تاریخچه و تکامل ورق روغنی
در این مقاله به تاریخچه و تکامل ورق روغنی پرداخته می شود و به شما کمک می کند که در زمان بسیار کوتاه به بررسی موضوع مقاله پرداخته و دانش خود را در این حوزه ارتقا دهید. این مقاله بر اساس آخرین ژورنالهای صنعت فولاد گردآوری شده و تلاش شده که با بیان خلاصه و روان به موضوع پرداخته شود.
تاریخچه و تکامل ورق روغنی
ورق روغنی به عنوان نام عمومی ورق فولادی نورد سرد شناخته میشود که به دلیل صاف و براق بودن سطح آن، در صنایع مختلف کاربرد وسیعی دارد. تولید این ورقها با استفاده از فرآیند نورد سرد انجام میگیرد، به این معنا که پس از ساخت ورقهای نورد گرم، آنها را در دمای محیط تحت فشار دقیق غلتکها قرار میدهند تا ضخامت کاهش یافته و سطح صافی حاصل شود. برخلاف نورد گرم، فرآیند نورد سرد در دمایی کمتر از دمای تبلور مجدد انجام میپذیرد و نتیجه آن ورقی با خواص مکانیکی بهتر و ظاهری زیباتر است. ویژگی بارز ورق روغنی کیفیت بالای سطح آن است. این سطح صیقلیافته امکان استفاده در مواردی که زیبایی محصول اهمیت دارد، مانند لوازم خانگی، بدنه خودروها، تجهیزات صنعتی و حتی کابینتسازی را فراهم میکند. دقت در ضخامت این ورقها نیز بسیار بالا بوده و معمولاً با تلورانس کمتر از ۰.۱ میلیمتر ارائه میشود که برای مصارف حساس یک امتیاز محسوب میشود. از نظر ترکیب شیمیایی، ورقهای روغنی اغلب از فولاد کمکربن ساخته میشوند که توانایی شکلدهی خوبی دارد. برخی انواع خاص نیز برای کاربردهای مقاومتر طراحی شدهاند. این ورقها معمولاً تحت عملیات حرارتی مثل بازپخت قرار میگیرند تا ساختار کریستالی فولاد اصلاح شود و قابلیت شکلپذیری آن افزایش یابد. نامگذاری این نوع ورق به عنوان “روغنی” به دلیل استفاده از روغن محافظ سطحی در انتهای فرآیند تولید است. پس از پایان عملیات نورد و پرداخت نهایی، ورقها با یک لایه نازک از روغن صنعتی پوشش داده میشوند تا از زنگزدگی در هنگام انبارش و حمل و نقل محافظت شوند. این روغن کاملاً قابل شستوشو بوده و باید پیش از رنگکاری یا استفاده پاک شود. به طور کلی، ورق روغنی یکی از محصولات فولادی پرکاربرد است که به خاطر خواص سطحی و مکانیکی مناسب، در صنایع مختلف جایگاه ویژهای دارد. در سالهای اخیر، با توسعه صنایع خودروسازی و لوازم خانگی در ایران و جهان، تقاضا برای ورق روغنی به شدت افزایش پیدا کرده است. در این مقاله به تاریخچه و تکامل ورق روغنی می پردازیم.
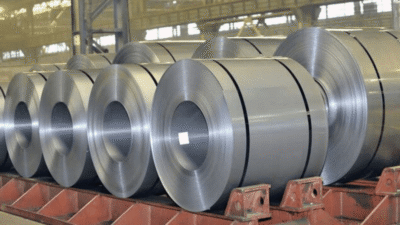
تاریخچه و تکامل ورق روغنی
تفاوت ورق روغنی و ورق سیاه
ورقهای فولادی روغنی و سیاه از انواع متداول با تفاوتهای عمده در تولید و ویژگیهای ظاهری و فنی به شمار میآیند. ورق سیاه از طریق نورد گرم تولید میشود، به این معنا که فولاد در دماهای بالا (بیش از ۱۱۰۰ درجه سانتیگراد) تحت فشار غلتکها شکل میگیرد. در مقابل، ورق روغنی با نورد سرد در دمای محیط ساخته میشود و دقت بیشتری در ابعاد و کیفیت سطح دارد. از نظر ظاهری، ورق سیاه اغلب دارای سطح خشن و تیره رنگ است، که ناشی از اکسیداسیون در فرآیند نورد گرم است. این ویژگی ممکن است برای مواردی که ظاهر اهمیت ندارد مناسب باشد، اما برای مواردی چون بدنه خودرو یا لوازم خانگی که نیاز به سطح صاف و براق دارند، قابل قبول نیست. در حالی که ورق روغنی دارای سطحی صاف، براق و یکنواخت است و برای کارهای دقیقتر استفاده میشود. در زمینه دقت ابعادی، ورق روغنی دارای برتری است. به دلیل انجام نورد سرد در دمای پایین، کنترل بهتری بر ضخامت، عرض و تختی ورق وجود دارد. این دقت سبب شده تا در تولید قطعات صنعتی و بدنههای فلزی دقیق یا هرجا که جزئیات اهمیت دارد، ورق روغنی گزینه اول باشد. از نظر خواص مکانیکی نیز تفاوتهایی وجود دارد. ورق سیاه معمولاً شکلپذیرتر است، زیرا ساختار فلزی آن تنش زیادی ندارد، اما ورق روغنی به دلیل فرآیند سرد شدن ساختارش سختتر است و برای برخی تغییر شکلها نیاز به بازپخت دارد. این ویژگی باعث افزایش مقاومت کششی ورق روغنی میشود که در بسیاری از موارد به عنوان یک مزیت محسوب میشود. در نهایت از لحاظ هزینه، ورق سیاه مقرونبهصرفهتر است چون فرآیند تولید آن سادهتر و کمهزینهتر است. در مقابل، ورق روغنی با توجه به نیاز به مراحل بیشتر مانند نورد سرد، روغنکاری و بازپخت، هزینه بالاتری دارد. انتخاب بین این دو نوع ورق بستگی کامل به نوع کاربرد، بودجه و نیاز صنعتی دارد.
تاریخچهی نورد سرد در جهان
نورد سرد بهعنوان یکی از مهمترین تحولهای صنعت فولاد، بیش از دویست سال سابقه دارد. این تکنیک در قرن ۱۸ و اوایل قرن ۱۹ میلادی شکل گرفت، زمانی که انقلاب صنعتی نیاز به قطعات فلزی با دقت بالا و سطحی صافتر را افزایش داد. در آن دوره، نورد گرم بهطور گسترده استفاده میشد، اما برای مواردی که نیاز به تلورانس دقیقتر و سطح صافتر داشتند، مهندسان به دنبال راهحلهای دقیقتر رفتند و فرآیند نورد سرد بهتدریج پدید آمد. کاربردهای اصلی نورد سرد در اروپا و آمریکا در اواسط قرن ۱۹ شروع شد. ابتدا برای نازککاری فلزات رنگین نظیر مس و برنج استفاده میشد، ولی بهمرور برای فولاد نیز توسعه یافت. در آن زمان، ماشینهای نورد دستی یا بخار، امکان فشردن ورقههای فلزی در دماهای پایین را فراهم کردند و با استفاده تدریجی از موتورهای الکتریکی، دقت تولیدات به شکل چشمگیری افزایش یافت. تا اوایل قرن بیستم، نورد سرد بهعنوان یکی از فرآیندهای صنعتی کلیدی شناخته شد و کارخانههای بزرگ فولادسازی در آلمان، انگلستان و ایالات متحده شروع به تجهیز خطوط نورد سرد کردند. تولید ورقههایی با ضخامت کمتر، سطحی بسیار بهتر و تلورانسهای دقیق باعث شد صنایع مهم مانند خودروسازی، ساخت ابزار دقیق و لوازم خانگی به شدت به این نوع محصول وابسته شوند. پیشرفتهای علمی و تکنولوژیکی در نیمه دوم قرن بیستم، بهویژه در زمینه مهندسی متالورژی و مکانیک جامدات، موجب بهبود فرآیند نورد سرد شد. روشهایی مانند بازپخت، Skin Pass و Rolling Schedule توسعه یافتند تا کیفیت محصول بالاتر برود و کنترل بر خواص مکانیکی دقیقتر شود. همزمان، استفاده از نورد سرد برای تولید فولادهای ویژه با مقاومت بالا همچون فولادهای Dual Phase یا TRIP رواج پیدا کرد. امروزه، نورد سرد یکی از ارکان اصلی صنعت فولاد جهان است و تقریباً در همه کشورهای صنعتی خطوط تولید تماماتومات با کنترل کامپیوتری موجود است. کشورهایی مثل چین، کره جنوبی، ژاپن، آلمان و آمریکا در توسعه تجهیزات پیشرفتهی نورد سرد پیشگام هستند و محصولات آنها در سطح جهانی صادر میشوند. برای مشاهده ورق سیاه کلیک کنید.
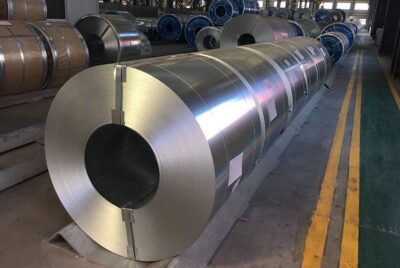
تاریخچه و تکامل ورق روغنی
تکامل فرایند تولید ورق روغنی
فرایند تولید ورق روغنی از ابتدای پیدایش تا کنون تحولات زیادی را تجربه کرده است. در آغاز، خطوط نورد سرد بسیار ساده و غالباً دستی بودند. ورقهای نورد گرم پس از سرد شدن بهصورت مکانیکی از میان غلتکها عبور داده میشدند تا ضخامت آنها کاهش یابد، اما به دلیل نبود تجهیزات دقیق، کیفیت سطحی و دقت ابعادی آنها قابل اعتماد نبود. با پیشرفت تکنولوژی، بهویژه در نیمه قرن بیستم، کارخانهها از غلتکهای دقیقتر و کنترل دمای بهتر در نورد سرد بهره گرفتند. همچنین دستگاههای بازپخت به خطوط تولید اضافه شدند تا تنشهای داخلی ناشی از نورد سرد رفع و قابلیت شکلدهی ورقها بهبود یابد. این توسعه باعث شد تا ورقهای روغنی نهتنها دقیقتر بلکه انعطافپذیرتر و مناسبتر برای شکلدهی عمیق باشند. از مراحل مهم اضافهشده به فرآیند میتوان به مرحله Skin Pass یا نورد سبک نهایی اشاره کرد. در این مرحله، ورق با فشار کم از میان غلتکها عبور میکند تا کیفیت سطح نهایی بهبود یابد و هرگونه موج یا ناهمواری احتمالی برطرف شود. این کار موجب افزایش یکنواختی ضخامت و بهبود خواص مکانیکی سطحی میشود. در دهههای اخیر، با ورود سیستمهای کنترل عددی مانند PLC و SCADA و سیستمهای کنترل کیفیت آنلاین، دقت تولید به سطح بیسابقهای رسیده است. اکنون کارخانههای مدرن قادرند ضخامت، سختی، یکنواختی سطح و حتی ترکیب شیمیایی ورق را در حین تولید اندازهگیری و تنظیم کنند. این تحولات ورق روغنی را به محصولی استراتژیک در صنایع با استانداردهای بالا مثل خودروسازی و الکترونیک تبدیل کرده است. تولید ورقهای روغنی خاص مانند فولادهای با استحکام بالا و فولادهای پوششدار نظیر گالوانیزه سرد، رنگی و ضدزنگ نیز به فرآیند نورد سرد افزوده شدهاند. این ورقها برای تحمل فشار و شکلدهی زیاد طراحی شدهاند و در عین حال خواص ضد خوردگی دارند. چنین روندهایی نشاندهنده ادامهی پیشرفت تکاملی ورق روغنی همگام با نیازهای صنایع و استانداردهای جهانی است.
جایگاه ورق روغنی در صنعت امروز
ورق روغنی یا ورق نورد سرد به دلیل ویژگیهای منحصربهفرد خود، در صنایع امروزی جایگاه ویژهای دارد. کیفیت سطحی بالا و دقت ابعادی از مهمترین دلایل استفاده گسترده از این نوع ورق هستند. این ویژگیها باعث میشود ورق روغنی در صنایعی که نیاز به ظرافت و دقت دارند، بسیار مورد استفاده قرار گیرد. یکی از کاربردهای اصلی آن در صنعت خودروسازی است؛ جایی که ورق روغنی به دلیل سطح صاف و مقاومت در برابر خوردگی برای تولید بدنه خودروها، قطعات داخلی و خارجی مانند دربها، سقفها و پنجرهها استفاده میشود. همچنین، قابلیت فرمدهی این ورقها امکان تولید قطعات پیچیده و دقیقتر را برای خودروسازان فراهم میکند. استفاده از فولادهای با استحکام بالا در ساخت خودروها، ایمنی آنها را افزایش میدهد. در صنعت لوازم خانگی مانند یخچالها، ماشین لباسشوییها، اجاق گازها و تلویزیونها نیز ورق روغنی بسیار کاربردی است. سطح براق و صاف این ورقها برای بخشهای خارجی محصولات خانگی مناسب است و خواص ضدزنگ آنها موجب افزایش دوام و طول عمر این محصولات میشود. در صنعت الکترونیک، ورق روغنی به عنوان بدنه تجهیزات الکتریکی، پوششها و قطعات داخلی مخابراتی مورد استفاده قرار میگیرد. کیفیت سطحی بالا و دقت ضخامت این ورقها امکان تولید اجزای دقیق الکترونیکی را فراهم میکند. علاوه بر این، در آنتنها و محفظههای مخابراتی نیز کاربرد دارند. در صنایع تولیدی و ساختمانی، از ورق روغنی برای ساخت قطعات دقیق مقاوم بهره برده میشود. صنایع نفت و گاز، معدن و ماشینآلات صنعتی به دلیل دقت بالا و تحمل فشارهای متعدد از این ورق به عنوان ماده اولیه برای تولید تانکها، لولهها و فریمها استفاده میکنند. در صنعت بستهبندی نیز ورق روغنی برای تولید جعبهها و بستهبندیهای مقاوم و فلزی مثل مواد غذایی و شیمیایی به کار میرود. با پیشرفت صنایع، استفاده از ورق روغنی در تولید ورقهای گالوانیزه، رنگی و ضدزنگ افزایش یافته است. این ورقها به دلیل مقاومت بیشتر در برابر خوردگی، خواص آنتیباکتریال و زیستمحیطی بهبود یافتهای دارند که در صنعت ساختمان و صنایع دریایی که مقاومت محیطی اهمیت دارد، مهم است. امروزه ورق روغنی با خواص مانند دقت ابعادی بالا، سطح صیقلی، قابلیت فرمدهی و مقاومت در برابر خوردگی، یکی از مواد پرکاربرد در تولیدات صنعتی محسوب میشود و نقش حیاتی در صنعت فولاد و دیگر صنایع مرتبط با تولید قطعات فلزی دارد. برای مشاهده تیرآهن کلیک کنید.
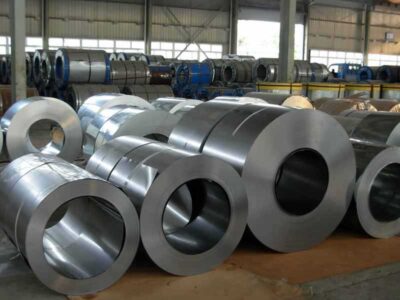
تاریخچه و تکامل ورق روغنی
تاریخچه تولید ورق روغنی در ایران
تولید ورق روغنی در ایران به دوران نیمه دوم قرن بیستم و آغاز رشد صنعت فولاد در کشور بازمیگردد. پیش از این دوره، ایران به علت کمبود زیرساختهای لازم، تولیدات فولادی چشمگیری نداشت و عمده نیازهای خود را از طریق واردات برآورده میکرد. با افزایش نیاز صنایع مختلفی همچون خودروسازی، لوازم خانگی و ساختمانسازی، توجه بیشتری به تولید ورقهای فولادی، به ویژه ورق روغنی در کشور معطوف شد. در دهه ۱۳۴۰ شمسی، ایران شروع به احداث اولین کارخانههای فولاد خود نمود. این کارخانهها که عمدتاً برای تولید فولاد ساختمانی طراحی شده بودند، به تدریج به تولید ورقهای فولادی نیز پرداخته و به چالشهایی برخورد کردند که ناشی از نیاز به تکنولوژی نورد سرد و تجهیزات پیشرفته بود، تکنولوژیای که در آن زمان در دسترس نبود. پیشرفتهای حقیقی تولید ورق روغنی در ایران به دهه ۱۳۷۰ شمسی برمیگردد. با ایجاد کارخانههایی نظیر مجتمع فولاد مبارکه در اصفهان که از بزرگترین تولیدکنندگان فولاد کشور است، زمینه مناسب برای تولید ورقهای روغنی پدیدار شد. این کارخانهها با استفاده از تکنولوژی نورد سرد توانستند ورقهای روغنی با کیفیت بالا تولید کرده و نیاز کشور به واردات این محصول را کاهش دهند. در دهه ۱۳۸۰ شمسی با توسعه بیشتر صنعت فولاد و رشد تکنولوژیهای نورد سرد، تولید ورق روغنی در ایران به سطح قابل قبولی رسید. علاوه بر فولاد مبارکه، سایر کارخانهها نیز به تولید این ورقها پرداختهاند و ایران به یکی از تولیدکنندگان بزرگ این محصولات در خاورمیانه تبدیل شده است. این پیشرفت امکان تأمین بخش بزرگی از نیازهای داخلی در صنایع مختلف، بهویژه خودروسازی، لوازم خانگی و ساختمانسازی را فراهم کرد. امروزه ایران در تولید ورق روغنی از خودکفایی مناسبی برخوردار بوده و علاوه بر رفع نیاز داخلی، قابلیت صادرات این محصولات به کشورهای منطقه را داراست. با ادامه رشد و توسعه صنعت فولاد، انتظار میرود تولید ورق روغنی در ایران همچنان افزایش یافته و کیفیت محصولات نیز به استانداردهای جهانی نزدیکتر شود.
مزایا و معایب ورق روغنی
ورق روغنی به دلیل ویژگیهای خاص خود، دارای مزایا و معایبی است که باید در انتخاب آن برای کاربردهای مختلف به این نکات توجه داشت. یکی از مهمترین مزایای آن، سطح صاف و براق است. فرآیند نورد سرد باعث میشود این ورقها سطحی یکدست و بدون عیوبی مانند زنگزدگی یا خش داشته باشند که در مواردی با نیاز به ظاهر و دقت از جمله بدنه خودرو، لوازم خانگی و صنعت الکترونیک، بسیار مناسب است. همچنین، این ورقها به دلیل دقت در فرآیند تولید، دقت ابعادی بالایی دارند که در صنایعی با نیاز به اندازهگیریهای دقیق و تحمل تلورانس کم، همچون خودروسازی و تجهیزات الکترونیکی، اهمیت دارد. از نظر استحکام نیز، ورقهای روغنی نسبت به ورق نورد گرم مقاومتر هستند و در کاربردهایی که به مقاومت در برابر فشار، تنش و خوردگی احتیاج است، استفاده از این نوع ورق مفید است. قابلیت بالای شکلدهی ورقهای روغنی نیز باعث میشود در تولید قطعات پیچیده و دقیق مورد استفاده قرار گیرند. افزون بر این، پوشش روغنی یا سطح صاف و بدون اکسید ورق روغنی باعث مقاومت بیشتر در برابر خوردگی، خصوصاً در محیطهای مرطوب و صنعتی میشود. اما، ورق روغنی معایب خاص خود را نیز دارد. تولید آن معمولاً هزینه بیشتری نسبت به ورق سیاه دارد به دلیل فرآیند پیچیدهتر نورد سرد و تجهیزات پیشرفتهتر. بنابراین، قیمت آن بالاتر است که ممکن است در برخی پروژهها محدودیتهایی ایجاد کند. بهعلاوه، ورقهای روغنی معمولاً با ضخامتهای نازکتر تولید میشوند که برای کاربردهایی با نیاز به ورقهای بسیار ضخیم ممکن است مناسب نباشند. صنایعی که به ورقهای ضخیم نیاز دارند، اغلب از ورقهای نورد گرم یا مواد دیگر استفاده میکنند. هرچند سطح صیقلی ورق روغنی جذاب است، اما این ویژگی آن را نسبت به آسیبهای سطحی حساس میکند؛ خراش یا ضربه ممکن است ظاهر آن را زودتر خراب کند. مقاومت کششی ورق روغنی نسبت به نورد گرم بیشتر است ولی در برخی کاربردها با نیاز به ویژگیهای مکانیکی خاص مثل انعطافپذیری بالا ممکن است نیاز به بازپخت داشته باشد. همچنین نگهداری این ورقها در شرایط رطوبتی و محیطی مناسب برای جلوگیری از زنگزدگی و آسیب ضروری است. برای مشاهده ورق آلیاژی کلیک کنید.
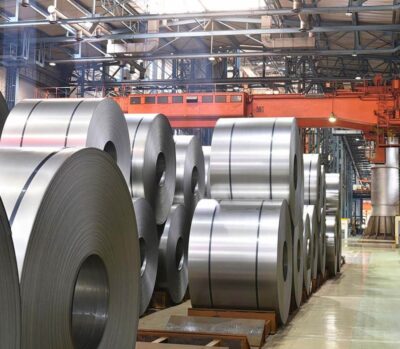
تاریخچه و تکامل ورق روغنی
آینده صنعت ورق روغنی
آینده صنعت ورق روغنی توسط چندین عامل مختلف تحت تأثیر قرار خواهد گرفت، از جمله روندهای جهانی، نیازهای متنوع صنایع و تحولات تکنولوژیکی. با توجه به ترقی فناوریها و افزایش تقاضا برای محصولات با کیفیت بالا و ویژگیهای خاص، این صنعت احتمالاً دستخوش تغییرات عمدهای خواهد شد. یکی از اصلیترین عواملی که آینده این صنعت را رقم میزند، تحول در روشهای تولید است. استفاده از فناوریهای جدید مانند اتوماسیون هوشمند و کنترل کیفیت آنلاین میتواند دقت تولید را تا سطح بیسابقهای ارتقا دهد. این پیشرفتها نه تنها هزینههای تولید را کاهش میدهند، بلکه امکان تولید ورقهای با کیفیت و ضخامت دقیقتر را فراهم میسازند. همزمان با این تحولات، نیاز به ورقهایی با ویژگیهای خاص در صنایع مختلف مانند خودروسازی، ساختمانسازی و لوازم خانگی رو به افزایش است. توجه به خصوصیات ویژه مانند مقاومت در برابر خوردگی، سختی بالا و ویژگیهای ضد زنگ برای کاربردهای خاص، به ویژه در صنعت خودروسازی و تجهیزات سنگین، همچنان حائز اهمیت خواهد بود. ورقهای با استحکام بالا و طراحی پیچیدهتر، به خصوص در ساخت بدنه و قطعات داخلی خودروها، توجه ویژهای را به خود جلب میکنند. علاوه بر این، نگرانیهای محیطزیستی و توجه به تولید پایدار محصولات فولادی نیز بر آینده صنعت ورق روغنی تأثیرگذار خواهد بود. به دلیل استفاده گسترده از ورق روغنی در صنایع مختلف، تولید آن با کمترین آلودگی و مصرف انرژی تبدیل به یک اولویت اساسی خواهد شد. صنعت فولاد در جهت استفاده از فناوریهای سبز و منابع انرژی تجدیدپذیر برای تولید محصولات حرکت خواهد کرد تا ضمن کاهش تأثیرات محیطی منفی، هزینههای تولید را نیز کاهش دهد. همچنین، افزایش صادرات ورق روغنی به بازارهای جهانی به ویژه در مناطق خاورمیانه و آسیا، روندی است که در آینده ادامه خواهد داشت. کشورهایی مانند ایران که به خودکفایی در تولید ورق روغنی دست یافتهاند، با بهرهگیری از کیفیت برتر و قیمتهای رقابتی، قادر خواهند بود سهم بیشتری از بازارهای بینالمللی را کسب کنند. در مجموع، با پیشرفت تکنولوژی، افزایش نیاز به محصولات خاص و ضرورت تولید پایدار، انتظار میرود که صنعت ورق روغنی در آینده با تغییرات چشمگیری مواجه شود و به سوی تولید محصولات متنوعتر، با کیفیت بالاتر و سازگارتر با محیطزیست حرکت نماید. در این مقاله به تاریخچه و تکامل ورق روغنی پرداخته شد.