلی، فرآیند تولید زنجیر فولادی ترکیبی از انتخاب مواد اولیه باکیفیت، استفاده از فناوری های مدرن در تولید و اجرای دقیق کنترل کیفیت است. نتیجه نهایی محصولی است که از لحاظ استحکام، دوام و مقاومت به خوردگی در بالاترین سطح قرار دارد و برای کاربردهای متنوع صنعتی مناسب است. برای مشاهده تیرآهن کلیک کنید.
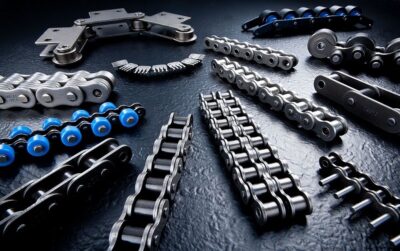
تولید زنجیر فولادی
انواع زنجیر فولادی
زنجیرهای فولادی به انواع گوناگونی تقسیم می شوند که هر کدام برای کاربردی خاص طراحی و تولید شده اند. این زنجیرها بسته به نیازهای صنعتی، شرایط محیطی و الزامات مختلف، ویژگی های متنوعی را ارائه می دهند. یکی از پرکاربردترین انواع، زنجیرهای صنعتی سنگین است که برای تحمل بارهای سنگین و فشار بالا طراحی شده اند. این زنجیرها را اغلب در صنایع سنگین مانند معدن، کشاورزی، حمل ونقل و ماشین آلات بزرگ می توان یافت. حلقه های آن ها ضخیم و مقاوم بوده و توانایی تحمل فشار زیاد را دارند. زنجیرهای انتقال قدرت نوع دیگری از زنجیر بوده و برای انتقال نیرو و حرکت در ماشین آلات مورد استفاده قرار می گیرند. این زنجیرها به ویژه در صنایع تولیدی و کشاورزی کاربرد بسیاری دارند. دقت در انتقال نیرو و جلوگیری از لغزش حلقه ها، ویژگی بارز این زنجیرهاست. به طور معمول، این زنجیرها به صورت یک طرفه یا دوطرفه ساخته می شوند و نقش مهمی در هدایت انرژی بین بخش های مختلف دستگاه ها ایفا می کنند. زنجیرهای فولادی ضد زنگ برای محیط های مرطوب یا حاوی مواد خورنده مناسب هستند. این زنجیرها که عمدتاً در صنایع غذایی، دارویی و شیمیایی به کار می روند، از جنس فولاد آلیاژی تهیه شده اند و مقاومت چشمگیری در برابر زنگ زدگی و خوردگی دارند؛ به همین دلیل، عملکرد بهتری در شرایط مرطوب نشان می دهند. زنجیرهای گالوانیزه نیز گزینه ای مناسب برای محیط های مرطوب یا مناطقی با رطوبت بالا هستند. فرآیند گالوانیزاسیون فولاد را با روکش روی پوشش می دهد تا از زنگ زدگی جلوگیری شود و مقاومت در برابر خوردگی افزایش یابد. این نوع زنجیرها در مناطقی که احتمال بارش باران زیاد وجود دارد یا شرایط مرطوب حاکم است، عملکرد مطلوب تری دارند. زنجیرهای باربری مخصوص حمل و نقل بارهای سنگین طراحی شده اند. این زنجیرها در بخش هایی مانند جرثقیل ها، بالابرها و تجهیزات بارگیری کاربرد دارند. حلقه های آن ها عموماً بزرگتر و مستحکم تر هستند تا توانایی تحمل بارهای سنگین و فشار ناگهانی را داشته باشند. مقاومت در برابر ضربات و کشش های شدید از مهم ترین ویژگی های آنها محسوب می شود تا فرآیند جابه جایی ایمن باشد. زنجیرهای کانوایر یا انتقال دهنده مواد، برای سیستم های تولیدی و خطوط انتقال مواد طراحی شده اند. این زنجیرها در صنایعی همچون تولید، بسته بندی و مواد غذایی بسیار رایج هستند. مقاومت بالا در برابر سایش و فشار همراه با انعطاف پذیری مناسب از الزامات اصلی این نوع زنجیر است که باعث حرکت روان آن ها در سیستم های با سرعت بالا می شود. زنجیرهای جابجایی سنگین که برای کاربردهای دشوارتر طراحی شده اند، بیشتر در صنایع فلزی، معدنی و نفت و گاز استفاده می شوند. حلقه های ضخیم این زنجیرها به گونه ای ساخته شده اند که فشارها و شرایط سخت را تاب آورند تا عملکرد مطلوب خود را حفظ کنند. زنجیرهای سیمی که از رشته های تابیده سیم فولادی تهیه می شوند، مقاومت بالایی در برابر کشش و فشار داشته و معمولاً در صنایع پل سازی، دریایی و سایر کاربردهای سنگین به کار می روند. این نوع زنجیرها به دلیل ترکیب مواد اولیه مقاوم، انتخاب ایده آلی برای محیط هایی با نیازهای فیزیکی بالا محسوب می شوند. زنجیرهای کشاورزی که به طور اختصاصی برای ماشین آلات کشاورزی تولید شده اند، مقاومت بالایی در برابر سایش، خوردگی و فشار دارند. از آنجا که این زنجیرها با خاک، آب، و مواد شیمیایی در تماس هستند، ساخته شدن آن ها از مواد بادوام امری ضروری است. معمول ترین استفاده آنها در دستگاه هایی مانند دروگرها و آسیاب هاست. در نهایت، زنجیرهای خودتنظیم که به عنوان یکی از پیشرفته ترین انواع شناخته می شوند، قابلیت روانکاری خودکار داشته و عموماً در صنایع شیمیایی، غذایی و ماشین آلات دقیق به کار می روند
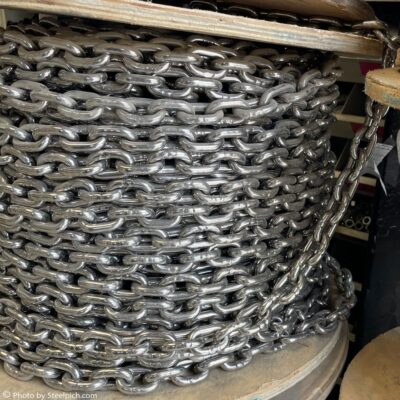
تولید زنجیر فولادی
روش های بهبود خواص زنجیر
برای بهبود خواص زنجیر فولادی و افزایش عملکرد آن در شرایط گوناگون، می توان از روش های متنوعی استفاده کرد. این روش ها شامل اصلاح ترکیب شیمیایی فولاد، بهره گیری از فرآیندهای حرارتی، پوشش دهی سطحی و تکنیک های پیشرفته دیگر است. در ادامه، به برخی از مهم ترین این روش ها پرداخته می شود: یکی از اصلی ترین راهکارها، تغییر ترکیب شیمیایی فولاد است. افزودن عناصری مانند کربن، منگنز، کروم، نیکل و مولیبدن می تواند خواصی نظیر استحکام، سختی، مقاومت به سایش و خوردگی را بهبود بخشد. مثلاً افزایش کربن موجب استحکام و سختی بیشتر می شود، هرچند که ممکن است انعطاف پذیری را کاهش دهد. در سوی دیگر، عناصری مانند کروم و نیکل مقاومت در برابر خوردگی و زنگ زدگی را بالا می برند، که برای محیط های مرطوب یا شیمیایی ایده آل است. استفاده از فرآیندهای حرارتی نیز از روش های موثر برای بهبود ویژگی های فولاد محسوب می شود. عملیاتی مانند آنیلینگ، تمپرینگ، کوئنچینگ و تردیفینگ می توانند ساختار فولاد را متناسب با نیازهای خاص تغییر دهند. برای مثال، کوئنچینگ که فرآیند سرد کردن سریع فولاد بعد از گرم کردن آن است، سختی را افزایش می دهد. از سوی دیگر، تمپرینگ که پس از کوئنچینگ انجام می شود، انعطاف پذیری و مقاومت به شکست را به فولاد اضافه می کند. پوشش دهی سطحی نیز نقش مهمی در افزایش عمر و خواص زنجیرهای فولادی دارد. تکنیک هایی مانند گالوانیزه کردن، پوشش دهی با کروم یا نیکل و استفاده از پوشش های پلیمری می توانند مقاومت در برابر خوردگی و سایش را به شدت افزایش دهند. این روش ها برای محیط های مرطوب یا خورنده بسیار مناسب هستند و دوام زنجیر را به شکل قابل توجهی بالا می برند. برای کاهش اصطکاک و افزایش عمر مفید، می توان از روانکارها و مواد ضدسایش استفاده کرد. این مواد معمولاً روی سطح یا داخل حلقه های زنجیر اعمال می شوند تا اصطکاک و سایش قطعات کاهش یابد. این روش به ویژه در شرایطی که زنجیر در سرعت بالا یا تحت فشار زیاد کار می کند، اثربخش است. در تکنیک های نوین تر، استفاده از پوشش های نانو می تواند خواص سطحی زنجیر را بیشتر بهبود بخشد. این پوشش ها علاوه بر افزایش مقاومت در برابر خوردگی و سایش، به کاهش اصطکاک نیز کمک می کنند و بیشتر در صنایع پیشرفته ای مثل هوافضا و خودروسازی کاربرد دارند. از دیگر روش های مؤثر می توان به فرآیند فورجینگ اشاره کرد که موجب تنظیم بهتر ساختار دانه ای فولاد می شود و در نتیجه استحکام، مقاومت به سایش و انعطاف پذیری آن تقویت می شود. همچنین سردکاری و کشش سرد از جمله تکنیک هایی هستند که امکان شکل دهی دقیق به فولاد در دماهای پایین را فراهم کرده و موجب افزایش دقت ابعادی و سفتی ماده می شوند. در نهایت، طراحی مناسب زنجیر و استفاده از مواد اولیه با کیفیت از مراحل ابتدایی تولید تا فرآیندهای نهایی اهمیت بسیاری دارد. انتخاب نوع مناسب فولاد و تنظیم صحیح فرآیندها بر اساس نیازهای کاربردی زنجیر، نقش مهمی در دستیابی به کارایی و عمر مفید بالای محصول ایفا می کند. با بهره گیری هوشمندانه از این روش ها می توان زنجیرهای فولادی با عملکرد بالا تولید کرد که توانایی مقاومت در برابر سایش، خوردگی، فشار و دماهای بالا را داشته باشند و عمر مفید طولانی تری ارائه دهند. برای مشاهده پروفیل ساختمانی کلیک کنید.
آزمایش ها و کنترل کیفیت
فرآیند آزمایش و کنترل کیفیت بخش کلیدی در تولید زنجیر فولادی است و تضمین می کند که محصول نهایی از لحاظ استحکام، دوام و عملکرد در شرایط مختلف، با استانداردهای صنعتی و نیازهای کاربردی کاملاً انطباق داشته باشد. برای تحقق این اهداف، مجموعه ای از آزمایش ها و فرآیندهای کنترل کیفیت در مراحل مختلف تولید و پیش از تحویل به مشتری انجام می شود. ابتدایی ترین مرحله کنترل کیفیت، انجام آزمایش های شیمیایی جهت بررسی ترکیب مواد اولیه است. این آزمایش ها برای اطمینان از انطباق ترکیب شیمیایی فولاد (مانند درصد عناصر کربن، منگنز، نیکل و کروم) با مشخصات فنی ضروری هستند. ابزارهایی نظیر طیف سنج جذب اتمی (AAS) یا فناوری ICP برای تحلیل این ترکیبات مورد استفاده قرار می گیرند. پس از تعیین ترکیب شیمیایی، نوبت به آزمایش های مکانیکی می رسد. این دسته از آزمایش ها نقاط قوت فیزیکی و مکانیکی فولاد همچون مقاومت در برابر فشار، کشش و سایش را ارزیابی می کنند. نمونه بارز این آزمایش ها، تست کشش است که در آن میزان استحکام کششی فولاد سنجیده می شود تا توانایی تحمل تنش های کاری عملیاتی ارزیابی شود. این آزمایش با کمک دستگاه های کشش دقیقی انجام می گیرد که داده های مهمی درباره شکست ماده و ظرفیت آن تحت بار کششی فراهم می آورند. آزمایش سختی نیز از دیگر مراحل اساسی فرآیند کنترل کیفیت است که مقاومت فولاد در برابر فرورفتگی و سایش را بررسی می کند. روش های متداولی مانند برینل، راکول یا ویکرز برای انجام این آزمایش ها به کار گرفته می شوند. نتایج حاکی از سختی بالای فولاد نشان دهنده مقاومتی است که از خرابی زودهنگام زنجیرها جلوگیری می کند. همچنین آزمایش مقاومت به سایش زنجیر فولادی نقش مهمی در ارزیابی دوام آن در برابر فرسایش دارد. این آزمایش ها با دستگاه هایی انجام می شوند که شرایط سایشی مطابق با محیط عملیاتی را شبیه سازی می کنند. داده های حاصل از این ارزیابی ها شامل نرخ کاهش ضخامت و کمیت ذرات ساییده شده است که به عملکرد کلی زنجیر کمک می کنند. یکی دیگر از مراحل حیاتی در کنترل کیفیت، آزمایش مقاومت به خوردگی است که عمدتاً برای زنجیرهایی که در محیط های مرطوب یا خورنده به کار می روند، طراحی شده است. این مرحله شامل تست هایی مانند غوطه وری در محلول های خورنده، پاشش نمک یا بخار آب است. هدف این آزمایش ها بررسی تأثیر شرایط محیطی بر کیفیت و ماندگاری زنجیر است. علاوه بر روش های فوق، تست های غیرمخرب نیز برای بررسی نقص های احتمالی داخلی، ترک ها یا حفرات ناشی از مرحله تولید انجام می شوند. این آزمایش ها مانند اولتراسونیک، جریان گردابی یا تست مغناطیسی، بدون آسیب رساندن به نمونه، ایرادهای نهان را تشخیص داده و نقش اساسی در تضمین کیفیت محصول دارند. برای بازبینی دقیق تر عملکرد زنجیر فولادی، آزمایش هایی تحت شرایط متفاوت از نظر دما، رطوبت و فشار اجرا می شود که تأثیرات این عوامل را بر کارایی و عمر مفید زنجیر مشخص می کنند. در نهایت، فرآیند تولید زنجیر فولادی تحت نظارت مستمر کنترل کیفیت قرار دارد. این کنترل شامل بررسی دقیق ابعاد هندسی زنجیر برای تطابق با نقشه های مهندسی است. ابزارهایی نظیر میکرومتر، کالیپر و دستگاه های دیجیتال اندازه گیری نیز به این منظور استفاده می شوند. به طور کلی، فرآیند آزمایش و کنترل کیفیت ترکیبی از بررسی های شیمیایی، مکانیکی و فیزیکی است که هدف آن تضمین تطابق محصول نهایی با معیارهای استاندارد است. اهمیت ویژه این فرآیند به این دلیل است که زنجیرهای فولادی معمولاً تحت شرایط سخت عملیاتی استفاده می شوند و وجود هرگونه نقص یا مشکل کیفی ممکن است باعث خرابی سیستم های صنعتی گردد. در این مقاله تولید زنجیر فولادی مورد بررسی قرار گرفت.