فرایند تولید پروفیل صنعتی
در این مقاله به فرایند تولید پروفیل صنعتی پرداخته می شود و به شما کمک می کند که در زمان بسیار کوتاه به بررسی موضوع مقاله پرداخته و دانش خود را در این حوزه ارتقا دهید. این مقاله بر اساس آخرین ژورنالهای صنعت فولاد گردآوری شده و تلاش شده که با بیان خلاصه و روان به موضوع پرداخته شود.
فرایند تولید پروفیل صنعتی
پروفیلهای صنعتی به قطعات فلزی با مقاطع ویژه و مشخصات دقیق گفته میشود که عمدتاً در صنایع مختلف برای ساخت سازهها، تجهیزات و ماشینآلات به کار میروند. این پروفیلها معمولاً از مواد مختلفی مثل آلومینیوم، فولاد، مس یا آلیاژها ساخته میشوند و در طرحهای متنوعی چون پروفیلهای باز، بسته یا پیچیده طراحی میگردند. هدف اصلی از مصرف پروفیلهای صنعتی، تأمین نیازهای مهندسی و طراحی پروژههاست، بهگونهای که این قطعات با مشخصات فنی دقیق تولید و مورد استفاده قرار میگیرند. به دلیل ویژگیهایی چون استحکام بالا، وزن سبک (به ویژه در آلومینیوم)، قابلیت شکلدهی، مقاومت بالا در برابر خوردگی و طول عمر زیاد، پروفیلهای صنعتی در بسیاری از صنایع نقش حیاتی دارند. از جمله کاربردهای این پروفیلها میتوان به صنعت ساخت و ساز، خودروسازی، لوازم خانگی، تجهیزات صنعتی، صنایع برق و الکترونیک، بستهبندی و بسیاری دیگر اشاره کرد. آنها به خصوص برای ساخت قابها، سازههای فلزی، سیستمهای تهویه، ماشینآلات و تجهیزات پیچیده صنعتی به کار گرفته میشوند. در فرآیند تولید پروفیلهای صنعتی از تکنیکهایی مانند ریختهگری، اکستروژن، نورد و برش استفاده میشود تا به شکل و ابعاد دقیق مورد نیاز برسند. این فرآیندها باید با دقت و براساس نیازهای ویژه هر صنعت انجام شوند تا پروفیلها ویژگیهایی نظیر استحکام، انعطافپذیری، مقاومت به خوردگی و ظاهر دلخواه را داشته باشند. مقاله پیش رو به بررسی فرآیند تولید پروفیلهای صنعتی و نقش آنها در صنایع مختلف میپردازد. در این مقاله به فرایند تولید پروفیل صنعتی پرداخته می شود.
انتخاب مواد اولیه در فرایند تولید پروفیل صنعتی
انتخاب مواد اولیه یکی از مراحل مهم در تولید پروفیلهای صنعتی است که به شدت بر کیفیت محصول نهایی و کارایی آن در کاربردهای مختلف اثرگذار است. این مواد باید به گونهای انتخاب شوند که علاوه بر داشتن ویژگیهای فنی مطلوب، از لحاظ اقتصادی نیز مقرونبهصرفه باشند. در این مرحله، باید عوامل متعددی مورد ارزیابی قرار گیرند تا مواد اولیه با ویژگیهای مناسب انتخاب شده و منجر به تولید پروفیلهایی با کیفیت بالا شوند. یکی از اصلیترین عوامل در انتخاب مواد اولیه، ویژگیهای فنی ماده است. این ویژگیها شامل مقاومت کششی، استحکام، انعطافپذیری، مقاومت در برابر خوردگی و دماهای متفاوت، و نیز خصوصیات الکتریکی و حرارتی میشود. معمولاً، آلومینیوم و فولاد به عنوان مواد پرمصرف برای تولید پروفیلهای صنعتی شناخته شدهاند که هر کدام ویژگیهای اختصاصی خود را دارند. مثلاً، آلومینیوم به سبب سبکی وزن، قابلیت شکلدهی ساده و مقاومت خوب در برابر خوردگی در صنایع متعدد کاربرد دارد. فولاد، به خاطر استحکام بالا و مقاومت بیشتر در برابر فشار و تنش، معمولاً در صنایع سنگین و ساختوساز استفاده میشود. علاوه بر ویژگیهای فنی، جنبههای اقتصادی نیز در انتخاب مواد اولیه مهم هستند؛ زیرا هزینه آنها میتواند بر قیمت نهایی پروفیل تأثیر بگذارد. بنابراین، تولیدکنندگان باید میان هزینه و کیفیت تعادل مناسبی برقرار کنند. برای نمونه، فولاد اغلب قیمت کمتری نسبت به آلومینیوم دارد اما با توجه به ویژگیهای خاص آلومینیوم، ممکن است در بسیاری از صنایع گزینه بهتری باشد. توانایی دسترسی و منابع نیز از عوامل کلیدی در انتخاب مواد اولیه محسوب میشود. مهم است که مواد اولیه از منابع معتبر تامین گردیده و به راحتی در دسترس باشند تا تولید پروفیلها بدون وقفه پیش رود، بهخصوص در مقیاسهای بزرگ یا هنگام تولید انبوه. ویژگیهای زیستمحیطی و پایداری مواد اولیه نیز تأثیرگذار هستند. توجه به مسائل زیستمحیطی امروز بسیار اهمیت یافته است؛ لذا انتخاب موادی که قابل بازیافت بوده و آسیب کمتری به محیط زیست میرسانند، بسیار مهم است. آلومینیوم با قابلیت بازیافت بالا، محبوبیت زیادی در صنایع مختلف به ویژه تولید پروفیلهای صنعتی دارد. در نهایت، نیازهای ویژه هر صنعت در انتخاب مواد اولیه بیتاثیر نیستند. برای مثال، صنعت خودروسازی از پروفیلهای آلومینیومی به دلیل سبکی وزن و مقاومت خوردگی استفاده میکند، ولی در ساختمانسازی ممکن است پروفیلهای فولادی به دلیل استحکام بیشتر و قابلیت تحمل بارهای سنگین ترجیح داده شوند. به طور کلی، انتخاب مواد اولیه برای تولید پروفیلهای صنعتی مستلزم ارزیابی دقیق ویژگیهای فنی، اقتصادی، زیستمحیطی و نیازهای خاص هر صنعت است تا محصول نهایی با کیفیت عالی، عملکرد مطلوب و هزینه مناسب تولید شود.
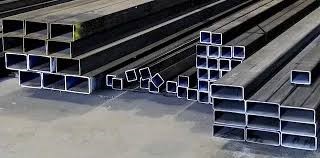
فرایند تولید پروفیل صنعتی
فرآیند ذوب و ریخته گری پروفیل صنعتی
فرآیند ذوب و ریختهگری یکی از مراحل اساسی در تولید پروفیلهای صنعتی است که در آن مواد اولیه به حالت مذاب درآمده و پس از آن به قالبهای مشخص ریخته میشوند تا شکل اولیه پروفیلها ایجاد شود. در این مرحله، فلزات خام یا آلیاژها در کورههای صنعتی ذوب میشوند تا به دمای مذاب دست یابند. این دما بسته به نوع ماده اولیه متغیر است؛ مثلاً، دمای ذوب آلومینیوم حدود ۶۶۰ درجه سانتیگراد و فولاد معمولاً در حدود ۱۴۵۰ درجه سانتیگراد است. برای ذوب از کورههای القایی، کورههای قوس الکتریکی یا کورههای سوختی استفاده میگردد، که میتوانند دمای بالای فلز مذاب را تحمل نمایند. در برخی مواقع برای بهبود کیفیت فلز و تنظیم ترکیب شیمیایی آن از گازهای محافظ یا پودرهای آلیاژی استفاده میشود. پس از ذوب شدن فلزات، فلز مذاب به قالبهای خاص منتقل میشود. این قالبها عمدتاً از جنس فولاد یا چدن و مقاوم در برابر حرارت هستند. در فرآیند ریختهگری، قالبها به گونهای طراحی میشوند که پروفیلها به شکل مطلوب خود درآیند. قالبها میتوانند به روش دایکست (ریختهگری تحت فشار) یا وکیوم ساخته شوند. در دایکستینگ، فلز مذاب با فشار تزریق میشود تا شکل دقیقتری حاصل شود، در حالی که در ریختهگری وکیوم، فرآیند در فضای خلاء انجام شده که به حداقل رساندن حبابهای هوا و ناخالصیهای فلز کمک میکند. پس از ریختن فلز مذاب در قالب، فلز شروع به سرد شدن و انجماد میکند. این فرآیند اغلب در اتاقهای خنککننده یا در آب سرد انجام میشود تا فلز به سرعت از حالت مایع به جامد تبدیل شود. سرعت سرد شدن تأثیر زیادی بر خواص پروفیلها دارد. اگر سرعت بیش از حد بالا باشد، ممکن است منجر به تشکیل ترکیبات نامطلوب یا کاهش استحکام محصول شود. پس از انجماد، پروفیلها با استفاده از ابزارهای مکانیکی یا هیدرولیکی از قالب خارج میشوند. گاهاً نیاز به اصلاح اضافی برای حذف بخشهای زائد وجود دارد. پروفیلها پس از این مراحل تحت آزمایشهای مختلف قرار میگیرند تا از دقت ابعادی و استحکام آنها اطمینان حاصل شود. این آزمایشها شامل تستهای کششی، فشاری، مقاومت به خوردگی و بررسی دقت ابعادی هستند. در نهایت، پروفیلهای نهایی برای مراحل بعدی مانند پرداخت سطح، عملیات حرارتی و بستهبندی آماده میشوند. فرآیند ذوب و ریختهگری نقش کلیدی در کیفیت نهایی پروفیلها دارد و کنترل دقیق دما، سرعت ریختهگری و نحوه سرد کردن بر ویژگیهای نهایی پروفیلها موثر است. برای مشاهد ورق سیاه کلیک کنید.
اکستروژن و نورد پروفیل صنعتی
فرآیندهای اکستروژن و نورد از جمله روشهای متداول برای تولید پروفیلهای صنعتی هستند که در این فرآیندها، مواد اولیه تحت فشار یا حرارت قرار میگیرند تا به شکلهای دلخواه تبدیل شوند. این دو روش بخصوص برای تولید پروفیلهای فلزی مانند آلومینیوم، فولاد، مس و دیگر آلیاژها کاربرد دارند و بهطور گسترده در صنایع مختلف مانند خودروسازی، ساختمانسازی، لوازم خانگی و صنایع برق و الکترونیک مورد استفاده قرار میگیرند. در فرآیند اکستروژن، ماده اولیه که معمولاً به شکل شمش یا بیلت است، به داخل قالب مخصوصی فشرده میشود. این قالب دارای یک یا چند مقطع مشخص است که پروفیل نهایی از آن گذر میکند. در طی این فرآیند، ماده اولیه تحت دمای بالا و فشار قرار دارد و به آرامی از قالب خارج میشود. اکستروژن برای تولید پروفیلهای آلومینیومی رایج است زیرا آلومینیوم قابلیت مناسبی برای تغییر شکل تحت فشار دارد و منجر به تولید پروفیلهایی با دقت ابعادی بالا و خواص مکانیکی مطلوب میشود. اکستروژن بهطور کلی برای پروفیلهای بلند و مقاطع پیچیده بهکار میرود که شامل شکلهای دایرهای، مربعی، مستطیلی و حتی مقاطع خاصتر مانند سهگوش یا پنجگوش هستند. در فرآیند نورد، مواد اولیه به صورت شمش یا ورق فلزی وارد دستگاه نورد میشوند. فلز از میان یک یا چند جفت غلتک عبور داده میشود که در فاصله معینی قرار گرفتهاند. این فرآیند ممکن است در دماهای بالا (نورد گرم) یا دماهای پایین (نورد سرد) انجام شود و هدف آن کاهش ضخامت فلز و افزایش طول آن است. در نورد گرم، فلز تحت دمای بالا قرار میگیرد تا شکلپذیری آن بهبود یابد؛ در حالی که در نورد سرد، فلز در دماهای پایینتر نورد میشود تا استحکام آن افزایش یابد. نورد گرم معمولاً برای تولید پروفیلهای فولادی و مقاطع بزرگ مناسب است و نورد سرد برای تولید ورقهای نازکتر با دقت ابعادی بالاتر کاربرد دارد. این دو فرآیند ویژگیهایی مانند استحکام، سختی و انعطافپذیری فلز را تعیین میکنند. برای مثال، در اکستروژن، فشار و دمای وارد شده به ماده اولیه ساختار میکروسکوپی پروفیلهای نهایی را متأثر میکنند؛ در مقابل، در نورد، میزان فشاری که از طریق غلتکها وارد میشود، خواص مکانیکی محصول نهایی را تغییر میدهد. در مجموع، اکستروژن بیشتر برای تولید پروفیلهای پیچیدهتر با مقاطع خاص و طول بلند مناسب است؛ در حالی که نورد بیشتر برای مقاطع با ضخامت یکنواخت و طولهای بزرگتر استفاده میشود. هر دو فرآیند دارای مزایای ویژهای هستند و انتخاب بین آنها بر اساس نوع پروفیل مورد نظر و نیازهای خاص تولید انجام میشود.
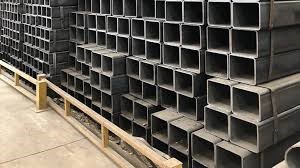
فرایند تولید پروفیل صنعتی
سرد کردن و عملیات حرارتی پروفیل صنعتی
فرآیند سرد کردن و عملیات حرارتی پس از مراحل تولید پروفیلهای صنعتی حالتی ضروری یافته است. این فرآیندها که بعد از ذوب، ریختهگری، اکستروژن و نورد انجام میشوند، برای بهبود ویژگیهای فیزیکی و مکانیکی مواد کاربرد دارند. در تولید پروفیلهای فلزی مانند آلومینیوم، فولاد و مس، این مراحل نقش مهمی در افزایش استحکام، سختی، انعطافپذیری و مقاومت به خوردگی دارند. سرد کردن یا خنکسازی به کاهش دمای مواد تا سطح مشخص اشاره دارد. این عملیات معمولاً بعد از شکلدهیهایی مانند ریختهگری، اکستروژن یا نورد اجرا میشود. روش سرد کردن سریع ویژگیهایی نظیر استحکام، ساختار دانهای و سختی فلز را تحت تأثیر قرار میدهد. تکنیکهای متداول سرد کردن شامل آبکشی هستند که در آن فلز مذاب یا گرم سریعاً در آب یا محلولهای دیگر قرار میگیرد. این فرآیند سرعت کاهش دما را افزایش میدهد و از تغییرات ناخواسته در ساختار فلز جلوگیری میکند. برای نمونه، در فولاد، سرد کردن سریع به تشکیل ساختار مارتنزیتی و افزایش استحکام منجر میشود. عملیات حرارتی شامل مجموعهای از فرآیندهای کنترلشده است که قطعه فلزی به دمای خاصی رسانده میشود و سپس به طرز معینی سرد میگردد. آنیل کردن، تیمار حرارتی، سخت کردن و بازپخت جزو این فرآیندها هستند. هدف اصلی عملیات حرارتی، بهبود خواص فلزات همانند استحکام، انعطافپذیری و سختی و کاهش تنشهای داخلی ایجاد شده در مراحل پیشین نام برده شده مثل نورد یا ریختهگری است. در فرآیند آنیل کردن، فلز به دمای مشخصی که بسته به نوع فلز متفاوت است، گرم شده و به آرامی سرد میشود. این اقدام باعث بهبود ساختار دانهای فلز شده، استحکام و انعطافپذیری را افزایش داده و تنشهای داخلی را کاهش میدهد. در فولاد، این فرآیند معمولاً برای افزایش انعطافپذیری و کاهش سختی استفاده میشود. تیمار حرارتی با گرم کردن فلز تا دمای معین و سپس سرد کردن سریع آن شناخته میشود. معمولاً در فولادها و آلیاژهای مرتبط آن کاربرد داشته تا ویژگیهایی مثل استحکام و سختی بیشتر شود. در فرآیند سختکردن فولاد، فلز به دمای بالا رسیده و سپس سریعاً در آب یا روغن خنک میشود تا سختی و مقاومت به سایش افزایش یابد. بازپخت یا ریکریستالیزاسیون نیز از فرآیندهای عملیات حرارتی است که هدف آن بهبود ویژگیهای مکانیکی و کاهش تنشهای داخلی ناشی از نورد سرد بوده. این فرآیند با گرم کردن قطعه فلزی تا دمای مشخص و سپس سرد کردن کنترلشده آن، ساختار دانهای فلز را تغییر داده و خواص را بهتر میکند. در پایان، فرایندهای سرد کردن و عملیات حرارتی تأثیر مستقیمی بر خواص نهایی پروفیلها و قطعات صنعتی دارند. این عملیاتها میتوانند ویژگیهایی مانند استحکام، سختی، انعطافپذیری و مقاومت به خوردگی را بهبود بخشیده و طول عمر و عملکرد قطعات را در کاربردهای صنعتی متنوع افزایش دهند. برای مشاهده تیرآهن کلیک کنید.
برش و شکل دهی نهایی پروفیل
پس از مراحل اولیه تولید پروفیلهای صنعتی مانند ذوب، ریختهگری، اکستروژن یا نورد، مرحله بعد برش و شکلدهی نهایی است. این مرحله برای دستیابی به ابعاد دقیقتر، اصلاح شکل و حذف بخشهای اضافی پروفیلها انجام میشود. علاوه بر این، ویژگیهای ظاهری و عملکردی پروفیلها نیز در این مرحله بهبود مییابد. در فرآیند برش، پروفیلها به اندازههای دقیقی که برای کاربردهای خاص لازم است، برش داده میشوند. برش معمولاً با ماشینآلات خاصی مانند برش مکانیکی، لیزر، یا واترجت انجام میشود. برشهای مکانیکی شامل استفاده از ارههای مخصوص یا تیغههای برشی است که پروفیلها را به طولهای مورد نظر تقسیم میکنند. برش لیزری برای ایجاد برشهای دقیق و تمیزی به کار میرود و از پرتو لیزر برای برش فلزات به شکلهای پیچیده استفاده میکند. واترجت نیز با جت آب فشار بالا و مواد ساینده، برشهای تمیز و دقیق روی فلزات ایجاد میکند. پس از برش، شکلدهی نهایی پروفیلها انجام میشود. این مرحله شامل فرآیندهایی است که پروفیلها را شکل نهایی و مطلوب برای استفاده در صنایع مختلف میدهد. ممکن است پروفیلها تحت خمکاری، فشار دادن، کشیدن یا منحنیسازی قرار بگیرند. این عملیاتها کمک میکند تا پروفیلها به ابعاد و شکلهای مورد نظر دقیقاً برسند. در خمکاری، پروفیلهای فلزی با نیروی خاصی خم میشوند تا به شکل دلخواه درآیند؛ این روش برای ساخت پروفیلهایی با زاویههای خاص یا انحنای مشخص کاربرد دارد. در ساختمانسازی، پروفیلهای فولادی معمولاً خمکاری میشوند تا در سازهها استفاده شوند. فشار دادن به مواد اولیه برای دستیابی به شکلهای خاص با استفاده از فشار انجام میشود. این فرآیند مخصوص تولید مقاطع بلند و با اشکال خاص است. در کشیدن، پروفیلهای فلزی از میان قالبها یا دیافراگمها عبور داده میشوند تا به شکلهای نازکتر و دقیقتر تبدیل شوند؛ این فرآیند برای تولید پروفیلها با مقاطع مشخص و طول زیاد کاربرد دارد. این مرحله از تولید نه تنها به شکلدهی دقیق پروفیلها کمک میکند بلکه دقت ابعادی را ارتقا داده، ضایعات را کاهش میدهد و کیفیت بالاتر محصولات نهایی را تضمین میکند. در نهایت، پروفیلها آماده استفاده در صنایع مختلف مانند ساختمانسازی، خودروسازی، لوازم خانگی و صنایع برق و الکترونیک هستند.
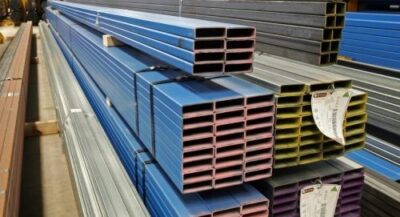
فرایند تولید پروفیل صنعتی
پرداخت و تمیزکاری پروفیل صنعتی
پس از اجرای مراحل اصلی تولید پروفیلهای صنعتی مانند برش و شکلدهی نهایی، عملیات پرداخت و تمیزکاری برای بهبود کیفیت سطح پروفیلها انجام میشود. این مرحله از اهمیت ویژهای برخوردار است؛ چرا که به طول عمر بیشتر و عملکرد بهتر پروفیلها در کاربریهای مختلف صنعتی کمک میکند. بسته به نوع ماده و نیازهای خاص، فرآیند پرداخت و تمیزکاری میتواند به روشهای مختلفی انجام شود. پرداخت سطحی معمولاً برای دستیابی به ظاهری صاف و بدون نقص صورت میگیرد. این فرآیند شامل مواردی مانند سنبادهزنی، پولیش کردن، شات بلاست یا لایهگذاری است. در سنبادهزنی، از ابزارهایی برای حذف لایههای اضافی و خطوط ناپیوسته استفاده میشود تا سطحی نرمتر و زیباتر ایجاد شود. پولیش کردن به فرآیندی اطلاق میشود که در آن از مواد ساینده و تجهیزات ویژه برای ایجاد سطوح براق استفاده میشود. این تکنیک معمولاً بر روی فلزاتی مانند آلومینیوم، مس و فولاد ضد زنگ اعمال میشود تا علاوه بر زیبایی، مقاومت در برابر خوردگی را نیز افزایش دهد. شات بلاست یکی دیگر از روشهای پرکاربرد تمیزکاری است که در آن فلزات با برخورد گلولههای فولادی یا سایر سایندهها صیقلی میشوند. این روش برای پروفیلهای بزرگتر یا قطعاتی که دچار زنگزدگی یا آلودگی شدهاند، مناسب است و مقاومت پروفیلها در برابر خوردگی را افزایش میدهد. در فرآیند لایهگذاری، سطح پروفیل با فلزات مختلف مانند کروم، نیکل یا روی پوشانده میشود که باعث افزایش مقاومت در برابر خوردگی و سایش میگردد. این عملیات علاوه بر بهبود ظاهر، ویژگیهای حفاظتی بهتری را نیز فراهم میکند. تمیزکاری برای حذف آلودگیها، روغن یا مواد شیمیایی باقیمانده از مراحل قبلی مانند برش و نورد ضروری است. استفاده از روشهای شستشو با مواد شیمیایی، بخار یا آب گرم برای تضمین کیفیت سطح و اطمینان از عدم تأثیر منفی این مواد روی پروفیلها انجام میشود. در صورتی که قرار باشد پروفیلها با روکشهای خاص پوشانده شوند، تمیزکاری دقیق برای اطمینان از چسبندگی مناسب پوششها اهمیت دارد. این مرحله نه تنها به بهبود ظاهر و کیفیت پروفیلها کمک میکند، بلکه بر ویژگیهای عملکردی و مقاومت به خوردگی آنها نیز تأثیر بسزایی دارد. به طور کلی، پرداخت و تمیزکاری یک بخش ضروری در تولید پروفیلهای صنعتی با کیفیت بالا است که نیازهای متنوعی از جمله خودروسازی، ساختمانسازی و صنایع الکترونیک را پاسخگوست. برای مشاهده پروفیل ساختمانی کلیک کنید.
کنترل کیفیت در فرایند تولید پروفیل صنعتی
مرحله کنترل کیفیت یکی از اجزای کلیدی و اساسی در فرآیند تولید پروفیلهای صنعتی است که با هدف اطمینان از انطباق محصولات نهایی با استانداردها و نیازهای صنعتی انجام میشود. اهمیت بالای این مرحله از آنجا ناشی میشود که هرگونه نقص یا خطا در پروفیلها میتواند منجر به مشکلات قابلتوجهی در کاربردهای نهایی شده و عمر مفید قطعات را کاهش دهد. این فرآیند عموماً شامل آزمایشهای فنی، بررسیهای ظاهری و اندازهگیریهای دقیق است. آزمایشهای فیزیکی و مکانیکی برای ارزیابی استحکام، سختی و انعطافپذیری پروفیلها انجام میشوند. این آزمایشها با استفاده از دستگاههایی نظیر تجهیزات تست کشش و سختیسنج عملیاتی میگردند. در آزمایش کشش، نمونهها تحت نیروی کششی قرار میگیرند تا میزان نیرو یا تغییر شکلی که باعث شکست یا تغییر شکل دائمی میشود، مشخص شود. این اطلاعات نقش مهمی در تشخیص کیفیت فلز یا آلیاژ مورد استفاده ایفا میکند. همچنین، میزان سختی پروفیلها با روشهایی چون تستهای راکول یا ویکرز اندازهگیری شده و مقاومت سطح در برابر فرسایش ارزیابی میگردد. آزمایشهای ابعادی نیز بخش حیاتی دیگری از کنترل کیفیت هستند. در این مرحله، دقت ابعاد پروفیلها مانند ضخامت، طول، عرض و زوایا بررسی میشود تا تطابق آنها با مشخصات طراحی تضمین گردد. ابزارهایی مانند گیج، کالیپر یا دستگاههای پیشرفته نظیر مختصات سهبُعدی (CMM) برای انجام این اندازهگیریها به کار گرفته میشوند و توانایی ثبت دقیق انحرافات احتمالی را دارا هستند. آزمایشهای شیمیایی به منظور بررسی ترکیب شیمیایی مواد اولیه انجام شده و تأمین تطابق آلیاژها با استاندارد تعریفشده را تضمین میکنند. روشهایی مثل آنالیز فلورسانس اشعه ایکس یا طیفسنجی جرمی برای بررسی دقیق ترکیبات فلزات مورد استفاده قرار گرفته و از کیفیت مواد اولیه اطمینان حاصل میشود. کنترل کیفیت سطح پروفیلها نیز بخش دیگری از این فرآیند است که برای تشخیص معایب ظاهری یا داخلی مانند ترک، حباب یا سایر نواقص صورت میگیرد. این بررسیها از طریق روشهایی چون تست مایعات نفوذی، التراسونیک یا حتی بررسی بصری انجام شده و به عملکرد بهینه پروفیلها کمک میکند. آزمایش مقاومت به خوردگی نیز مرحلهای کلیدی است که طی آن پروفیلها در شرایط خاصی مثل تست نمکپاشی یا رطوبت قرار گرفته و مقاومت آنها در برابر عوامل محیطی نظیر خوردگی ارزیابی میشود. این آزمایشها بویژه برای کاربردهایی در صنایع نفت، گاز، ساختوساز یا خودروسازی که شرایط محیطی دشوار هستند، الزامی محسوب میشوند. ثبت و مستندسازی تمامی مراحل آزمایشها بخش مهم دیگری از کنترل کیفیت است. نتایج ثبتشده اطمینان میدهند که فرآیند تولید قابل پیگیری بوده و امکان رجوع به آنها برای تحلیل مشکلات آینده وجود دارد. در نهایت، فرآیند کنترل کیفیت نه تنها امکان شناسایی مشکلات احتمالی و جلوگیری از بروز نقص را فراهم میکند، بلکه به تولید محصولاتی باکیفیت بالا کمک کرده و ضمن کاهش ضایعات و افزایش رضایت مشتریان، عمر مفید محصولات را نیز افزایش میدهد.
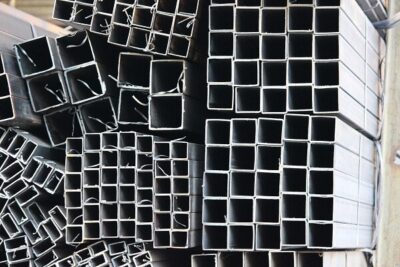
فرایند تولید پروفیل صنعتی
مراحل بسته بندی و ارسال پروفیل
فرایند تولید پروفیل صنعتی در مراحل بسته بندی و ارسال پروفیل نیز جاری است. پس از پایان تولید پروفیلهای صنعتی و تایید کیفیت آنها از طریق مراحل کنترل، فرآیند بستهبندی و ارسال آغاز میشود. این مرحله از اهمیت ویژهای برخوردار است زیرا بستهبندی مناسب میتواند از آسیبدیدگی محصول در طول حملونقل و ذخیرهسازی جلوگیری کند و تضمین نماید که پروفیلها در شرایط مطلوب به مقصد نهایی میرسند. علاوه بر آن، بستهبندی نقش تبلیغاتی برای برند و شرکتها دارد. پس از تایید کیفیت پروفیلها، آمادهسازی دقیق آنها برای بستهبندی الزامی است. این شامل حذف مواد زائد مانند برچسبهای اضافی، قطعات برشخورده یا هرگونه آلودگی است که ممکن است به محصول آسیب برساند. برای اطمینان از این که پروفیلها در بهترین شرایط به بستهبندی منتقل شوند، گاهی اوقات از فرآیندهایی مثل تمیزکاری نهایی و آبکاری استفاده میشود. در این مرحله، پروفیلها معمولاً در بستهبندیهای اولیه مانند کیسههای پلاستیکی، فویلهای محافظ، یا پوششهای نایلونی قرار داده میشوند. این پوششها کمک میکنند تا محصول در برابر رطوبت، گردوغبار و آلایندههای محیطی محافظت شود. برای پروفیلهای فلزی، به ویژه آلومینیوم یا فولاد، ممکن است پوششهای ضد خوردگی خاصی استفاده شود تا مانع زنگزدگی و آسیب ناشی از شرایط جوی گردد. پس از بستهبندی اولیه، پروفیلها باید در بستهبندیهای نهایی مانند کارتنها، جعبههای چوبی، یا پالتهای فلزی قرار گیرند. این بستهبندیها به گونهای طراحی شدهاند تا از فشار، ضربه و آسیبهای مکانیکی محافظت کنند. برای پروفیلهای بزرگ یا سنگین، غالباً از پالتها جهت تسهیل حملونقل استفاده میشود. همچنین، برای حفظ ثبات و ایمنی پروفیلها در حملونقل، به استفاده از نوارهای کششی یا سیمهای فلزی برای محکم کردن بستهبندی متوسل میشود. هر بسته باید برچسبهایی حاوی اطلاعات ضروری درباره محتویات داشته باشد. این اطلاعات شامل نوع پروفیل، ابعاد، وزن، تعداد واحدها و کد محصول است. همچنین ممکن است اطلاعات مرتبط با شماره سفارش، تاریخ تولید و جزئیات حملونقل نیز روی برچسبها قید شود. برچسبگذاری دقیق به فرآیند ارسال و پیگیری محصولات کمک زیادی میکند. اگر پروفیلها برای مناطق خاصی با محیط ویژه ارسال شوند، باید برچسبهایی مشخصکننده شرایط حملونقل نیز روی بستهبندی قرار گیرد. پس از بستهبندی، پروفیلها آماده حمل به مقصد نهایی هستند. حملونقل ممکن است از طرق مختلفی مانند دریایی، هوایی، جادهای یا ریلی انجام شود؛ این امر بستگی به مقصد و نوع محصول دارد. برای انتخاب مناسبترین روش حملونقل باید عواملی چون فاصله، هزینه، زمان تحویل و نوع محصول مورد توجه قرار گیرند. بستهبندیها باید به گونهای آماده شوند که از آسیب احتمالی محصول در طی مسیر جلوگیری کنند. شرکتهای معتبر حملونقل نقش مهمی در تحویل سریع و ایمن پروفیلها ایفا میکنند. برخی سفارشات خاص یا حجم بالای پروفیلها ممکن است به حملونقل تخصصی نیازمند باشند که تجهیزات خاصی مانند ماشینآلات بالابر یا وسایل حملونقل سفارشی برای بارگیری و تخلیه استفاده شود. برای تضمین تحویل به موقع و بدون مشکل پروفیلها معمولاً سیستمهای پیگیری و نظارت بر ارسال به کار گرفته میشوند. این سیستمها به شرکتها و مشتریان امکان بررسی وضعیت بستهها را میدهند تا از هرگونه تأخیر یا مشکل احتمالی مطلع باشند. این مسئله موجب افزایش شفافیت و کاهش مشکلات مرتبط با حملونقل میشود. در نهایت، فرآیند بستهبندی و ارسال نقش حیاتی در تضمین تحویل ایمن و به موقع پروفیلهای صنعتی به مشتریان دارد. بستهبندی صحیح نه تنها از محصولات محافظت میکند بلکه به افزایش رضایت مشتری و ارتقاء اعتبار برند کمک میکند. برای مشاهده ورق آلیاژی کلیک کنید.
نوآوریها و روندهای آینده در فرایند تولید پروفیل صنعتی
صنعت پروفیلهای صنعتی با توجه به پیشرفتهای تکنولوژیکی و تغییرات نیاز بازار، دائماً در حال تحول است. تولیدکنندگان پروفیلها پیوسته به دنبال روشهای نوآورانه و بهبودهای مداوم برای ارتقای کارایی، کاهش هزینهها و ارتقاء کیفیت محصولات هستند. برخی از نوآوریها و روندهای آینده در این صنعت عبارتاند از: یکی از روندهای مهم، استفاده از مواد جدید و پیشرفته است. افزایش تقاضا برای کاهش وزن و بهبود ویژگیهای مکانیکی موجب شده تا کاربرد آلیاژهای خاص و کامپوزیتها در ساخت پروفیلهای صنعتی بیشتر شود. این مواد ضمن افزایش مقاومت در برابر خوردگی، عملکرد بهتری در شرایط دشوار محیطی ارائه میدهند و عمر محصولات را افزایش میدهند، همچنین به سبکتر شدن قطعات کمک میکنند که برای صنایع خودروسازی و هوافضا بسیار مهم است. اتوماسیون و دیجیتالی شدن فرآیندها نیز از دیگر روندهای آینده صنعت پروفیل است. با پیشرفت فناوریهایی نظیر هوش مصنوعی (AI) و اینترنت اشیاء (IoT)، تولیدکنندگان توانایی اتوماسیون کامل فرآیندهای تولیدی خود را دارند. این توسعهها به کاهش خطاها، بهینهسازی مصرف انرژی و مواد، و در نتیجه کاهش هزینههای تولید منجر میشوند. علاوه بر این، بهرهگیری از دستگاههای تولید هوشمند و سیستمهای آنلاین نظارت بر کیفیت، دقت و کارایی تولید پروفیلها را افزایش میدهد. فناوریهای چاپ سهبعدی (3D Printing) هم در حال گسترش هستند. این فناوری امکان ساخت پروفیلهای پیچیدهتر با اشکال و ابعاد خاص را فراهم میکند که صنایع مختلف قادر به تولید قطعات خاص با دقت بالا و هزینه کمتر میشوند. همچنین، این تکنولوژی نوآوریهایی را برای طراحی و توسعه پروفیلهای صنعتی ارائه میدهد. موضوع بازیافت و استفاده مجدد از مواد نیز یکی از مسائل کلیدی آینده خواهد بود. با توجه به دغدغههای زیستمحیطی و فشار برای کاهش ضایعات، شرکتها در حال سرمایهگذاری روی فناوریهای بازیافت فلزات و آلیاژها هستند. این اقدامات موجب استفاده بهینهتر از مواد اولیه و تولید پایدارتر پروفیلها میشود که دوستدار محیطزیست است. در نهایت، روند سفارشیسازی و تولید براساس تقاضا نیز اهمیت بیشتری پیدا کرده است. با پیشرفت تکنولوژیهای تولیدی و نیاز به واکنش سریع به درخواستهای بازار، ساخت پروفیلها بیشتر بهصورت سفارشی و با مشخصات دقیق انجام خواهد شد. این تغییر به صنایع امکان داشتن محصولاتی متناسب با نیازهای خاص خود را بدون نیاز به انبار کردن انبوه محصولات استاندارد میدهد. این نوآوریها و روندها همراه با تغییرات سریع در فناوری، بازار و نیازهای صنعتی نشان میدهد که صنعت پروفیلهای صنعتی در حال تغییر و تحول است و در آینده شاهد توسعههایی چشمگیر در کیفیت، کارایی، و طراحی خواهیم بود.
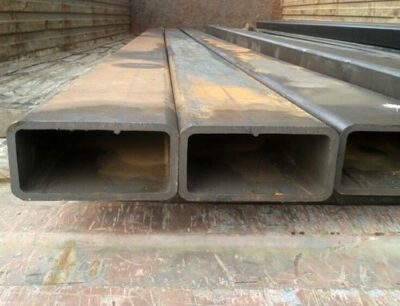
فرایند تولید پروفیل صنعتی
چالشها و موانع در تولید پروفیل صنعتی
در تولید پروفیلهای صنعتی، چالشها و موانع مختلفی وجود دارند که ممکن است بر کیفیت، کارایی و هزینههای تولید تأثیرگذار باشند. این چالشها میتوانند ناشی از محدودیتهای فناوری، مشکلات اقتصادی، مسائل زیستمحیطی و نیازهای خاص مشتریان باشند. در اینجا به برخی از این چالشهای اصلی اشاره میکنیم. یکی از بزرگترین چالشها، تأمین مواد اولیه است. برای تولید پروفیلهای صنعتی با کیفیت نیاز به مواد اولیه با ویژگیهای خاص و استاندارد داریم. نوسانات قیمت، کمبود منابع اصلی مانند آلومینیوم و فولاد و مشکلات تأمین این مواد میتواند بر روند تولید اثر منفی بگذارد. همچنین افزایش هزینه مواد اولیه، بهویژه در زمان بحرانهای اقتصادی، میتواند هزینههای تولید را بالا ببرد. محدودیتهای فناوری و ماشینآلات نیز یکی از موانع اصلی در تولید پروفیلهای صنعتی است. فرآیندهای تولید نیاز به تجهیزات پیشرفته دارند که هزینههای بالایی را بههمراه دارند. نگهداری و تعمیرات این دستگاهها نیز هزینهبر است، و با توجه به پیچیدگی طراحی پروفیلها، دقیق بودن تولید اهمیت زیادی دارد. هر نقصی در ماشینآلات یا فرآیندها میتواند به مشکلات کیفی و هدررفت منابع منجر شود. مسائل زیستمحیطی و پایداری فرآیندها نیز از چالشهای مهم صنعت پروفیلهای صنعتی محسوب میشود. قوانین زیستمحیطی سختگیرانهتر در بسیاری از کشورها، تولیدکنندگان را مجبور به استفاده از روشهای پایدارتر و دوستدار محیط زیست کرده است. این تغییرات ممکن است شامل استفاده از انرژیهای تجدیدپذیر، کاهش مصرف آب و آلودگی هوا و افزایش بازیافت باشد. اجرای چنین تغییراتی میتواند به سرمایهگذاری بیشتر و اصلاح فرآیندهای تولید نیاز داشته باشد که ممکن است برای برخی شرکتها چالشبرانگیز باشد. مشکلات نیروی کار نیز یکی دیگر از موانع اساسی است. تولید پروفیل صنعتی به نیروی کار متخصص و ماهر نیاز دارد. کمبود نیروی کار ماهر و مشکلات در جذب و نگهداشت کارکنان باتجربه میتواند بر روند تولید تأثیر منفی بگذارد. در فرایندهای پیچیده، نبود نیروی متخصص ممکن است کیفیت تولید را کاهش داده و زمان آن را افزایش دهد. تغییرات سریع در تقاضای بازار و نیازهای مشتریان نیز چالشی دیگر در این زمینه است. صنایع مختلف ممکن است به پروفیلهایی با مشخصات خاص یا طراحیهای نوین نیاز داشته باشند. توانایی تولیدکنندگان در پاسخگویی سریع به این نیازها و تطبیق با تغییرات بازار چالشی مهم تلقی میشود و ممکن است نیازمند بروز رسانی تجهیزات و تغییر فرایندها باشد که هزینهها و زمان تولید را افزایش میدهد. رقابت فشرده و فشار قیمتها هم در این صنعت جایگاه ویژهای دارد. با افزایش رقابت در بازارهای جهانی، تولیدکنندگان مجبورند هزینهها را کاهش داده و بهرهوری را بالا ببرند. این فشارها میتواند منجر به کاهش حاشیه سود یا حتی کاهش کیفیت محصولات برای پایین آوردن هزینهها شود. شرکتها باید به صورت مستمر در زمینه نوآوری و بهبود فرآیندها فعالیت کنند تا از رقبای خود جلو بزنند. در نهایت، لجستیک و توزیع محصولات هم چالشهای خاص خود را دارد. حملونقل پروفیلهای صنعتی، بهویژه بزرگ و سنگین، میتواند با مشکلاتی همچون آسیبدیدگی حین حمل، تأخیر در تحویل و هزینههای بالای حملونقل مواجه شود. این مسائل میتوانند بر توانایی شرکتها در تأمین بهموقع نیازهای مشتریان تأثیر بگذارند و موجب کاهش رضایت مشتریان شوند. به طور کلی، تولید پروفیلهای صنعتی با چالشها و موانع بسیاری روبرو است که برای غلبه بر آنها نوآوری، سرمایهگذاری در فناوریهای جدید، مدیریت منابع مناسب و سازگاری با شرایط بازار و قوانین زیستمحیطی ضروری است. در این مقاله فرایند تولید پروفیل صنعتی بیان گردید.