فرایند تولید میلگرد آجدار
در این مقاله به فرایند تولید میلگرد آجدار پرداخته می شود و به شما کمک می کند که در زمان بسیار کوتاه به بررسی موضوع مقاله پرداخته و دانش خود را در این حوزه ارتقا دهید. این مقاله بر اساس آخرین ژورنالهای صنعت فولاد گردآوری شده و تلاش شده که با بیان خلاصه و روان به موضوع پرداخته شود.
فرایند تولید میلگرد آجدار
فرایند تولید میلگرد آجدار یکی از مهمترین و پیچیدهترین فرآیندها در صنعت فولاد است که برای ارائه محصولاتی با ویژگیهای خاص و مناسب برای استفاده در پروژههای ساختمانی، راهسازی، پلسازی و سایر سازههای بتنی طراحی شده است. میلگرد آجدار به واسطه ساختار ویژهای که دارد، نقش حیاتی در تقویت بتن ایفا میکند و موجب افزایش مقاومت کششی و استحکام سازهها میشود. تفاوت عمده میلگرد آجدار با میلگرد ساده در وجود آجهای مخصوص روی سطح آن است که باعث بهبود چسبندگی میلگرد به بتن میگردد. این ویژگی کلیدی موجب میشود که میلگرد آجدار برای پروژههای عمرانی که به مقاومت بالاتری نیاز دارند، بسیار مورد استفاده قرار گیرد.
ذوب و آمادهسازی مواد اولیه در فرایند تولید میلگرد آجدار
مرحله ذوب و آمادهسازی مواد اولیه آغازگر فرآیند تولید میلگرد آجدار بوده و اهمیت زیادی در کیفیت نهایی محصول دارد. مواد اولیه این بخش شامل سنگآهن، قراضههای فولادی، کک متالورژی و فروآلیاژهایی مانند فروسیلیس یا فرو منگنز است که بر اساس ترکیب شیمیایی مورد نیاز انتخاب و به دقت اندازهگیری میشوند. این مواد ابتدا به کورههای ذوب منتقل میشوند. در کارخانههای مدرن، معمولاً از کورههای قوس الکتریکی (EAF) و گاهی از کوره بلند استفاده میشود. در کوره قوس الکتریکی، جریان قوی برق از طریق الکترودهای گرافیتی وارد مواد شده و دمایی بالای ۱۵۰۰ درجه سانتیگراد ایجاد میکند که موجب ذوب سریع میشود. در کوره بلند نیز با استفاده از سوختهای کربنی مانند کک و دمش هوای داغ، سنگآهن ذوب میشود. در حین فرآیند ذوب، ناخالصیهایی نظیر گوگرد، فسفر، و سیلیس به صورت سرباره از سطح فولاد مذاب جدا میگردند. در این مرحله، ترکیب شیمیایی فولاد به دقت کنترل شده و در صورت لزوم، افزودنیهایی برای ارتقاء ویژگیهای مکانیکی و فیزیکی میلگرد به آن افزوده میشود. به عنوان مثال، افزایش کربن استحکام کششی میلگرد را افزایش میدهد، در حالی که کاهش گوگرد و فسفر مقاومت را در برابر شکست بهبود میبخشد. پس از تکمیل مرحله ذوب و رسیدن به ترکیب شیمیایی مطلوب، فولاد مذاب آماده انتقال به مراحل بعدی، یعنی ریختهگری به شکل بیلت میشود. دقت در این مرحله مهم است، چرا که هر نقص یا ناخالصی ممکن است مشکلات جدی در کیفیت نهایی میلگرد آجدار ایجاد کند.
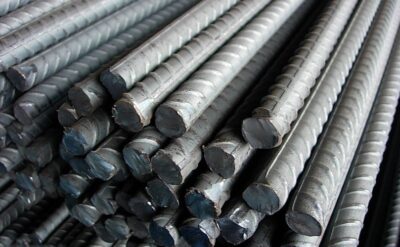
فرایند تولید میلگرد آجدار
ریخته گری و شکل دهی اولیه میلگرد آجدار
پس از تکمیل فرآیند ذوب و آمادهسازی مواد اولیه، لازم است فولاد مذاب به شکلی مناسب برای فرآیند نورد تبدیل شود. این مرحله به عنوان ریختهگری و شکلدهی اولیه شناخته میشود و تأثیر بسزایی در کیفیت ساختاری میلگردهای آجدار دارد. در این فرآیند، فولاد مذاب از طریق پاتیلهای خاص به بخش ریختهگری منتقل میشود. یکی از روشهای معمول، ریختهگری پیوسته است که در آن فولاد مذاب وارد قالبهایی با سطح مقطع مشخص شده و با سیستمهای خنککننده آب و هوا به تدریج سخت میشود. محصول نهایی این فرآیند بیلت یا شمش فولادی است که به صورت مقاطع مستطیلی یا مربعی و در ابعاد استاندارد تولید میشود. بیلتها معمولاً دارای ابعادی بین ۱۰۰×۱۰۰ میلیمتر تا ۱۵۰×۱۵۰ میلیمتر هستند و طول آنها بر اساس نیاز خطوط تولید تنظیم میگردد. کیفیت بیلت و یکنواختی ترکیب شیمیایی، نبود ترکها یا حبابهای داخلی، و ساختار بلوری منظم بسیار حائز اهمیت است، زیرا هر نقصی در این مرحله میتواند در طول فرآیند نورد تشدید شود و منجر به تولید میلگردهای ناقص گردد. پس از سرد شدن کامل، بیلتها به دقت برش داده شده و برای ورود به خطوط نورد آماده میشوند. در برخی کارخانهها، بیلتها قبل از نورد وارد مرحله پیشگرمکن میشوند تا به دمای مناسب برای عملیات نورد برسند. این حرارتدهی مجدد باعث بهبود انعطافپذیری بیلت و تسهیل فرآیند شکلدهی در مراحل بعدی میشود. ریختهگری دقیق و شکلدهی اصولی بیلتها پایهگذار کیفیت بالای میلگردهای آجدار است و تأثیر مستقیمی بر خواص مکانیکی و ظاهری محصول نهایی دارد.
نورد گرم در فرایند تولید میلگرد آجدار
پس از آمادهسازی بیلتها در مرحله ریختهگری، فرآیند نورد گرم آغاز میشود که یکی از مراحل کلیدی تولید میلگرد آجدار محسوب میشود. در ابتدا، بیلتهای فولادی وارد کورههای پیشگرم شده و به دمایی بین ۱۱۰۰ تا ۱۲۵۰ درجه سانتیگراد میرسند. این دما موجب افزایش انعطافپذیری فولاد شده و امکان شکلدهی تحت فشار بالا را فراهم میآورد. هنگامی که بیلتها به دمای مطلوب میرسند، به خط نورد منتقل میشوند. در این خط، بیلتها از میان مجموعهای از غلتکهای خاص عبور داده میشوند. غلتکها در چندین مرحله با فشار شدید مقاطع بیلت را کوچکتر کرده و به تدریج آنها را به شکل میلگردهای مختلف تبدیل میکنند. میلگردها بر اساس نیاز بازار در قطرهای متفاوت مانند ۸، ۱۲، ۱۶ یا ۲۰ میلیمتری تولید میشوند. در حین نورد، علاوه بر کاهش اندازه و تغییر شکل، عملیات آجزنی نیز انجام میشود. قالبهای خاص آجزنی که بر روی غلتکها نصب شدهاند، نقشهای منظم و برجستگیهایی را روی سطح میلگرد ایجاد میکنند. این نقشها برای افزایش چسبندگی میلگرد به بتن بسیار مهم هستند و نقشی اساسی در مقاومت نهایی سازههای بتنی دارند. کنترل دقیق دما، سرعت حرکت بیلتها و تنظیم درست فاصله غلتکها در این مرحله اهمیت بسیاری دارد. هر گونه خطا ممکن است موجب تولید میلگردهای بیکیفیت، ترکهای سطحی یا عدم یکنواختی در ابعاد شود. پس از پایان نورد، میلگردها با قیچیهای صنعتی بر اساس طول استاندارد (معمولاً ۱۲ متر) بریده و برای خنکسازی و کنترل کیفیت آماده میشوند. فرآیند نورد گرم نه تنها شکل نهایی میلگرد را مشخص میکند بلکه بر خواص مکانیکی آن مانند مقاومت کششی، چقرمگی و انعطافپذیری نیز تاثیر مستقیمی دارد. برای مشاهده میلگرد ساده کلیک کنید.
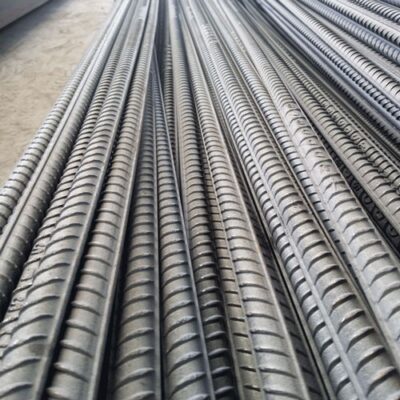
فرایند تولید میلگرد آجدار
اعمال آجها بر روی میلگرد آجدار
پس از عبور بیلتهای گرمشده از مراحل اولیه نورد و رسیدن به قطر موردنظر، مرحله حیاتی اعمال آج روی سطح میلگرد فرا میرسد. آجزنی نه تنها ظاهر میلگرد را تعیین میکند، بلکه یکی از مهمترین ویژگیهای مکانیکی آن، یعنی افزایش چسبندگی به بتن و تقویت استحکام سازه را شکل میدهد. فرآیند آجزنی معمولاً همزمان با نورد نهایی انجام میشود و میلگردها از میان غلتکهای مخصوص آجزنی عبور میکنند. این غلتکها دارای شیارها و الگوهای خاصی هستند که هنگام عبور میلگرد، برجستگیها را با دقت و یکنواختی روی سطح ایجاد میکنند. طراحی این الگوها ممکن است بسته به استانداردهای ملی و بینالمللی متفاوت باشد. برای مثال، میلگردهای استاندارد A3 دارای آجهای مارپیچی و میلگردهای A4 دارای آجهای جناقی هستند. آجها به گونهای طراحی میشوند که در بتن، مقاومت بیشتری در برابر نیروهای کششی و برشی ایجاد کنند. نوع، زاویه و عمق آجها تاثیر چشمگیری بر میزان چسبندگی و عملکرد نهایی میلگرد در سازههای بتنی دارد. به همین دلیل، تنظیم دقیق غلتکهای آجزنی، فشار وارد شده و یکنواختی آجها اهمیت ویژهای دارد. هرگونه نقص در این مرحله – مانند ناقص بودن آج، فاصله نامنظم یا سطح صاف – ممکن است عملکرد مناسب میلگرد در بتن را مختل کند و در پروژههای ساختمانی رد شود. اعمال صحیح آجها یکی از شاخصهای کیفیت میلگردهای آجدار است و مستقیماً بر ایمنی، دوام و استحکام پروژههای عمرانی تاثیر میگذارد.
سرد کردن و برش در فرایند تولید میلگرد آجدار
پس از عملیات نورد و ایجاد آجها، میلگردهای تازه تولید شده همچنان دارای دمای بالایی هستند که نیاز به خنککاری کنترلشده دارند. این فرآیند، خنککاری نامیده میشود و در بهبود ویژگیهای مکانیکی میلگردها مانند افزایش استحکام تسلیم، مقاومت کششی و چقرمگی نقش کلیدی دارد. در این مرحله، میلگردها از طریق سیستمی به نام بستر خنککننده عبور داده میشوند. این بستر، شامل مجموعهای از نوارها یا غلطکهای فلزی است که میلگردها روی آن حرکت کرده و طی زمان تحت تاثیر جریان هوا سرد میشوند. برخی خطوط تولید پیشرفته برای دستیابی به ویژگیهای مکانیکی خاص از روش خنککاری آبی موسوم به TMT بهره میبرند. در این روش، میلگردهای داغ به سرعت توسط آب تحت فشار پاشیده میشوند و سطحی سخت روی آنها شکل میگیرد، در حالی که هسته میلگرد همچنان گرم و نرم باقی میماند. این روش سبب افزایش قابل توجه سختی و دوام میلگرد میگردد. پس از رسیدن به دمای محیط، میلگردها برای مرحله برش آماده میشوند. در این مرحله، میلگردها با قیچیهای صنعتی بزرگ و دقیق به طولهای استاندارد معمولاً ۱۲ متر بریده میشوند. بر اساس سفارش مشتری یا نوع استفاده، ممکن است در اندازههای خاص دیگری نیز برش داده شوند. دقت در برش بسیار مهم است؛ زیرا طول نامناسب یا آسیب در نقاط برش ممکن است مشکلاتی در مراحل بعدی ایجاد کند. پس از برش، میلگردها به صورت دستههای منظم بستهبندی شده و برای مراحل بعدی مانند بازرسی نهایی، علامتگذاری و حمل به انبار آماده میشوند. فرآیندهای خنککاری و برش مستقیماً بر کیفیت نهایی، یکنواختی ابعاد و استحکام میلگردها تأثیرگذارند و بخش جداییناپذیر تولید میلگردهای آجدار استاندارد محسوب میشوند برای مشاهده ورق سیاه کلیک کنید.
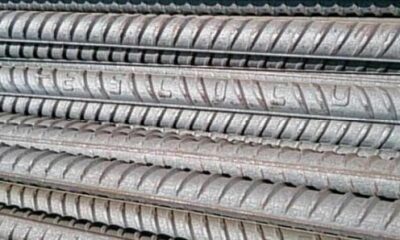
فرایند تولید میلگرد آجدار
کنترل کیفیت و آزمایشها در فرایند تولید میلگرد آجدار
بعد از مرحله نورد و ایجاد آجها، میلگردهای تازهساختهشده هنوز دمای بالایی دارند و باید به صورت کنترلشده سرد شوند. این فرایند نقش مهمی در بهبود خصوصیات مکانیکی میلگردها مانند افزایش استحکام تسلیم، مقاومت کششی و چقرمگی دارد. میلگردها از بسترهای خنک کننده عبور میکنند که در آنجا با استفاده از جریان طبیعی هوا یا در موارد خاص با روش خنککننده آبی، به تدریج سرد میشوند. برخی کارخانهها برای ارتقا کیفیت محصول، از روش خنککاری ترمومکانیکی بهرهگیری میکنند که موجب تشکیل لایهای سخت در سطح و هستهای نرم در مرکز میلگرد میشود. این ساختار دوگانه مقاومت چشمگیری در برابر تنشهای کششی و فشاری فراهم میآورد. پس از خنکسازی، میلگردها توسط دستگاههای صنعتی به طولهای استاندارد برش داده میشوند. معمولاً میلگردها به اندازه ۱۲ متر برش داده میشوند، اما بسته به نیاز پروژهها امکان تولید در طولهای سفارشی نیز وجود دارد. دقت در برش حیاتی است، زیرا طولهای نادرست ممکن است در نصب و اجرا مشکل ایجاد کنند. پس از برش، میلگردها به شکل بستههای منظم مرتب میشوند تا حمل و نقل آنها آسان شود. زمانی که مرحله بستهبندی به پایان میرسد، میلگردهای تولیدی تحت مجموعهای از آزمایشهای کنترل کیفیت قرار میگیرند. نمونههایی از میلگردها انتخاب شده و آزمایشهایی مانند کشش، خمش، بازخمش، سختیسنجی و بررسی ساختار متالورژیکی روی آنها انجام میشود. هدف از این آزمونها اطمینان حاصل کردن از این است که محصول نهایی مطابق با استانداردهای ملی و بینالمللی باشد. در آزمایش کشش، مقاومت میلگرد در برابر نیروی کششی تا لحظه شکست اندازهگیری میشود و در آزمایش خمش و بازخمش، میزان انعطافپذیری و مقاومت میلگرد در برابر تغییر شکلهای ناگهانی ارزیابی میشود. همچنین ابعاد، شکل و یکنواختی آجها به دقت بررسی میشود تا از کیفیت ظاهری مناسب محصول مطمئن شویم. میلگردهایی که تمام آزمایشها را با موفقیت پشت سر گذاشتهاند، مجوز ورود به مرحله نهایی یعنی بستهبندی و انبارداری را دریافت میکنند. میلگردها در بستههای ۲ یا ۵ تنی بستهبندی شده و با استفاده از برچسبهای شناسایی اطلاعات فنی، استاندارد تولید و شماره سریال مشخص میشوند. این بستهها در انبارهای روباز یا سرپوشیده نگهداری میشوند که باید شرایط مطلوب از نظر رطوبت، دما و تهویه مناسب را داشته باشند تا از زنگزدگی یا آسیب به میلگردها جلوگیری شود. در نهایت، میلگردهای آماده برای مشتریان بارگیری شده و با رعایت اصول ایمنی حملونقل به محل پروژههای عمرانی ارسال میشوند.
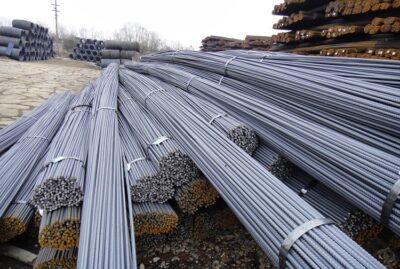
فرایند تولید میلگرد آجدار
بسته بندی و حمل میلگرد آجدار
پس از تأیید نهایی در مرحله کنترل کیفیت، میلگردهای آجدار برای بستهبندی آماده میشوند. این میلگردها بر اساس قطر، طول و وزن به گروههای مشخص تقسیم میشوند. هر بسته معمولاً وزنی بین ۲ تا ۵ تن دارد و با تسمههای فلزی یا پلاستیکی محکم بسته میشود تا در حملونقل دچار بازشدگی یا آسیب نشود. هر بسته مجهز به برچسبهایی برای شناسایی دقیق است که اطلاعاتی مانند نام کارخانه، شماره ذوب، استاندارد تولید، قطر میلگرد و تاریخ تولید را شامل میشود. در مرحله حمل، بستههای میلگرد با جرثقیل، لیفتراک یا تجهیزات بارگیری مخصوص به کامیونها یا واگنهای ریلی منتقل میشوند. رعایت نکات ایمنی در این بخش اهمیت دارد تا از آسیب به میلگردها و تجهیزات جلوگیری به عمل آید. میلگردها باید به گونهای چیده شوند که از جابجایی یا افتادن آنها طی مسیر جلوگیری شود. در صورت نیاز به حملونقل طولانی مدت یا مواجهه با شرایط آبوهوایی خاص، از پوششهای محافظ مانند برزنت استفاده میشود تا میلگردها از رطوبت، باران یا آلودگیهای محیطی محافظت شوند. حمل درست و استاندارد میلگردها باعث حفظ کیفیت محصول و افزایش رضایت مشتریان میشود و هزینههای تعمیر یا بازگشت کالا را کاهش میدهد. دقت در تمامی این مراحل نشاندهنده تعهد تولیدکننده به ارائه محصولی با کیفیت و خدمات حرفهای به مشتریان است.