تفاوت سنگ آهن با آهن اسفنجی
در این مقاله به تفاوت سنگ آهن با آهن اسفنجی پرداخته می شود و به شما کمک می کند که در زمان بسیار کوتاه به بررسی موضوع مقاله پرداخته و دانش خود را در این حوزه ارتقا دهید. این مقاله بر اساس آخرین ژورنالهای صنعت فولاد گردآوری شده و تلاش شده که با بیان خلاصه و روان به موضوع پرداخته شود.
تفاوت سنگ آهن با آهن اسفنجی
تفاوت سنگ آهن با آهن اسفنجی از نظر تعریف و ویژگیهای فیزیکی با یکدیگر بسیار زیاد است که درک آنها برای آشنایی با زنجیره تولید فولاد بسیار مهم است. سنگ آهن یک ماده معدنی طبیعی است که از معادن استخراج میشود و بهصورت سنگهای سخت یا خاکهای با رنگهای قهوهای، خاکستری یا قرمز یافت میشود. ترکیب اصلی آن شامل اکسیدهای آهن مانند مگنتیت (Fe₃O₄)، هماتیت (Fe₂O₃) و لیمونیت است. این ماده خام دارای ناخالصیهایی مانند سیلیس، آلومینا و گوگرد است که باید در مراحل فرآوری کاهش یا حذف شوند. شکل فیزیکی آن بسته به فرآیند آمادهسازی میتواند به صورت کلوخه، گندله یا کنسانتره باشد. در مقابل، آهن اسفنجی محصولی نیمهنهایی و فرآوریشده است که از احیای مستقیم سنگ آهن بدون ذوب شدن تولید میشود. ساختار آن متخلخل و شبیه به اسفنج است، به همین دلیل این نام را دارد. رنگ آن معمولاً خاکستری تیره با سطحی مات است. این محصول بهطور مستقیم از گندله یا کنسانتره سنگ آهن و تحت تأثیر گازهای احیاکننده مانند گاز طبیعی یا گازهای سنتزی ساخته میشود. شکل ظاهری آن عمدتاً به صورت گلولههای کوچک یا بریکتهای فشرده حساس به حمل عرضه میشود. در نهایت، میتوان گفت سنگ آهن مادهای خام و طبیعی است، در حالی که آهن اسفنجی محصولی فرآوریشده و صنعتی با درصد خلوص بالاتر است که یک گام نزدیکتر به فولاد نهایی محسوب میشود. برای مشاهده ورق سیاه کلیک کنید.
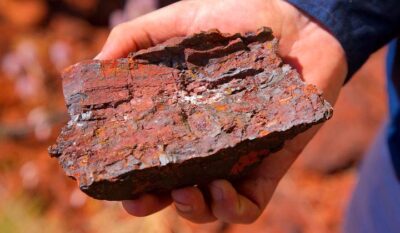
تفاوت سنگ آهن با آهن اسفنجی
فرآیند تولید آهن اسفنجی و سنگ آهن
فرایندهای تولید سنگ آهن و آهن اسفنجی هر دو در صنایع فولادسازی اهمیت ویژهای دارند. تولید سنگ آهن با استخراج آن از معادن آغاز میشود. سنگهای بزرگ استخراجشده، بهطور طبیعی حاوی اکسیدهای آهن و ناخالصیهایی مانند سیلیس، آلومینا و فسفر هستند. پس از استخراج، این سنگها از طریق روشهایی چون خردایش، آسیاب و جداسازی مغناطیسی، به ذرات کوچکتر تبدیل میشوند. سپس در فرایند کنسانترهسازی، این ذرات به ترکیباتی با غلظت بالای آهن تبدیل میگردند. در ادامه، بنا بر نیاز تولید، سنگ آهن بهصورت گندله یا دانهدرشت وارد کورههای ذوب میشود. در این مرحله، سنگ آهن معمولاً با کک و موادی دیگر مانند سنگ آهک ترکیب شده و در دمای مناسب ذوب میشود تا آهن خام تولید شود. این ذوبریزی معمولاً در کورههای بلند یا احیا انجام میگیرد و در طی آن، ناخالصیها به صورت سرباره جدا میشوند. در مقابل، فرایند تولید آهن اسفنجی براساس احیای مستقیم صورت میگیرد. در این فرایند، سنگ آهن آمادهشده به شکل گندله یا کنسانتره در کورههای احیا با گاز طبیعی یا کربن واکنش میدهد. این واکنش که در دمای پایینتر از نقطه ذوب (حدود ۸۰۰ تا ۱۰۰۰ درجه سانتیگراد) انجام میشود، باعث حذف اکسیژن از اکسید آهن شده و آهن را بهصورت جامد و متخلخل تولید میکند؛ به این حالت آهن اسفنجی میگویند. ویژگیهای متخلخل بودن این نوع آهن به آن شکلی خاص داده و برای تولید فولاد در واحدهای کوره قوس الکتریکی استفاده میشود. تفاوتهای عمده در این دو روش شامل فرایند ذوب است. سنگ آهن از طریق فرایندهای سنتی در کوره بلند به آهن خام تبدیل میشود که انرژی زیادی نیاز دارد. اما آهن اسفنجی با احیای مستقیم و مصرف انرژی کمتر تولید میشود. این روش بدون نیاز به ذوب کردن انجام شده و محصول نهایی بهصورت جامد باقی میماند. در مجموع، تولید آهن اسفنجی روشی بهینهتر با آلایندگی کمتر محسوب میشود و به همین دلیل برای تولید فولاد در کورههای قوس الکتریکی بسیار مناسب است.
درصد خلوص و ترکیب شیمیایی آهن اسفنجی و سنگ آهن
در فرآیند تولید سنگ آهن و آهن اسفنجی، نظارت بر خلوص و ترکیب شیمیایی مواد اهمیت بسیاری دارد، زیرا این عوامل تأثیر مستقیمی بر کیفیت و کارایی فرآیند تولید فولاد دارند. معمولاً، سنگ آهن حاوی مقدار زیادی ناخالصی است که باید در مراحل مختلف تولید کاهش یابند تا به فولادی با کیفیت بالا دست یابیم. سنگ آهن بهطور معمول دارای ۵۰ تا ۶۵ درصد آهن است و بقیه آن شامل ناخالصیهایی مانند سیلیس (SiO2)، آلومینا (Al2O3)، گوگرد (S) و فسفر (P) است. این ناخالصیها میتوانند تأثیر منفی بر کیفیت فولاد داشته باشند؛ برای مثال، حضور سیلیس و آلومینا باعث کاهش استحکام فولاد میشود، در حالی که گوگرد و فسفر باعث کاهش داکتیلیته و افزایش شکنندگی میشوند. به همین دلیل، در فرآیند ذوب سنگ آهن در کوره بلند، از سنگ آهک (CaCO3) برای جذب ناخالصیها و تبدیل آنها به سرباره استفاده میشود. سربارهها بهعنوان ضایعات از کوره جدا میشوند و در نتیجه فولاد استخراج میشود. در فرآیند تولید آهن اسفنجی، که شامل احیای مستقیم سنگ آهن است، خلوص آهن بهطور قابل توجهی بالاتر از سنگ آهن است. آهن اسفنجی معمولاً شامل ۸۴ تا ۹۴ درصد آهن است که این درصد بیشتر باعث میشود این محصول از نظر شیمیایی آمادهتر برای تولید فولاد باشد. همچنین، در فرآیند احیای مستقیم، گاز طبیعی یا گاز سنتزی به عنوان عامل احیاکننده استفاده میشود که اکسیژن را از اکسید آهن جدا کرده و آهن را بهصورت جامد و متخلخل تولید میکند. این ساختار متخلخل به آهن اسفنجی امکان جذب بهتر در کورههای قوس الکتریکی را میدهد و بنابراین تبدیل آن به فولاد مؤثرتر است. ترکیب شیمیایی آهن اسفنجی معمولاً شامل مقادیری از عناصر آلیاژی و ناخالصیهایی مانند سیلیس و فسفر است که بسته به منبع سنگ آهن و روش تولید متغیر هستند. برای تولید فولاد با کیفیت بالا، این ناخالصیها باید در حداقل میزان خود باشند تا تأثیر منفی بر خواص فیزیکی و مکانیکی فولاد نگذارند. علاوه بر این، آهن اسفنجی معمولاً بهطور مستقیم در واحدهای مدرن فولادسازی مانند کورههای قوس الکتریکی استفاده میشود که امکان کنترل دقیقتری بر ترکیب شیمیایی فولاد نهایی فراهم میکند. در نهایت، نظارت دقیق بر خلوص و ترکیب شیمیایی سنگ آهن و آهن اسفنجی در مراحل مختلف تولید باعث بهبود کیفیت محصول نهایی میشود و بهعنوان یکی از عوامل کلیدی در بهینهسازی فرآیند تولید فولاد محسوب میشود. برای مشاهده تیرآهن کلیک کنید.
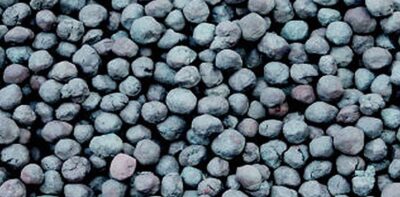
تفاوت سنگ آهن با آهن اسفنجی
کاربرد صنعتی آهن اسفنجی و سنگ آهن
سنگ آهن و آهن اسفنجی هر کدام نقشهای خاصی در صنعت فولادسازی دارند و استفاده از آنها بر اساس ویژگیها و فرآیندهای تولید متفاوت است. این دو ماده اصلی برای تولید فولاد محسوب میشوند، اما راههای مختلفی را در این فرآیند طی میکنند. سنگ آهن بهعنوان ماده اولیه در تولید فولاد در کوره بلند به کار میرود. در این فرآیند، سنگ آهن با کک و سایر مواد نظیر سنگ آهک ترکیب میشود و تحت حرارت بالا ذوب میگردد تا آهن خام (چدن) تولید شود. این روش عمدتاً در صنایع فولادسازی بزرگ و قدیمیتر رایج است و بیشتر برای تولید فولاد در مقیاس وسیع به کار میرود. در این روش، سنگ آهن بهعنوان منبع اصلی تامین آهن در مراحل بعدی مانند تولید فولاد و آلیاژها عمل میکند. پس از تولید آهن خام، ناخالصیهای موجود بهعنوان سرباره جدا میشوند و فولاد خام برای مراحل بعدی تصفیه و شکلدهی آماده میشود. در فرآیند تولید آهن اسفنجی، با استفاده از روش احیای مستقیم سنگ آهن، تولید فولاد مستقیماً از آهن اسفنجی در کورههای قوس الکتریکی انجام میشود. این روش برای تولید فولاد در مقیاسهای کوچک و متوسط مفید و در کارخانههای فولادسازی مدرن و پیشرفته مرسوم است. آهن اسفنجی به دلیل درصد بالای آهن (۸۴ تا ۹۴ درصد)، برای تولید فولاد با کیفیت بالا بسیار مناسب است. علاوه بر این، چون فرآیند احیای مستقیم نسبت به روش سنتی کوره بلند کربن کمتری تولید میکند، گزینهای اقتصادیتر با تأثیرات زیستمحیطی کمتر به شمار میرود. به طور خلاصه، کاربرد صنعتی سنگ آهن عمدتاً در کورههای بلند برای تولید آهن خام است، در حالی که آهن اسفنجی غالباً در کورههای قوس الکتریکی برای تولید فولاد با کیفیت بالا و در مقیاس کوچکتر استفاده میشود. علاوه بر این، آهن اسفنجی بسیار رایج در کشورهایی است که دسترسی بیشتری به منابع گاز طبیعی دارند، زیرا فرآیندی اقتصادی با آلودگی کمتر محسوب میشود. همچنین، آهن اسفنجی برای تولید فولادهای خاص مانند آلیاژی و فولادهای با کیفیت بالا که در صنایع خودروسازی و مهندسی کاربرد دارند، بسیار مناسب است.
نوع کورههای مصرف کننده آهن اسفنجی و سنگ آهن
در فرآیند تولید فولاد، انتخاب نوع کوره یکی از جنبههای حیاتی است، زیرا این کورهها مسئولیت ذوب و تبدیل مواد اولیه به فولاد نهایی را دارند. به بررسی کورههای مصرفکننده سنگ آهن و آهن اسفنجی میپردازیم. کوره بلند در صنایع فولادسازی سنتی برای ذوب سنگ آهن نقش کلیدی دارد. در این فرآیند، سنگ آهن بههمراه کک و سنگ آهک بهطور مداوم وارد کوره میشود. کک بهعنوان عامل کاهنده و سوخت عمل میکند، و سنگ آهک برای حذف ناخالصیها و تشکیل سرباره استفاده میشود. در دمای بسیار بالا، واکنشهای شیمیایی صورت میگیرد که منجر به تبدیل اکسید آهن به آهن خام میشود. در پایان، آهن مذاب بهعنوان چدن جمعآوری میشود که نیازمند تصفیه بیشتر برای تبدیل به فولاد است. این روش در تولید فولاد در مقیاس بزرگ، خصوصاً در صنایع قدیمی و بزرگتر، کاربرد دارد. از سوی دیگر، کوره قوس الکتریکی مدرنتر بوده و برای تولید فولاد از آهن اسفنجی بهکار میرود. این نوع کوره از برق بهعنوان منبع حرارتی برای ذوب استفاده میکند و توانایی ذوب سریعتر و کنترل دقیق دما را داراست. در این کورهها، آهن اسفنجی که درصد آهن بالایی دارد مستقیم وارد شده و با افزودن عناصر مختلف نظیر کربن، کروم و نیکل میتوان فولاد با ویژگیهای خاص تولید کرد. این نوع کوره به دلیل بازده انرژی بالا و تأثیرات زیستمحیطی کمتر در صنایع مدرن بسیار محبوب است. همچنین در کشورهایی که منابع گاز طبیعی فراوان دارند مورد توجه قرار گرفته و بیشتر مناسب تولید فولاد در مقیاسهای متوسط و کوچک است، به خصوص جایی که از آهن اسفنجی یا ضایعات فلزی استفاده میشود. بهطور کلی، کوره بلند معمولاً برای ذوب سنگ آهن در مقیاس بزرگ استفاده شده و از کک بهره میبرد، در حالی که کوره قوس الکتریکی برای ذوب آهن اسفنجی و همچنین ضایعات فولادی مناسب است. برای مشاهده ورق رنگی کلیک کنید.
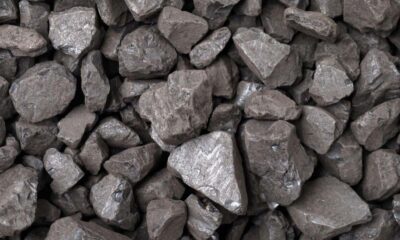
تفاوت سنگ آهن با آهن اسفنجی
ملاحظات زیستمحیطی
فرآیندهای تولید سنگ آهن و آهن اسفنجی بهصورت مستقیم بر محیطزیست و مصرف انرژی تأثیر میگذارند. این اثرات بهویژه در کورهها و روشهای تولید فولاد قابل مشاهده هستند و چالشهایی را برای صنعت فولادسازی ایجاد میکنند. در ادامه به ملاحظات زیستمحیطی و انرژی مربوط به تولید سنگ آهن و آهن اسفنجی پرداخته میشود. در فرآیند تولید سنگ آهن، استفاده از کوره بلند برای ذوب و تبدیل سنگ آهن به آهن خام به مصرف بسیار زیاد انرژی، بهویژه سوختهای فسیلی مانند کک نیاز دارد. یکی از اصلیترین ملاحظات زیستمحیطی این فرآیند، تولید حجم زیادی از گازهای گلخانهای، از جمله دیاکسید کربن (CO₂)، است که از واکنشهای شیمیایی در کوره بلند و سوختن کک ناشی میشود و به تغییرات اقلیمی و گرمشدن زمین کمک میکند. علاوه بر این، تولید سرباره بهعنوان یک ضایعه صنعتی که نیاز به دفع مناسب دارد، از دیگر چالشهای زیستمحیطی است. برای کاهش این تأثیرات، بعضی کارخانهها به فنآوریهای جدید مثل کورههای با کاهش انتشار CO₂ و روشهای بازیافت سرباره روی آوردهاند. از نظر مصرف انرژی، کوره بلند به مقادیر زیادی انرژی حرارتی نیاز دارد. برای کاهش هزینههای انرژی و افزایش کارایی، بهبود فرآیندها مانند استفاده از سیستمهای بازیابی حرارتی و بهینهسازی مصرف کک ضروری است. در این راستا، روشهای نوینی مانند استفاده از گازهای احیاکننده بهجای کک و کاهش نیاز به سوختهای فسیلی در برخی کورهها و فرآیندهای جدید همچون کورههای بازیابی انرژی مورد توجه قرار گرفتهاند. در فرآیند تولید آهن اسفنجی، احیای سنگ آهن با گاز طبیعی یا سایر گازهای احیاکننده انجام میشود. این روش نسبت به کوره بلند مصرف انرژی پایینتری دارد و میزان تولید CO₂ آن نیز بسیار کمتر است. استفاده از گاز طبیعی به جای کک که عامل اصلی انتشار CO₂ در فرآیند کوره بلند است، منجر به کاهش چشمگیر آلودگی هوا میشود. در مجموع، تولید آهن اسفنجی به دلیل کاهش انتشار گازهای گلخانهای و استفاده از منابع گازی سبزتر و کماثرتر تلقی میشود. از دیدگاه زیستمحیطی، کورههای قوس الکتریکی که آهن اسفنجی و ضایعات فولادی را به عنوان مواد اولیه مورد استفاده قرار میدهند، از دیگر گزینههای کمتأثیر هستند. در این روش، انرژی از طریق الکتریسیته تأمین میشود که در صورت استفاده از منابع تجدیدپذیر مانند انرژی خورشیدی یا بادی، میتواند اثرات زیستمحیطی را کاهش دهد. این روش همچنین باعث کاهش مصرف انرژی در مقایسه با فرآیندهای سنتی مانند کوره بلند میشود. بنابراین، صنعت فولاد با چالشهای بزرگی در زمینه مصرف انرژی و اثرات زیستمحیطی مواجه است. انتشار گازهای گلخانهای و مصرف بالای انرژی از مهمترین مسائل در فرآیندهای سنتی است. اما روشهای نوین مانند استفاده از گاز طبیعی در تولید آهن اسفنجی و کورههای قوس الکتریکی گزینههایی پاکتر و کارآمدتر هستند. توجه به ارتقاء فرآیندهای موجود و بهرهگیری از فنآوریهای جدید میتواند کمک شایانی به کاهش تأثیرات زیستمحیطی و بهبود بهرهوری انرژی نماید.
موقعیت استراتژیک کشورها
موقعیت استراتژیک کشورها در تولید سنگ آهن و آهن اسفنجی میتواند اهمیت زیادی برای دسترسی به منابع اولیه، کنترل هزینهها، استفاده از فناوریها و در نهایت رقابتپذیری جهانی در صنعت فولاد داشته باشد. این موقعیتها به دلیل تفاوتها در دسترسی به معادن سنگ آهن، منابع انرژی و زیرساختهای حمل و نقل متفاوت هستند. در ادامه، موقعیت استراتژیک چند کشور مهم در این صنعت مورد بررسی قرار گرفته است. کشورهایی که منابع غنی سنگ آهن دارند بهعنوان بازیگران اصلی صنعت فولاد شناخته میشوند. استرالیا، برزیل و چین سه کشور برجسته در تولید سنگ آهن هستند. استرالیا بهعنوان بزرگترین صادرکننده سنگ آهن درجهان شناخته شده و ذخایر عظیم آن در غرب کشور، نقشی کلیدی در تأمین نیاز جهانی سنگ آهن ایفا میکند. برزیل با داشتن معادن بزرگ در منطقه کاراخاس پس از استرالیا در رتبه دوم قرار دارد و چین نیز با تولید و مصرف گسترده سنگ آهن سهم مهمی دارد. در حوزه آهن اسفنجی، ایران، هند و امارات متحده عربی در روشهای احیای مستقیم نقش برجستهای دارند. ایران یکی از بزرگترین تولیدکنندگان آهن اسفنجی دنیا بوده و به سبب دسترسی گسترده به گاز طبیعی، این روشها را در صنعت فولاد خود توسعه داده است. هند نیز با استفاده وسیع از کورههای احیای مستقیم یکی از بازیگران اصلی است و امارات متحده عربی به همراه دیگر کشورهای خلیج فارس به دلیل داشتن انرژی و منابع گازی ارزان توجه ویژهای به تولید آهن اسفنجی دارند. چین که بزرگترین تولیدکننده فولاد جهان محسوب میشود، از دیدگاه موقعیت استراتژیک اهمیت زیادی دارد. این کشور علاوه بر مصرف گسترده سنگ آهن، بازار عمدهای برای آهن اسفنجی و فولادهای نهایی محسوب میشود و همچنین در توسعه فناوریهای نوین نظیر کورههای قوس الکتریکی پیشتاز است. آمریکا و اروپا نیز بهعنوان مصرفکنندگان عمده فولاد جهان به شمار میآیند. در این مناطق، تولید فولاد بیشتر بر پایه فناوریهای پیشرفته و استفاده از کورههای قوس الکتریکی تمرکز دارد. ایالات متحده با بهرهگیری از ضایعات فولادی و آهن اسفنجی توانسته جایگاه خود را به عنوان یکی از بزرگترین مصرفکنندگان فولاد تثبیت کند. موقعیت استراتژیک کشورها در تولید سنگ آهن و آهن اسفنجی تحت تأثیر منابع طبیعی، دسترسی به انرژی، فناوریهای تولید و قابلیتهای صادراتی است. کشورهایی مانند استرالیا، ایران و برزیل، با منابع غنی سنگ آهن و گاز طبیعی از این امکانات بهرهبرداری کردهاند و توانستهاند در بازار جهانی رقابت کنند. همچنین کشورهای صنعتی مانند چین، آمریکا و کشورهای اروپا با استفاده از فناوریهای پیشرفته، زیرساختهای مدرن و نیروی کار متخصص در خط مقدم این صنعت قرار دارند. برای مشاهده پروفیل زد کلیک کنید.
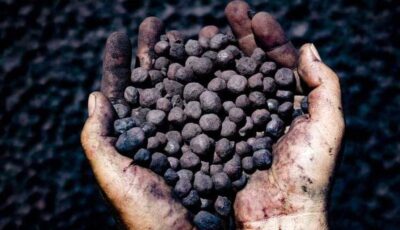
تفاوت سنگ آهن با آهن اسفنجی
هزینه و اقتصاد تولید آهن اسفنجی و سنگ آهن
هزینه و اقتصاد تولید در صنعت فولاد، بهویژه در زمینه تولید سنگ آهن و آهن اسفنجی، تحت تأثیر عوامل مختلفی مانند هزینه مواد اولیه، انرژی، نیروی کار، فناوریهای تولید و زیرساختهای حمل و نقل قرار دارد. این عوامل میتوانند قیمت نهایی محصول و رقابتپذیری در بازار جهانی را بهطور چشمگیری متأثر کنند. در اینجا به بررسی جنبههای اقتصادی و هزینههای تولید در این صنعت پرداختهایم. هزینههای مواد اولیه از مهمترین مواردی است که بر اقتصاد تولید فولاد اثرگذار است. در فرآیند تولید از سنگ آهن، هزینه خرید این ماده بخش قابل توجهی از کل هزینه تولید را شامل میشود. این هزینه بهصورت مستقیم تحت تأثیر قیمت جهانی سنگ آهن قرار دارد که خود وابسته به عرضه و تقاضا در بازارهای جهانی، وضعیت معادن و هزینههای استخراج است. کشورهایی مانند استرالیا و برزیل با منابع غنی، میتوانند هزینههای استخراج کمتری داشته باشند و قیمتهای صادراتی رقابتیتری ارائه دهند. در تولید آهن اسفنجی، هزینه گاز طبیعی (در روش احیای مستقیم) نیز اهمیت بسیاری دارد. کشورهایی با منابع گاز ارزانقیمت مانند ایران و قطر میتوانند قیمت تمامشده تولید این کالا را کاهش دهند و در بازارهای جهانی رقابت کنند. همچنین در کورههای قوس الکتریکی که از ضایعات فولادی یا آهن اسفنجی بهعنوان مواد اولیه بهره میبرند، هزینه این مواد بهعنوان بخش عمدهای از روند تولید مد نظر است. هزینههای انرژی عامل دیگری است که بر اقتصاد تولید فولاد تأثیر دارد. روش کوره بلند که برای تولید فولاد از سنگ آهن استفاده میشود، به انرژی حرارتی زیادی از سوختهای فسیلی نیاز دارد که این باعث بالا رفتن هزینههای تولید میشود. کورههای احیای مستقیم که معمولاً با گاز طبیعی بهجای سوختهای فسیلی کار میکنند، موجب کاهش هزینهها و انتشار کربن میشوند. هزینه نیروی کار و فناوری نیز تأثیر چشمگیری بر هزینههای تولید دارد. کشورهایی که دارای نیروی کار ماهر و کمهزینه هستند، معمولاً هزینههای کمتری دارند. مثلاً کشورهایی همچون هند و ایران با نیروی کار ارزانتر، قادر به کاهش هزینهها هستند. فناوریهای نوین مانند کورههای قوس الکتریکی و سیستمهای بازیابی انرژی نیز میتوانند هزینه انرژی را کاهش داده و بهرهوری را افزایش دهند. زیرساختهای حمل و نقل نقش مهمی در کاهش یا افزایش هزینههای تولید دارند. دسترسی به بنادر و زیرساختهای حمل و نقل پیشرفته میتواند هزینه حمل و نقل را پایین آورد و محصول نهایی را مقرونبهصرفهتر کند. کشورهای بزرگی مانند استرالیا و برزیل با داشتن بنادر کارآمد، هزینههای مرتبط با صادرات خود را کاهش میدهند. اقتصاد مقیاس نیز تأثیر قابلتوجهی در این صنعت دارد. کارخانههای بزرگ فولادسازی با ظرفیت تولید بالا میتوانند از مزایای اقتصاد مقیاس بهرهمند شوند؛ بدین معنا که هزینهها بین حجم بیشتری از تولید تقسیم میشود و در نتیحه قیمت نهایی کاهش پیدا میکند. علاوه بر این، خرید مواد اولیه در حجم بالا اغلب با قیمتهای پایینتر صورت میگیرد. در نهایت، رقابت جهانی در صنعت فولاد و تاثیرات اقتصادی آن بر قیمتگذاری نهایی محصول در بازارهای جهانی مؤثر است. کشورهای تولیدکننده باید با سایر رقبا رقابت کنند و برای موفقیت نیازمند بهینهسازی هزینهها هستند تا بتوانند جایگاه خود را در بازارهای بینالمللی حفظ کنند. در این مقاله به تفاوت تفاوت سنگ آهن با آهن اسفنجی پرداخته شد.