فرایند تولید ورق سنگین
در این مقاله به فرایند تولید ورق سنگین پرداخته می شود و به شما کمک می کند که در زمان بسیار کوتاه به بررسی موضوع مقاله پرداخته و دانش خود را در این حوزه ارتقا دهید. این مقاله بر اساس آخرین ژورنالهای صنعت فولاد گردآوری شده و تلاش شده که با بیان خلاصه و روان به موضوع پرداخته شود.
فرایند تولید ورق سنگین
ورق سنگین دستهای از محصولات تخت فولادی است که به خاطر ضخامت بالا، معمولاً بیش از ۱۰ میلیمتر، در گروه محصولات سنگین قرار میگیرد. این ورقها نسبت به ورقهای معمولی دارای مقاومت مکانیکی بیشتری هستند و برای کاربردهایی طراحی شدهاند که به تحمل بارهای سنگین، فشار بالا یا شرایط محیطی سخت نیاز دارند. ترکیبات شیمیایی این ورقها ممکن است شامل عناصر آلیاژی خاصی مانند منگنز، کروم یا نیکل باشد تا ویژگیهای مقاومتی و استحکام آنها افزایش یابد. مصرف اصلی ورق سنگین در صنایع زیرساختی و پروژههای مهندسی بزرگ است. این ورقها در ساخت سازههای فلزی عظیم مانند پلها، سدها، ساختمانهای بلندمرتبه، دکلهای نفتی و گازی و اسکلتهای صنعتی به کار برده میشوند. مقاومت بالای آنها در برابر فشار، ضربه و خوردگی، آنها را به گزینهای عالی برای محیطهای کاری سخت و پرتنش تبدیل کرده است. این ورقها همچنین در صنعت کشتیسازی اهمیت ویژهای دارند؛ چون ساخت بدنه کشتیها، زیرساخت بنادر و سازههای دریایی نیازمند موادی با ضخامت مناسب و دوام بالا در برابر آب شور و تغییرات دمایی است. علاوه بر این، در صنایع تولید مخازن تحت فشار، بویلرها و تانکرهای حمل گاز و مایعات نیز از ورق سنگین استفاده میشود، زیرا قابلیت تحمل فشار داخلی بالا یکی از ویژگیهای اصلی آنها محسوب میشود. در صنایع ماشینآلات سنگین، تجهیزات معدنی، خطوط ریلی و صنایع نظامی نیز کاربری گستردهای دارند. برای نمونه، در ساخت شاسی ماشینآلات راهسازی یا بدنه خودروهای زرهی، از ورقهایی با ترکیب شیمیایی خاص و ضخامت زیاد استفاده میشود. این ورقها باید نهتنها سخت باشند بلکه از نظر چقرمگی نیز در سطح مطلوبی باشند تا در برابر ضربه و شکست مقاومت کنند. در کل، ورق سنگین به خاطر تنوع آلیاژی، قابلیت تولید در ابعاد بزرگ و خواص مکانیکی ممتاز به عنوان محصولی راهبردی در بسیاری از پروژههای صنعتی و عمرانی شناخته میشود. اهمیت آن در زیرساختهای حیاتی و صنایع سنگین کاملاً آشکار بوده و کیفیت آن میتواند تأثیر مستقیمی بر ایمنی، دوام و بهرهوری سازهها داشته باشد. در این مقاله به فرایند تولید ورق سنگین می پردازیم.
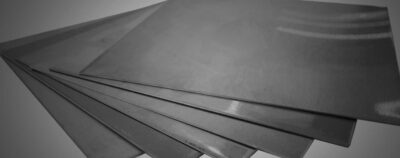
فرایند تولید ورق سنگین
مواد اولیه ورق سنگین
برای تولید ورق سنگین، ماده اولیه اصلی تختال فولادی است که از شمش فولادی بهدست میآید. تختالها به شکل قطعات مستطیلی و با ضخامت زیاد تولید میشوند و بسته به نوع ورق نهایی، میتوانند شامل فولادهای ساده کربنی یا آلیاژی با ترکیبات خاص باشند. کیفیت تختال و ترکیب شیمیایی آن تأثیر مستقیمی بر خواص مکانیکی، قابلیت جوشکاری، مقاومت در برابر خوردگی و دیگر ویژگیهای ورق سنگین دارد. برای ساخت تختال، معمولاً از روشهای رایج تولید فولاد مانند کوره بلند یا کوره قوس الکتریکی استفاده میشود. در این فرآیندها، سنگ آهن یا آهن اسفنجی به همراه قراضههای فولادی و عناصر آلیاژی مانند منگنز، کروم، مولیبدن، نیکل یا وانادیوم ذوب شده و پس از پالایش در قالبهای مستطیلی ریخته میشوند تا تختال تشکیل شود. ترکیب دقیق شیمیایی بستگی به استفاده نهایی ورق دارد؛ برای مثال، برای ورقهای مقاوم به سایش ممکن است درصد بالاتری از عناصر سختکننده استفاده شود. تختالهایی که برای تولید ورق سنگین بهکار میروند باید کیفیت سطحی مطلوبی داشته باشند و بدون ترک، حفره، آخال یا نقصهای ساختاری باشند. بنابراین، در برخی موارد، تختالها قبل از ورود به مرحله نورد تحت آزمونهای غیرمخرب مانند اولتراسونیک قرار میگیرند تا سلامت داخلی آنها تأیید شود. آمادهسازی مناسب مواد اولیه قبل از ورود به فرآیند نورد اهمیت زیادی دارد زیرا هرگونه نقص در تختال میتواند در ضخامتهای بالا تشدید شده و در محصول نهایی باقی بماند. بنابراین انتخاب دقیق نوع تختال، ترکیب شیمیایی مناسب و کنترل کیفی دقیق، پایههای اصلی برای تولید ورق سنگین با کیفیت بالا هستند.
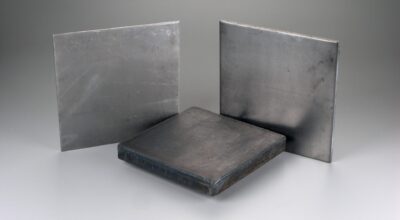
فرایند تولید ورق سنگین
فرآیند نورد گرم ورق سنگین
در فرآیند نورد گرم، تختال فولادی که پیشتر آمادهسازی و به دمای مطلوب حرارت داده شده است، وارد خط نورد میشود تا ضخامتش کاهش یابد و به ورق سنگین تبدیل گردد. این عملیات اغلب در دمای بالا، بین ۱۱۰۰ تا ۱۲۵۰ درجه سانتیگراد انجام میشود، به طوری که فولاد حالت خمیری پیدا کرده و امکان تغییر شکل مکانیکی بدون ترک یا شکست را داشته باشد. هدف اصلی این مرحله شامل کاهش ضخامت و افزایش طول و عرض تختال با کنترل دقیق بر ابعاد و خواص مکانیکی آن است. ابتدا تختال پیشگرمشده را به واحدهای نورد اولیه منتقل میکنند که در آنجا با عبور از میان غلطکهای قدرتمند، ضخامتش بهتدریج کاهش مییابد. هر مرحله عبور از غلطک به عنوان یک “پاس” شناخته میشود. در هر پاس بخشی از ضخامت کاهش یافته و این فرایند تا رسیدن به ضخامت نهایی ادامه پیدا میکند. بسته به ضخامت نهایی موردنظر و ویژگیهای فلز، تعداد پاسها میتواند متفاوت باشد. یکی از ویژگیهای مهم در نورد گرم، توانایی اصلاح عیوب سطحی و ارتقای ساختار داخلی فولاد است. با کنترل دقیق دما، نرخ تغییر شکل و زمان عبور از هر مرحله، خواص مکانیکی مانند مقاومت کششی، سختی و چقرمگی میتوانند بهینهسازی شوند. در این مرحله معمولاً از سیستمهای خنککاری میانپاس برای جلوگیری از افت بیش از حد دما استفاده میشود، زیرا کاهش ناگهانی دما ممکن است منجر به افت کیفیت سطحی یا ایجاد ساختار نامناسب گردد. در نهایت، پس از به پایان رسیدن نورد نهایی، ورقها وارد مرحله خنکسازی کنترلشده میشوند. این خنکسازی ممکن است به صورت طبیعی در هوا یا توسط آبپاشهای پر فشار انجام شود. سرعت خنککاری در این مرحله بر ریزساختار نهایی و خواص مکانیکی ورق سنگین تاثیر مستقیم دارد و یکی از عوامل کلیدی در تولید ورقهایی با خواص مهندسی خاص محسوب میشود. برای مشاهده ورق سیاه کلیک کنید.
خنک کاری صاف سازی ورق سنگین
پس از اتمام نورد گرم و دستیابی ورق به ضخامت نهایی، ضروری است ورق داغ تحت فرایند خنکسازی کنترلشده قرار گیرد تا ساختار متالورژی آن تثبیت شده و خواص مکانیکی مطلوب شکل گیرد. در این مرحله، کنترل دقیق سرعت و یکنواختی خنکشدن از اهمیت زیادی برخوردار است. خنکشدن بیش از حد سریع ممکن است موجب ایجاد تنشهای حرارتی، ترکخوردگی سطحی یا سختی بیش از حد شود؛ در حالی که خنکشدن خیلی کند ممکن است منجر به رشد دانههای ریزساختاری و کاهش مقاومت مکانیکی گردد. برای کنترل دقیق این فرایند، از سیستمهای خنکسازی به وسیله آب فشار بالا یا هوای فشرده استفاده میشود. گاهی، بسته به نوع فولاد و خواص مورد نظر، خنکسازی بهصورت ترکیبی از روشهای مختلف انجام میشود. علاوه بر خنکسازی، توزیع حرارت یکنواخت در سراسر ورق نیز بسیار مهم است، زیرا تفاوت دما در نقاط مختلف ورق میتواند منجر به تابخوردن یا خمیدگی آن شود. پس از خنکسازی، ورقها به بخش صافسازی منتقل میشوند. هدف در این بخش حذف تنشهای پسماند و امواج سطحی باقیمانده از نورد است. صافسازی معمولاً با عبور ورقها از میان مجموعهای از غلطکهای صافکننده صورت میگیرد که با تنظیم فشار و زاویه مناسب، سطح ورق را صاف کرده و از نظر ابعادی بهبود میبخشند. این مرحله بهویژه برای ورقهای ضخیم مهم است، زیرا تاب یا پیچیدگی لبهها میتواند کاربرد صنعتی دقیق را به چالش کشد. در پایان این مراحل، ورقها برای ورود به مراحل بعدی نظیر برش، آزمون یا عملیات حرارتی تکمیلی آماده میشوند. حفظ یکنواختی سطح، صاف بودن و کاهش تنشهای داخلی از ویژگیهای کلیدی این بخش در فرایند تولید ورق سنگین محسوب میشود.
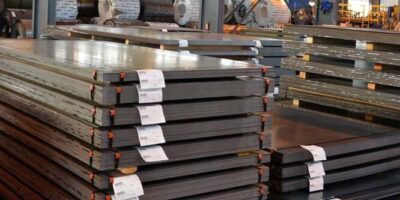
فرایند تولید ورق سنگین
عملیات حرارتی ورق سنگین
عملیات حرارتی در تولید ورقهای سنگین نقش حیاتی دارد و در مواردی ضروری است. این عملیات بهبود خواص مکانیکی، یکنواختی ساختار میکروسکوپی و افزایش مقاومت فولاد در برابر تنش، ضربه یا خوردگی را هدف قرار میدهد. نوع عملیات حرارتی با توجه به کاربرد نهایی ورق، نوع فولاد و استانداردهای فنی پروژه تعیین میشود. یکی از متداولترین روشها در فرآوری ورقهای سنگین، نرمالایز کردن است. در این روش، ورق تا دمای بین ۸۵۰ تا ۹۰۰ درجه سانتیگراد گرم شده و سپس در هوای آزاد سرد میشود. این روش به اصلاح ساختار کریستالی فولاد و حذف تنشهای داخلی و ارتقاء یکنواختی خواص مکانیکی در سطح ورق کمک میکند. نرمالایز کردن برای ورقهایی که در سازههای حساس یا تحت تاثیر بارهای متناوب هستند، بسیار کارآمد محسوب میشود. در موارد خاص همانند ورقهای مقاوم به سایش یا فشار بالا، از عملیات حرارتی کوئنچ و تمپر استفاده میشود. ابتدا ورق تا دمای بالا گرم و سپس سریعاً با آب یا روغن سرد میشود (کوئنچ)، که سطح فولاد را سختتر میکند. پس از آن ورق مجدداً گرم میشود (تمپر) تا شکنندگی ناشی از کوئنچ تعدیل شود و تعادل میان سختی و چقرمگی حاصل شود. این عملیات برای تولید ورقهایی که در ماشینآلات معدنی، تانکهای زرهی و مخازن تحت فشار به کار میروند، حیاتی است. گاهی عملیات بازپخت برای نرمسازی و افزایش شکلپذیری و جوشپذیری انجام میشود، مخصوصاً هنگامی که ورق در معرض شکلدهی شدید یا خمکاری خاص است. بازپخت موجب کاهش سختی و افزایش انعطافپذیری فولاد میشود. به طور کلی، عملیات حرارتی مرحلهای کلیدی در تولید ورق سنگین با خواص دقیق و قابل پیشبینی است. انتخاب نوع آن باید بر اساس شرایط کاری و خواص مورد انتظار صورت گیرد. این فرآیند معمولاً با کنترل دقیق دما، زمان و سرعت خنکسازی همراه است تا نتایج مطلوب حاصل شود. برای مشاهده تیرآهن کلیک کنید.
برش، تست و بسته بندی در فرایند تولید ورق سنگین
پس از پایان عملیات حرارتی و سرد کردن، ورقهای سنگین برای مرحله برش آماده میشوند. بسته به ضخامت و جنس فولاد، برش این ورقها میتواند با استفاده از دستگاههای برش گیوتینی، پلاسما، هوا-گاز (اکسیاستیلن)، یا حتی لیزر صنعتی انجام شود. هدف اصلی برش، تولید ورقهایی با ابعاد دقیق مطابق سفارش مشتری یا استانداردهای بازار است. در برخی پروژههای خاص، دقت در اندازهها و کیفیت لبههای برش خورده بسیار مهم است و باید سطوح برش صاف و بدون ترک یا زائده باشد. پس از برش، ورقها وارد مرحله آزمون و کنترل کیفیت میشوند. این آزمونها بر اساس نوع ورق و استفاده نهایی شامل آزمونهای مکانیکی مثل تست کشش، سختیسنجی، ضربه شارپی، و خمپذیری هستند. همچنین در پروژههای حساستر، آزمایشهای غیرمخرب مانند تست فراصوتی جهت تشخیص عیوب داخلی یا رادیوگرافی صنعتی انجام میشود. این آزمونها تضمین کننده سلامت ساختاری و خواص مکانیکی مطلوب ورق تولید شده هستند. در مرحله بعدی، ورقهای تایید شده به بخش بستهبندی هدایت میشوند. بستهبندی ورق سنگین به دلیل وزن و ابعاد بزرگ، نیازمند رعایت نکات فنی خاصی است. معمولاً ورقها به صورت پالتهای فلزی یا چوبی دستهبندی شده و با تسمههای فلزی محکم بسته میشوند. در صورت لزوم، برای جلوگیری از زنگزدگی، سطح ورقها با روغن محافظ پوشانده میشود یا از روکشهای پلاستیکی استفاده میشود. در نهایت، بستهبندی مناسب و استاندارد نه تنها حملونقل ایمنتر ورقهای سنگین را تسهیل میکند، بلکه از آسیب دیدن لبهها، سطوح و کاهش کیفیت محصول در زمان ذخیرهسازی یا تحویل به مشتری جلوگیری مینماید. رعایت اصول صحیح در این مرحله آخرین گام مهم برای حفظ کیفیت تولید و اعتبار تولیدکننده به شمار میرود.
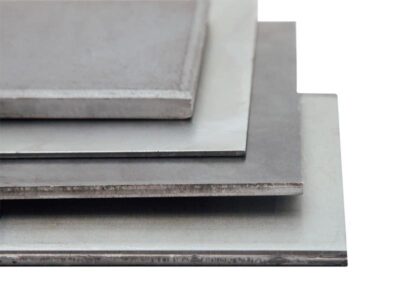
فرایند تولید ورق سنگین
استانداردهای در فرایند تولید ورق سنگین
در تولید ورقهای سنگین، توجه به استانداردهای بینالمللی و ملی بسیار مهم است، زیرا این استانداردها تعیینکننده کیفیت، ویژگیهای مکانیکی، ترکیب شیمیایی و ابعاد محصولات نهایی هستند. یکی از پرکاربردترین استانداردها در این زمینه، استاندارد ASTM آمریکاست، که برای ورقهای سنگین استفادهشده در سازهها، بویلرها، خطوط لوله و صنایع نفت و گاز بسیار اهمیت دارد. به عنوان مثال، استانداردهای ASTM A36 برای ورقهای ساختمانی معمولی و ASTM A516 برای ورقهایی که باید در برابر فشار و دمای بالا مقاوم باشند، شناختهشدهاند. استاندارد اروپایی EN نیز مانند EN 10025 یکی از مراجع معتبر است که مشخصات انواع ورقهای سازهای، آلیاژی و مقاوم به سایش را تعیین میکند. این استانداردها به کلاسبندیهای مختلفی تقسیم میشوند که بر اساس مقاومت کششی، چقرمگی یا دیگر خواص ویژه، ورقها را طبقهبندی میکنند. برای مثال، ورقهای با کیفیت S355 یا S690QL بر اساس کاربردهای صنعتی خاص مورد استفاده قرار میگیرند. در صنایع نفت، گاز و پتروشیمی، استانداردهای سازمانهای بینالمللی مانند API (انستیتوی نفت آمریکا) نیز اهمیت بالایی دارند. ورقهایی که برای ساخت مخازن تحت فشار، خطوط لوله یا تجهیزات دریایی استفاده میشوند باید مطابق با استانداردهای دقیق API 2H یا API 5L تولید شوند. در ایران نیز علاوه بر استفاده از استانداردهای بینالمللی، برخی تولیدکنندگان بر اساس استاندارد ملی ISIRI که ترکیبی از استانداردهای جهانی است، تولید میکنند. رعایت این استانداردها برای حصول اطمینان از قابلیت صادرات و پذیرش محصولات در پروژههای داخلی و خارجی بسیار حیاتی است. به طور کلی، استانداردها نهتنها کیفیت ورق را تضمین میکنند، بلکه در تعیین نحوه آزمونهای کنترل کیفیت، روشهای بستهبندی، علامتگذاری و مستندسازی محصولات نیز نقشی اساسی دارند. پیروی از یک استاندارد معتبر به مشتریان این اطمینان را میدهد که ورق سنگین تولیدشده توانایی تحمل شرایط سخت عملیاتی را دارد. برای مشاهده پروفیل صنعتی کلیک کنید.
چالشها و نکات کنترل کیفیت در فرایند تولید ورق سنگین
کنترل کیفیت در تولید ورق سنگین از بخشهای حیاتی و چالشبرانگیز این فرآیند به شمار میآید. یکی از مشکلات کلیدی، تضمین یکنواختی خواص مکانیکی در تمامی نقاط ورق است؛ چرا که ضخامت زیاد و ابعاد بزرگ باعث تفاوت دمای داخلی هنگام نورد یا عملیات حرارتی میشود و در نتیجه ریزساختار فولاد در بخشهای مختلف تغییر میکند. این امر میتواند نقاط ضعف یا ناهمگن در ورق ایجاد کند، لذا کنترل دقیق دمای نورد، سرعت خنکسازی و یکنواختی عملیات حرارتی برای پیشگیری از این مسائل ضروری است. عیوب سطحی مانند ترک، پوستهریزی، آخالهای غیرفلزی یا تورق داخلی نیز از چالشهای مهم در تولید ورق سنگین هستند. برای شناسایی این عیوب، باید از تستهای غیرمخرب نظیر اولتراسونیک، مغناطیسی یا رادیوگرافی در مراحل مختلف تولید استفاده کرد. وجود نقصهای پنهان ممکن است در مراحل بعدی شکلدهی یا جوشکاری مشکلات جدی ایجاد کند، به همین دلیل پروژههای صنعتی حساس به ورقهایی با استانداردهای بالاتر و گزارشهای تست معتبر نیاز دارند. کنترل ابعاد نیز چالشی دیگری است، چرا که هرگونه انحراف از تلرانسهای مجاز در ضخامت، طول یا عرض میتواند باعث عدم مطابقت محصول با نیاز پروژهها شود. بنابراین استفاده از تجهیزات اندازهگیری دقیق و تست ابعادی مکرر طی فرآیند تولید الزامی است. علاوه بر این، مستندسازی نتایج کنترل کیفیت و پیگیری دقیق هر بچ تولیدی اهمیت ویژهای دارد. در پروژههای صنعتی بزرگ، تولیدکنندگان باید قادر باشند تمام سوابق تولید، آزمایشها و عملیات حرارتی اعمال شده بر روی ورقها را به مشتری ارائه دهند. این شفافیت نه تنها اعتبار تولیدکننده را افزایش میدهد بلکه در صورت بروز مشکلات فنی، امکان ردیابی و رفع نقص را فراهم میکند.