فرآیند تولید ورق گالوانیزه
در این مقاله به فرآیند تولید ورق گالوانیزه پرداخته می شود و به شما کمک می کند که در زمان بسیار کوتاه به بررسی موضوع مقاله پرداخته و دانش خود را در این حوزه ارتقا دهید. این مقاله بر اساس آخرین ژورنالهای صنعت فولاد گردآوری شده و تلاش شده که با بیان خلاصه و روان به موضوع پرداخته شود.
فرآیند تولید ورق گالوانیزه
فرآیند تولید ورق گالوانیزه شامل مجموعهای از مراحل پیچیده و دقیق است که هدف آن پوشاندن لایهای از فلز روی بر روی ورقهای فولادی میباشد تا از خوردگی و زنگزدگی محافظت شود. این فرآیند عمدتاً در صنایع فولاد و فلزات انجام شده و یکی از مهمترین روشهای ایجاد پوشش محافظ برای قطعات فلزی به شمار میرود. بهدلیل ویژگیهای منحصر به فرد مانند مقاومت بالا در برابر شرایط جوی، طول عمر زیاد و سهولت در استفاده، ورق گالوانیزه به یکی از پرکاربردترین نوع ورقها تبدیل شده است. ابتدا ورقهای فولادی آمادهسازی میشوند. این ورقها، معمولاً تولید شده از نورد گرم یا سرد، باید پیش از گالوانیزهکردن کاملاً تمیز شوند. برای این کار، ورقها در حمامهای شیمیایی با محلولهای اسیدی غوطهور میشوند تا آلودگیها، روغنها و زنگ از سطح آنها پاک شود. اهمیت این مرحله به دلیل تأثیر مستقیم بر کیفیت نهایی پوشش گالوانیزه آشکار است، چرا که آلودگی میتواند چسبندگی فلز روی به سطح فولاد را کاهش دهد. پس از تمیزکاری، ورقهای فولادی به مرحله گالوانیزهکردن منتقل میشوند. روش “غوطهوری گرم” یا Hot-Dip Galvanizing یکی از رایجترین روشها است. در این روش، ورقها در حمام مذاب روی با دمای حدود ۴۵۰ درجه سانتیگراد غوطهور میشوند. در این حالت، فلز روی با سطح فولاد واکنش داده و لایهای ضخیم و مقاوم تشکیل میشود که علاوه بر محافظت خوردگی، خواص مکانیکی و ظاهری فولاد را ارتقا میبخشد. پس از خروج ورقها از حمام روی، مرحله سردکردن و خشککردن آغاز میشود. ورقها سریعاً در جریان هوا یا در تونلهای خنککننده قرار گرفته تا لایه روی سفت و پایدار شود. فرآیند سردکردن نقش اساسی در کیفیت و ضخامت نهایی پوشش دارد. گاهی اوقات برای دستیابی به سطحی صافتر، ورقها از دستگاههای خاص عبور داده میشوند. در پایان فرآیند گالوانیزهکردن، ورقها ممکن است تحت عملیاتهای تکمیلی قرار گیرند. این شامل سنگزنی، پرداخت، رنگآمیزی یا پوششدهی اضافی است که خواص سطحی را بهبود میبخشد. چنین کارهایی نه تنها ظاهر ورق را ارتقا میدهند بلکه مقاومت آن در برابر عوامل محیطی نظیر UV، آلودگیهای شیمیایی و رطوبت را افزایش میدهند. به طور کلی، فرآیند تولید ورق گالوانیزه به دقت بالا و رعایت استانداردهای کیفی نیاز دارد تا مشخصات مطلوب مانند مقاومت به خوردگی و دوام را تحقق بخشند. این ورقها در صنایعی نظیر ساختمانسازی، خودروسازی، لوازم خانگی و کشاورزی بهعنوان یکی از بهترین گزینهها برای محیطهای سخت و مرطوب شناخته میشوند.
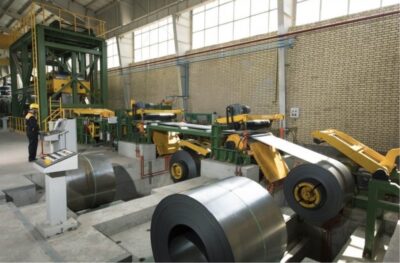
فرآیند تولید ورق گالوانیزه
روش های مختلف فرآیند تولید ورق گالوانیزه
فرآیند گالوانیزهکردن مجموعهای از تکنیکها است که برای پوشش دادن سطوح فلزی، بهخصوص فولاد، با لایهای از روی (زینک) جهت جلوگیری از خوردگی و زنگزدگی به کار میرود. یکی از پرکاربردترین روشها، گالوانیزهکردن به روش غوطهوری گرم است. در این روش، قطعات فولادی به صورت کامل در حمام روی مذاب قرار میگیرند که دمای آن معمولاً حدود ۴۵۰ درجه سانتیگراد است. پس از غوطهوری، لایهای ضخیم از روی بر سطح فولاد شکل میگیرد که مقاومت آن را در برابر خوردگی و شرایط جوی به میزان زیادی افزایش میدهد. این روش معمولاً برای ورقهای فولادی و قطعات بزرگ استفاده میشود و از مزایای آن میتوان به پوششدهی یکنواخت و طول عمر بالا اشاره کرد، هرچند ممکن است لایه روی در برخی نقاط نازکتر باشد. روش دیگری که برای گالوانیزهکردن استفاده میشود، گالوانیزهکردن الکتریکی است. در این روش، از جریان الکتریکی برای انتقال یونهای روی به سطح فولاد بهره میگیرند. ورقهای فولادی در محلول الکترولیتی حاوی یونهای روی قرار داده میشوند و سپس با اعمال جریان برق، لایهای نازک و یکنواخت از روی بر سطح آنها نشسته میشود. این روش نسبت به غوطهوری گرم لایههای نازکتری ایجاد میکند و بیشتر برای محصولاتی با دقت بالا و نیاز به پوشش کم ضخامت مناسب است. همچنین مزایای اقتصادی دارد و برای تولید قطعات با ابعاد کوچک و پیچیدهتر کاربرد دارد. گالوانیزهکردن مکانیکی یک روش دیگر است که در آن از پودر روی برای پوششدهی سطح فولاد استفاده میشود. در این تکنیک، قطعات فولادی در دستگاهی قرار میگیرند که پودر روی تحت فشار به سطح قطعه پرتاب میشود. این فرآیند نیازی به دمای بالا ندارد و نسبت به برخی روشها هزینه کمتری دارد. با این حال، پوشش ایجاد شده معمولاً نازکتر است و ممکن است کیفیت کمتری داشته باشد. این روش بیشتر برای قطعات کوچکتر و پیچیدهتر که با روشهای دیگر امکان پوششدهی ندارند، مناسب است. گالوانیزهکردن اسپری نیز یکی دیگر از روشهای کاربردی است که در آن پودر روی با اسپری به سطح فولاد پاشیده شده و سپس با حرارت ذوب میشود تا لایهای از روی به سطح فلز بچسبد. این روش بیشتر برای قطعات بزرگ یا قطعاتی با شکلهای پیچیده استفاده میشود و به خصوص برای عملیاتهایی که زمان کمی نیاز دارند مناسب است؛ هرچند کنترل ضخامت پوشش در این روش کمتر دقیق است. در نهایت، گالوانیزهکردن پیوسته یا Continuous Hot-Dip Galvanizing روشی است که ورقهای فولادی بهطور پیوسته از میان حمام روی مذاب عبور میکنند. این تکنیک عمدتاً برای تولید ورقهای گالوانیزه با ضخامت یکنواخت و در مقیاس وسیع استفاده میشود. ورقهای فولادی از یک خط تولید پیوسته عبور کرده و پس از خروج از حمام روی، سریعاً سرد میشوند. این روش در تولید ورقهای گالوانیزه با کیفیت بالا و ضخامت دقیق مناسب است اما برای قطعات با اندازههای خاص کاربرد ندارد. هر یک از این روشها بر اساس نوع محصول، نیاز به ضخامت لایه روی و هزینهها انتخاب میشود. در مجموع، هدف اصلی گالوانیزهکردن ایجاد لایهای مقاوم از روی است که فلز را در برابر خوردگی و تغییرات جوی محافظت کند. برای مشاهده ورق سیاه کلیک کنید.
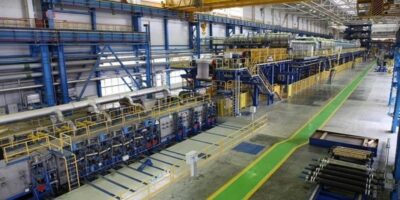
فرآیند تولید ورق گالوانیزه
مزایای ورق گالوانیزه
ورق گالوانیزه به دلیل ویژگیهای ممتازی که دارد، در صنایع مختلف بسیار پرطرفدار است. از مهمترین مزایای آن میتوان به مقاومت بالای آن در برابر زنگزدگی و خوردگی اشاره کرد. این ویژگی در محیطهای مرطوب و شرایط جوی سخت بسیار حائز اهمیت است، زیرا لایه محافظ روی باعث میشود فولاد از تماس با عوامل خورنده در امان بماند و طول عمر قطعات فلزی افزایش یابد. علاوه بر این، ورقهای گالوانیزه نسبت به ورقهای فولادی بدون پوشش، دوام بیشتری دارند که این امر هزینههای نگهداری و تعمیرات را در طولانیمدت کاهش میدهد. یکی دیگر از مزایای ورق گالوانیزه، سهولت در استفاده و شکلدهی است. این ورقها به راحتی در فرآیندهای تولید مانند برش، خمکاری و جوشکاری قابل استفاده هستند بدون اینکه به لایه روی آنها آسیبی وارد شود. این ویژگی در صنایع خودروسازی و ساختمانسازی بسیار مهم است، زیرا میتوان به راحتی از آنها برای ساخت قطعات پیچیده بهره برد. ورق گالوانیزه به دلیل ظاهر زیبا و درخشانش نیز محبوبیت دارد. این خصوصیت ظاهری در طراحی داخلی و صنایع معماری که علاوه بر عملکرد، زیبایی نیز مدنظر است، کاربرد زیادی دارد. همچنین این ورقها به راحتی رنگ پذیر هستند و میتوانند در رنگهای مختلف برای هماهنگی با نیازهای طراحی استفاده شوند. علاوه بر این، ورقهای گالوانیزه مقاومت خوبی در برابر آسیبهای فیزیکی دارند. لایه روی آنها باعث میشود در برابر خراشیدگی و سایش مقاومتر از ورقهای فولادی معمولی باشند که برای مصارف صنایع خانگی، کشاورزی و حملونقل بسیار مفید است. در نهایت، مقاومت بالای ورق گالوانیزه در برابر عوامل شیمیایی از دیگر نقاط قوت آن است. این ورقها در برابر رطوبت، آلودگیهای شیمیایی و اسیدها مقاوماند و از همین رو در محیطهای صنعتی که با مواد شیمیایی سر و کار دارند بسیار کارآمد هستند. این ویژگی علاوه بر افزایش دوام محصولات، نیاز به تعمیر و تعویض مکرر را نیز کاهش میدهد. برای مشاهده تیرآهن کلیک کنید.
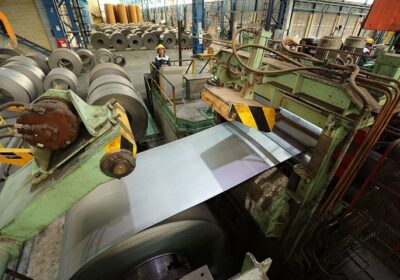
فرآیند تولید ورق گالوانیزه
بسته بندی و فرآیند تولید ورق گالوانیزه
بستهبندی ورق گالوانیزه یکی از مراحل کلیدی پس از تولید محسوب میشود که تأثیر قابلتوجهی بر حفظ کیفیت محصول در حملونقل، انبارداری و تحویل به مشتری دارد. این ورقها که معمولاً بهصورت رول یا برشخورده عرضه میشوند، به علت پوشش روی، نیازمند مراقبت ویژهای هستند تا از آسیبهای فیزیکی، رطوبت، گرد و غبار و خوردگی محافظت شوند. در ابتدا، ورقهای گالوانیزه با تسمههای فلزی یا پلاستیکی بسته میشوند تا از باز شدن رول یا جابهجایی آنها جلوگیری شود. برای حفاظت بیشتر، یک لایه پوششی مانند کاغذ ضد رطوبت یا نایلون ضخیم به دور آن پیچیده میشود. گاهی از کاغذ کرپ یا ضدزنگ هم جهت جلوگیری از تماس مستقیم رطوبت با سطح ورق استفاده میشود. برای کاهش آسیبهای فیزیکی در حملونقل، لبهها و گوشههای رول با محافظهای فلزی یا مقوایی پوشانده میشوند. قسمت مرکزی کویل نیز، که روی پالت قرار میگیرد، ممکن است با بوشی مقاوم پوشیده شود تا در برابر فشارهای مکانیکی محافظت شود. همچنین استفاده از پالتهای چوبی یا فلزی برای قرار دادن ورقها یا کویلها مرسوم است. این کار امکان جابهجایی آسان با لیفتراک یا جرثقیل را فراهم کرده و تماس مستقیم محصول با زمین را کاهش میدهد. در موارد صادرات یا نگهداری طولانی، ممکن است از پوششهای ضد خوردگی یا روغنهای محافظ استفاده شود. در انتها، برچسبهایی شامل مشخصات محصول مانند ضخامت، عرض، وزن، شماره سری تولید و تاریخ تولید بر روی بستهبندی قرار میگیرد. این اطلاعات برای شناسایی سریع محصول و مدیریت موجودی و کنترل کیفیت ضروری هستند. بستهبندی صحیح ضامن حفظ کیفیت ورق گالوانیزه تا زمان مصرف نهایی آن است.
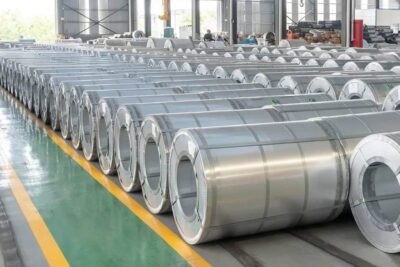
فرآیند تولید ورق گالوانیزه
حمل و نقل ورق گالوانیزه
حمل و نقل ورق گالوانیزه به دلیل ویژگیهای خاص این نوع ورق نیازمند رعایت استانداردها و دقت زیادی است تا سطح پوشش روی آن بدون آسیب بماند و از تغییر شکل مکانیکی جلوگیری شود. چه ورقها بهصورت رول (کویل) و چه بهصورت برشخورده باشند، باید به گونهای جابهجا شوند که کیفیت سطحی آنها حفظ شود و از رطوبت، ضربه یا آلودگی در امان بمانند. یکی از مهمترین جوانب در حمل و نقل این ورقها، استفاده از بستهبندی مقاوم است. کویلهای گالوانیزه معمولاً با تسمههای فلزی یا پلاستیکی محکم بسته میشوند و با موادی ضد رطوبت مانند نایلون ضخیم یا کاغذ کرپ پوشانده میشوند. این لایهها از نفوذ رطوبت و گرد و غبار به سطح ورق جلوگیری کرده و مانع اکسید شدن روی میشوند. همچنین، برای محافظت از لبهها، از ضربهگیرهای مقوایی یا فلزی مخصوص استفاده میشود. در فرآیند بارگیری و تخلیه، ابزارهایی مانند جرثقیل، لیفتراک یا گیرههای مخصوص به کار میرود تا از فشار غیرضروری بر روی ورق جلوگیری شود. کشیدن یا غلطاندن مستقیم ورق بر روی سطوح سخت میتواند موجب خطوخش یا تخریب لایهی گالوانیزه شود. بنابراین، توصیه میشود که سطوح تماس نرم و ایمن باشند یا از پالتهای چوبی برای زیرسازی استفاده شود. انتخاب وسیلهی نقلیه مناسب نیز بسیار حائز اهمیت است. برای حمل زمینی، استفاده از کامیونهایی با کف مسطح و دارای پوشش مناسب توصیه میشود. در صورتی که حمل در فضای باز صورت گیرد، باید از چادرهای ضد آب برای پوشش بار بهره برد تا در برابر باران، گرد و خاک و تابش آفتاب محافظت شود. در حملونقل دریایی، استفاده از کانتینرهای دربسته و تهویهدار به منظور جلوگیری از تعریق و خوردگی توصیه میشود. نکته دیگری که باید در نظر گرفته شود، نگهداری صحیح طی توقف یا پیش از تخلیه است. ورقهای گالوانیزه نباید در مکانهای مرطوب یا بدون تهویه مناسب نگهداری شوند، چرا که احتمال تعریق داخلی و سفیدک زدن وجود دارد. همچنین، انباشتن کویلها بهصورت ناپایدار یا روی یکدیگر میتواند باعث دفرمه شدن یا آسیب به لبهها شود. در مجموع، حمل و نقل اصولی ورق گالوانیزه مانع از کاهش کیفیت و آسیبدیدگی شده و رضایت مشتری را تضمین میکند، همچنین باعث کاهش هزینههای ناشی از برگشت کالا یا تعمیر محصول میشود. برای مشاهده پروفیل ساختمانی کلیک کنید.