فرایند تولید لوله درزدار
در این مقاله به فرایند تولید لوله درزدار پرداخته می شود و به شما کمک می کند که در زمان بسیار کوتاه به بررسی موضوع مقاله پرداخته و دانش خود را در این حوزه ارتقا دهید. این مقاله بر اساس آخرین ژورنالهای صنعت فولاد گردآوری شده و تلاش شده که با بیان خلاصه و روان به موضوع پرداخته شود.
فرایند تولید لوله درزدار
فرآیند تولید لولههای درزدار نقش حیاتی در صنایع فولادی و تولید لولهها دارد که در زمینههای متنوعی مانند نفت و گاز، آب و فاضلاب، ساختوساز، خودروسازی و دیگر صنایع کاربرد دارند. این لولهها از ورقهای فولادی تشکیل میشوند که در طول فرآیند تولید، لبههای آنها به هم جوش میخورند و به این ترتیب درز شکل میگیرد. برخلاف لولههای بدون درز (مکانیکال)، این نوع لولهها به دلیل روش تولید خاص خود، هزینه تولید کمتری دارند و بنابراین در بسیاری از کاربردهای صنعتی مورد توجه قرار میگیرند. در این مقاله فرایند تولید لوله درزدار مورد بررسی قرار می گیرد.
انتخاب مواد اولیه در فرایند تولید لوله درزدار
انتخاب مواد اولیه در فرآیند تولید لولههای درزدار نقش بسیار حیاتی دارد و بر کیفیت، هزینه و دوام نهایی لولهها تأثیرگذار است. برای انتخاب مواد اولیه مناسب، باید به خصوصیات فیزیکی و شیمیایی آنها توجه کرد تا در مراحل مختلف تولید، بهویژه در جوشکاری، تحت فشار و تنشهای مکانیکی به خوبی عمل کنند. در این انتخاب، نوع فلز و آلیاژ، ضخامت ورق فولادی، قابلیت جوشکاری، مقاومت در برابر خوردگی، قابلیت شکلدهی، هزینه مواد اولیه، تأمین منابع و موجودی مواد اولیه و ملاحظات زیستمحیطی بسیار مهم هستند. فولاد کربنی یکی از گزینههای رایج برای تولید لولههای درزدار است. این فلز خواص مکانیکی و قابلیت جوشکاری عالی دارد و به علت هزینه کمتر نسبت به دیگر آلیاژها، در تولید این نوع لولهها بسیار کاربردی است. علاوه بر فولاد کربنی، فولاد ضد زنگ برای ساخت لولههایی که به مقاومت بالا در برابر خوردگی نیاز دارند، استفاده میشود. همچنین آلیاژهای خاص فولادی که از ترکیب فولاد با عناصر دیگر مانند کروم، مولیبدن، نیکل و وانادیوم به دست میآیند، برای تولید لولههایی با ویژگیهای خاص مانند مقاومت در برابر دماهای بالا یا خوردگی شدید به کار میروند. ضخامت ورق فولادی مورد استفاده باید مطابق با نیازهای طراحی لوله باشد. ضخامت ورق مستقیماً بر استحکام و تحمل فشار لوله تأثیر دارد. برای مثال، لولههایی که در خطوط انتقال گاز یا نفت استفاده میشوند باید ضخامت بیشتری داشته باشند تا در برابر فشارهای بالا مقاوم باشند. قابلیت جوشکاری مواد اولیه در انتخاب آنها اهمیت زیادی دارد. زیرا لولههای درزدار از جوشکاری لبههای فولادی تولید میشوند؛ بنابراین انتخاب موادی با قابلیت جوشکاری بالا ضروری است. فولاد کربنی معمولاً خواص جوشکاری عالی دارد و به راحتی در فرآیند تولید لولههای درزدار قابل استفاده است. اما آلیاژهایی با مقادیر بالای عناصر آلیاژی مانند کروم یا نیکل ممکن است نیازمند فرآیندهای جوشکاری پیچیدهتری باشند. مقاومت در برابر خوردگی نیز یکی از عوامل کلیدی در انتخاب مواد اولیه برای تولید لولههای درزدار است. این ویژگی خصوصاً در صنایع نفت و گاز، شیمیایی و تأسیسات آب و فاضلاب اهمیت دارد. برای کاربردهایی که لولهها در شرایط محیطی خاص مانند رطوبت و مواد شیمیایی قرار دارند، استفاده از فولاد ضد زنگ یا آلیاژهای خاص با ویژگیهای ضد خوردگی ممکن است انتخاب بهتری باشد. قابلیت شکلدهی مناسب مواد اولیه نیز ضروری است تا بتوان آنها را به راحتی به شکل لوله تبدیل کرد. فلزاتی با قابلیت شکلدهی بالا اجازه میدهند فرآیند نورد و خمکاری مؤثر و بدون آسیبدیدگی انجام شود. علاوه بر این، هزینه مواد اولیه یکی از عوامل مهم در انتخاب فلز برای تولید لولههای درزدار است. برخی آلیاژها و فلزات مانند فولاد ضد زنگ یا آلیاژهای خاص ممکن است قیمت بالاتری داشته باشند که میتواند بر هزینه نهایی تولید تأثیر بگذارد. به همین دلیل از فولاد کربنی برای تولید لولههای درزدار عمومی استفاده میشود چون قیمت کمتری دارد و بهصورت گستردهای دردسترس است. دسترسی به مواد اولیه و تأمین بهموقع آنها اهمیت دارد. باید اطمینان یابیم که مواد اولیه از تأمینکنندگان معتبر تهیه شود تا کیفیت آنها تضمین گردد و تأمین بهموقع نیز بتواند از توقفهای ناخواسته در فرآیند تولید جلوگیری کند. با توجه به افزایش نگرانیهای زیستمحیطی، انتخاب مواد اولیه باید شامل توجه به تأثیرات زیستمحیطی تولید و بازیافت آنها باشد. استفاده از مواد اولیه با قابلیت بازیافت و کمترین اثر منفی بر محیط زیست میتواند به کاهش ردپای کربن و بهبود پایداری تولید کمک کند. انتخاب صحیح مواد اولیه برای تولید لولههای درزدار تأثیر زیادی بر کیفیت نهایی محصول و عملی بودن آن در محیطهای صنعتی مختلف دارد. مواد اولیه باید مطابق با خواص مکانیکی مورد نیاز، قابلیت جوشکاری، مقاومت در برابر خوردگی و هزینهها باشند تا لولههای تولید شده نهتنها از لحاظ اقتصادی مقرونبهصرفه باشند، بلکه عمر طولانی را نیز ساپورت نمایند.
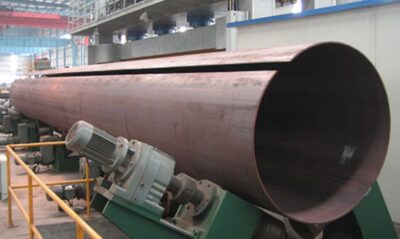
فرایند تولید لوله درزدار
آماده سازی ورق در فرایند تولید لوله درزدار
آمادهسازی ورق در تولید لولههای درزدار مرحلهای مهم است که طی آن، ورقهای فولادی پس از انتخاب اولیه و پیش از آغاز عملیات شکلدهی، به دقت برای جوشکاری و مراحل تولید دیگر آماده میشوند. این مرحله برای تضمین کیفیت بالا و هماهنگی دقیق در جوشکاری و شکلدهی بسیار اهمیت دارد. در ابتدا، ورقها باید به اندازههای دقیق بریده شوند. ورقهای فولادی معمولاً بزرگ و طولانی هستند و باید به ابعاد مناسب برای تولید لولههای درزدار تبدیل شوند. برش دقیق الزامی است تا لبههای ورقها بهدرستی با هم جفت شده و جوشکاری بهطور صحیح انجام شود. برای این منظور از دستگاههای برش لیزری یا مکانیکی استفاده میشود که امکان برش دقیق و تمیز را فراهم میکند. پس از برش، لبههای ورقها باید آماده شوند. این به معنی صاف و بینقص بودن لبههایی است که به یکدیگر جوش داده میشوند. عملیات پرداخت و پولیش میتواند در این زمینه مفید باشد تا لبهها بهطور کامل فیت شوند و هیچ ناهمواری یا آلایندهای در محل جوشکاری باقی نماند. زدودن زنگزدگی، روغن، آلودگی، یا هر نوع ناخالصی از سطح ورق ضروری است تا از وجود ضعف در جوشکاری جلوگیری شود. کنترل ضخامت ورقها از مراحل کلیدی آمادهسازی است و باید یکنواخت باشد؛ هرگونه تغییر در ضخامت ممکن است مشکلاتی در جوشکاری و شکلدهی لولهها ایجاد کند. این کنترل ضخامت معمولاً با ابزارهای اندازهگیری دقیق صورت میگیرد. پس از تکمیل این مراحل، ورقها وارد فرآیند شکلدهی میشوند. در این مرحله، ورقها باید به دقت و یکنواخت خم شوند تا لبهها مستقیم و در جای درست قرار گیرند. شکلدهی نامناسب میتواند مشکلاتی مانند جوشکاری یا برش نامطلوب لولهها ایجاد کند. بنابراین، این کار تحت شرایط کنترلشده و با تجهیزات دقیق انجام میشود. در نهایت، با آمادهسازی کامل ورقها، آنها جهت جوشکاری آماده میشوند. آمادگی دقیق ورقها باعث میشود که جوشکاری بهطور صحیح و با کیفیت بالا انجام شده و درزهای لولهها با دوام و دقت ایجاد شوند. برای مشاهده ورق سیاه کلیک کنید .
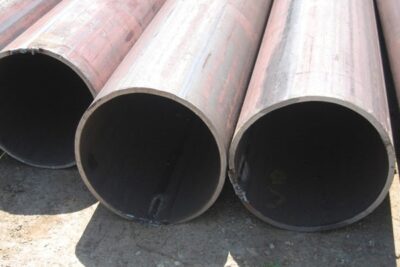
فرایند تولید لوله درزدار
عملیات شکل دهی لوله درزدار
در فرآیند تولید لولههای درزدار، عملیات شکلدهی یکی از مراحل اساسی است که طی آن ورقهای فولادی آماده شده به فرم لوله تبدیل میشوند. این گام برای ایجاد لولههایی با مشخصات هندسی دقیق و مناسب برای جوشکاری و سایر عملیاتهای تکمیلی ضروری است. باید این فرآیند به گونهای انجام شود که ورق فولادی به شکل یکنواخت و دقیق حول یک محور خم شود تا درزهای مورد نیاز برای جوشکاری به خوبی کنار هم قرار گیرند. شکلدهی لولههای درزدار عمدتاً با یکی از دو روش اصلی رولفرمینگ یا نورد صورت میگیرد. این روشها از دستگاههای ویژهای استفاده میکنند که ورق فولادی را به شکل دایرهای یا بیضی تبدیل میکنند. در روش رولفرمینگ، ورق فولادی بهطور پیوسته از میان مجموعه غلطکها عبور میکند که آن را به شکل لوله خم میکنند. در این مرحله، تنظیم دقیق غلطکها بسیار حیاتی است تا لبههای ورق به طور صحیح به یکدیگر نزدیک شوند. رولفرمینگ معمولاً برای تولید لولههایی با قطر و ضخامت مشخص کاربرد دارد. روش نورد شامل عبور ورق فولادی از میان رولهای نورد تحت فشار و حرارت بالا است. این فشار باعث ایجاد شکل یکنواخت و دقیق لوله میشود. نورد معمولاً برای تولید لولههایی با ضخامت بالا یا استحکام ویژه استفاده میگردد. در هر دو روش، لبههای ورق فولادی خم میشوند تا در فرآیند جوشکاری نهایی، لوله بدون نقص به هم جوش داده شود. کنترل دقیق دستگاهها برای اطمینان از اینکه شکل نهایی مطابق با ابعاد و ویژگیهای مورد نظر باشد، بسیار مهم است. همچنین، باید اطمینان حاصل شود که ورق تحت کشش یا فشاری قرار نمیگیرد که میتواند به آن آسیب بزند. کنترل کیفیت فرمدهی در این مرحله اهمیت زیادی دارد. باید بررسی شود که لولههای تولید شده دارای ابعاد یکنواخت و دایرهای باشند و هیچ نوع اعوجاج یا انحرافی در قطر یا طول وجود نداشته باشد. این کنترل غالباً با ابزارهای دقیق اندازهگیری اجرا میشود. با پایان عملیات شکلدهی، ورق فولادی به فرم لوله درآمده و آماده جوشکاری است. دقت در این مرحله تأثیر بنیادی بر کیفیت نهایی لولههای درزدار دارد و هرگونه نقص در شکلدهی ممکن است مشکلاتی در مراحل بعدی ایجاد کند، مانند جوشکاری و تستهای کیفیت.
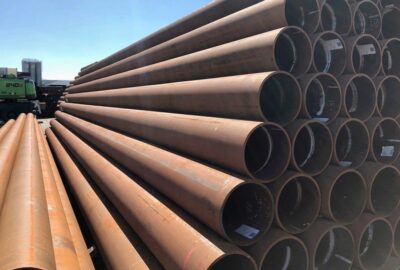
فرایند تولید لوله درزدار
جوشکاری لوله درزدار
جوشکاری در فرآیند تولید لولههای درزدار یک مرحله حیاتی است که در آن لبههای ورق فولادی با استفاده از تکنیکهای مختلف جوشکاری به هم متصل میشوند. هدف اصلی، ایجاد یک اتصال قوی و پایدار بین لبهها برای تولید لولهای مقاوم در برابر فشار و انواع نیروها است. در این فرآیند، روشهای مختلفی بهکار گرفته میشود، اما دو روش پرتکرار، جوشکاری مقاومتی و جوشکاری با گاز CO2 هستند. در روش جوشکاری مقاومتی، لبههای ورق با فشار و جریان الکتریکی نزدیک و بههم جوش میخورند. حرارت تولیدشده در اثر جریان الکتریکی باعث ذوبشدن لبهها و ایجاد اتصال میشود. این روش برای لولههای با ضخامت معمولی بسیار کارآمد و از سریعترین روشها در تولید لولههای درزدار محسوب میشود. در مقابل، جوشکاری با گاز CO2 از یک گاز محافظ مانند CO2 برای جلوگیری از آلودگی هوا و حفظ کیفیت جوش استفاده میکند. در این روش، الکترود و سیم جوش وارد ناحیه اتصال شده و از طریق قوس الکتریکی، لبهها را ذوب و اتصال میدهد. این تکنیک برای ضخامتها و شرایط مختلف کاربرد دارد و کیفیت بالایی در جوش ایجاد میکند. دقت در قرارگیری دقیق لبههای ورق قبل از جوشکاری بسیار حیاتی است تا از کیفیت بالای جوش اطمینان حاصل شود. این امر بهویژه برای لولههای تحت فشار یا استفاده در محیطهای حساس مانند صنایع نفت و گاز اهمیت دارد. کیفیت بالا نیازمند جلوگیری کامل از ترک یا نقص در جوش است. همچنین کنترل دقیق دما و فشار در فرآیند جوشکاری بسیار مهم است. تنظیم صحیح این پارامترها مستقیماً بر استحکام و کیفیت جوش تأثیر میگذارد. نامناسب بودن این تنظیمات ممکن است به جوش ضعیف یا غیر یکنواخت منجر شود که یک نقطه ضعف در لوله به شمار میآید. بعد از جوشکاری، آزمایشهایی مانند تست جوش و فشار باید انجام شود تا اطمینان حاصل شود که اتصال بدون نقص است. در صورت وجود نواقص، باید اقدام به اصلاح جوش گردد تا عملکرد مطلوب لولهها تضمین شود. در نهایت، جوشکاری نقشی اساسی در ایجاد اتصالات پایدار ایفا میکند، بهویژه که این لولهها اغلب در کاربردهای حساس نظیر سیستمهای گاز و نفت مورد استفاده قرار میگیرند، لذا دقت و کیفیت در این فرآیند بسیار حائز اهمیت است. برای مشاهده لوله بدون درز کلیک کنید.
تست و کنترل کیفیت لوله درزدار
در فرآیند تولید لولههای درزدار، تست و کنترل کیفیت مرحلهای بسیار مهم است که نقش اساسی در تضمین تطابق محصول نهایی با استانداردهای کیفی و عملکردی دارد. این نوع لولهها اغلب در صنایع حساس و پرخطر نظیر نفت، گاز، آب و فاضلاب و صنایع شیمیایی استفاده میشوند؛ بنابراین، اطمینان از ویژگیهایی چون استحکام، مقاومت در برابر فشار و خوردگی اهمیت فراوانی دارد. طی این مرحله، انواع آزمایشها و بازرسیها صورت میگیرند که به تأیید کیفیت لولههای تولید شده کمک میکنند. یکی از اصلیترین آزمایشها، بررسی جوشها است که در آن نقاط جوش بین لبههای ورقها ارزیابی میشود تا از اتصال مناسب و کافی آنها اطمینان حاصل شود. این ارزیابی ممکن است شامل بازرسی بصری و آزمایشهای غیرمخرب مانند اولتراسونیک یا رادیوگرافی باشد تا نواقص احتمالی مثل ترکها، حبابها و نقاط ضعیف شناسایی شوند. آزمایش فشار نیز نقش حیاتی دارد و در آن لولهها تحت فشارهای مختلف قرار میگیرند تا مشخص شود آیا جوشها و ساختار لوله توانایی تحمل فشار در شرایط عملیاتی را دارند یا نه. این آزمایش عمدتاً برای لولههایی که در صنایع نفت و گاز کاربرد دارند ضروری است. لولهها به فشار معین رسانده شده و عدم تحمل فشار منجر به رد آنها میشود. آزمایش ابعادی نیز بخش مهمی از فرایند است که طی آن ابعاد شامل قطر، طول، ضخامت و همراستایی لولهها با دقت محاسبه میشود تا از مطابقت با استانداردها و مشخصات طراحی اطمینان حاصل شود. حتی کوچکترین تغییرات در ابعاد میتواند بر عملکرد و استحکام لوله تأثیرگذار باشد. آزمایش سختی برای مقاومت فلز در برابر خراشیدگی و فرسایش انجام میشود. معمولاً از دستگاههای سختیسنج استفاده شده تا میزان مقاومت لولهها در برابر سایش و شرایط محیطی مختلف ارزیابی گردد. آزمایش مقاومت به خوردگی برای لولههایی کاربرد دارد که در محیطهای خورنده یا مرطوب مورد استفاده قرار میگیرند. این بررسی معمولاً شامل آزمون در شرایط شیمیایی خاص است و به ویژه در صنایعی چون شیمیایی یا نفتی اهمیت دارد. علاوه بر این آزمایشها، بررسیهای بصری نیز صورت میگیرد که به شناسایی هر گونه عیب سطحی، ترک یا دندانههای غیرمجاز روی لوله کمک میکند؛ این ارزیابی شامل مشاهده دقیق جوشها، لبهها و سطح کلی لوله میشود. تمام این تستها باید با ابزارها و تجهیزات دقیق به طور مداوم انجام شوند تا تضمین شود لولههای تولیدی باکیفیت بوده و آماده استفاده در صنایع مختلف هستند. این فرایند کنترل کیفیت برای تضمین عملکرد و ایمنی ضروری است، زیرا لولهها معمولاً تحت شرایط چالشبرانگیزی مانند فشار بالا، دماهای گوناگون و محیطهای خورنده قرار میگیرند.
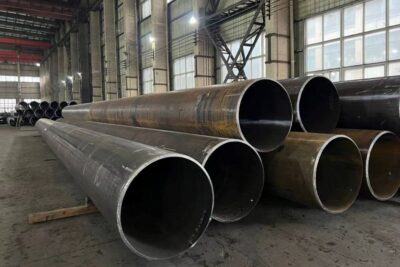
فرایند تولید لوله درزدار
فرآیندهای تکمیلی در فرایند تولید لوله درزدار
در تولید لولههای درزدار، مجموعهای از عملیات تکمیلی پس از جوشکاری و تست کیفیت انجام میشود تا ویژگیهای نهایی لولهها بهبود یابد و برای استفاده در صنایع مختلف آماده شوند. این فرآیندها با هدف افزایش استحکام، بهبود ظاهر، مقاومت در برابر خوردگی، افزایش دقت ابعادی و ارتقاء کیفیت محصول نهایی صورت میگیرند. در ادامه، به بررسی چندین فرآیند تکمیلی معمول در تولید لولههای درزدار میپردازیم. یکی از این فرآیندها، پرداخت سطح است که برای بهبود کیفیت سطح لولهها و حذف عیوبی مانند خراشها، زنگزدگیها و آلودگیهای ناشی از جوشکاری یا دیگر عملیاتها انجام میشود. این پرداخت شامل روشهایی نظیر سمبادهزنی، پولیش، برش لبهها و لایهبرداری سطحی است که باعث ایجاد ظاهر یکنواخت و پاکیزه در لولهها میشود و عملکرد آنها را بهبود میبخشد. فرآیند مهم دیگری آبکاری یا پوششدهی لولههاست که برای کاربرد در محیطهای خورنده یا شرایط خاص ضروری است. آبکاری فلزات مانند گالوانیزه کردن، رایجترین روش جلوگیری از خوردگی در محیطهای مرطوب یا شیمیایی محسوب میشود. این پوششدهی معمولاً با فلزی مقاوم مانند روی انجام میشود تا اثرات خوردگی را کاهش دهد. علاوه بر این، برای مقاومت لولهها در برابر شرایط خاص مثل دماهای بالا یا مواد شیمیایی ویژه، پوششهایی از جنس نیکل، کروم یا مواد ضد خوردگی بکار میرود. گرم کردن یا آنیل کردن، فرآیند دیگری است که به بهبود خواص مکانیکی لولهها کمک میکند. در این روش، لولهها تا دمای معینی گرم و سپس به آرامی خنک میشوند تا ساختار میکروسکوپی فلز تغییر کرده و خصوصیات آن ارتقاء یابد. این عمل برای لولههایی که فشار زیادی متحمل میشوند یا در دماهای بالا مورد استفاده قرار میگیرند، اهمیت دارد و موجب افزایش انعطافپذیری و کاهش شکنندگی فلز میشود. خمکاری نیز یک فرآیند تکمیلی است که طی آن لولهها به شکلهای منحنی یا زاویهدار خم میشوند. این عملیات برای لولههایی که در سیستمهای پیچیده نیاز به انحنا خاص دارند، انجام میشود و باید با دقت صورت گیرد تا از شکستن یا آسیب جلوگیری شود. در برخی موارد، پس از عملیات جوشکاری و پرداخت، فرآیندهای سردسازی یا شکلدهی سرد برای دقت ابعادی بیشتر مورد نیاز است. این فرآیند شامل اعمال فشار یا کشش بر روی لولهها است که باعث تغییرات ابعادی نهایی میشود و مخصوصاً هنگامی که دقت ابعادی بالا ضرورت دارد کاربرد دارد. در نهایت، لولهها بهمنظور حفاظت از آسیبدیدگی در حین حمل و نقل و ذخیرهسازی مناسب بستهبندی میشوند. این بستهبندیها اغلب از مواد مقاوم و ضد ضربه ساخته شدهاند تا از خرابی لولهها جلوگیری کنند. تمامی این فرآیندهای تکمیلی جهت بهبود کیفیت نهایی و تضمین عملکرد صحیح لولههای درزدار در محیطهای صنعتی مختلف انجام میشوند. این اقدامات به تقویت مقاومت لولهها در برابر فشار، خوردگی، سایش و سایر شرایط دشوار محیطی کمک کرده و عمر مفید آنها را افزایش میدهند برای مشاهده تیرآهن کلیک کنید .
بستهبندی و ارسال لوله درزدار
بستهبندی و ارسال لولههای درزدار یکی از مراحل پایانی تولید است که برای حفظ کیفیت و ایمنی محصولات در حمل و نقل و نگهداری انجام میشود. این مرحله اهمیت زیادی دارد، زیرا لولهها در اندازهها و ضخامتهای مختلف تولید میشوند و باید بهگونهای بستهبندی شوند که از آسیب، خش یا هرگونه نقص احتمالی در حین انتقال جلوگیری شود. این فرآیند شامل چند مرحله مهم است که باید با دقت انجام شوند. ابتدا، پس از پایان تولید و آزمایشهای کیفی، لولهها بهطور دقیق بررسی میشوند تا از نبود نقص یا آسیب سطحی مطمئن شویم. پس از این بررسی، لولهها وارد مرحله بستهبندی میشوند. یکی از روشهای متداول بستهبندی، استفاده از بستهبندی فلهای است که در آن لولهها بهطور مستقیم کنار یکدیگر قرار گرفته و بستهبندی میشوند. برای این منظور از حلقههای فلزی یا رابطهای چوبی برای جمعآوری و نگهداری لولهها استفاده میشود. این روش معمولاً برای لولههای با اندازه مشابه و کاربردهای عمومی مناسب است. در مواقعی که لولهها باید تحت شرایط خاص نگهداری شوند یا حجم سفارشات زیاد است، بهصورت مجموعهای در پالتهای فلزی یا چوبی بستهبندی میشوند. این پالتها بهگونهای طراحی شدهاند که لولهها بهطور ایمن و مرتب قرار گیرند و از ضربه و آسیب جلوگیری شود. استفاده از پالتها علاوه بر ایمنی در حمل و نقل، ذخیرهسازی را نیز آسانتر میکند. برای لولههایی که نیاز به محافظت بیشتری دارند، ممکن است از لایههای حفاظتی مانند پلاستیک ضد ضربه، فویلهای محافظ یا غلافهای پلاستیکی استفاده شود. این پوششها مخصوصاً برای لولههایی که حساسیت بیشتری به آسیب دارند، ضروری است. همچنین، برخی لولهها برای کاربردهای صنعتی حساس یا پروژههای بزرگ، ممکن است با برچسبهای هشداردهنده و دستورالعملهای حمل خاص بستهبندی شوند. پس از بستهبندی، فرآیند انتقال آغاز میشود. در این مرحله، لولهها برای ارسال به مقصد نهایی آماده میشوند که شامل بارگیری بر روی وسایل حمل مانند کامیونها، کشتیها یا قطارها است. باید اطمینان حاصل شود که لولهها ایمن قرار گرفتهاند تا از جابهجایی و آسیب جلوگیری شود. در نهایت، برای حفظ کیفیت لولهها در حمل و نقل، نظارت بر شرایط حمل همچون دما، رطوبت و جلوگیری از آسیب محیطی ضروری است. برخی لولهها ممکن است بهطور ویژه در شرایط خاص منتقل شوند که نیاز به تدابیر حفاظتی خاص دارند. مدیریت و پیگیری ارسال نیز بسیار مهم است. برای اطمینان از رسیدن لولهها بهموقع و صحیح به مقصد، استفاده از سیستمهای ردیابی محموله و مدیریت حمل و نقل ضروری است. این سیستمها به مشتریان و تولیدکنندگان امکان میدهند تا وضعیت ارسال را پیگیری کنند و مطمئن شوند که محموله بهموقع میرسد. در مجموع، فرآیند بستهبندی و ارسال لولههای درزدار اهمیت بالایی دارد و باید با دقت انجام شود تا محصول سالم و بدون نقص به مقصد برسد.