نورد گرم
در این مقاله به نورد گرم پرداخته می شود و به شما کمک می کند که در زمان بسیار کوتاه به بررسی موضوع مقاله پرداخته و دانش خود را در این حوزه ارتقا دهید. این مقاله بر اساس آخرین ژورنالهای صنعت فولاد گردآوری شده و تلاش شده که با بیان خلاصه و روان به موضوع پرداخته شود.
نورد گرم چیست
نورد گرم یکی از فرآیندهای کلیدی شکلدهی فلزات است که طی آن فلز، بهویژه فولاد، در دماهای بالا (معمولاً بین ۱۱۰۰ تا ۱۳۰۰ درجه سانتیگراد) حرارت دیده و سپس از میان غلتکها عبور داده میشود. این فرآیند به کاهش ضخامت فلز و ایجاد شکل مطلوب آن کمک میکند. در نتیجه عملیات نورد گرم، ساختار بلوری فلز تغییر کرده و خواص مکانیکی آن بهبود مییابد. این روش بهعنوان یکی از رایجترین فناوریها برای تولید ورق ها، میلگردها و مقاطع فولادی شناخته میشود. دمای بالای کار باعث نرمتر شدن فلز میشود و فرآیند تغییر شکل را آسانتر میسازد. در مقایسه با سایر روشهای نورد، نورد گرم از نظر هزینه نسبت به نورد سرد ارزانتر است و برای تولیدات انبوه گزینه مناسبی محسوب میشود. بااینحال، محصولات حاصل از این فرآیند اغلب دارای سطحی زبر و پوشیده از پوستههای اکسیدی هستند که ممکن است نیازمند عملیات تکمیلی مانند اسیدشویی یا سنگزنی باشد. همچنین، در مرحله خنک شدن ممکن است ابعاد قطعه دچار تغییر یا اعوجاج شود که از دقت ابعادی آن میکاهد. به همین دلیل، در کاربردهایی که کیفیت سطح یا دقت بالا اهمیت دارد، استفاده از نورد سرد ترجیح داده میشود. فرآیند نورد گرم در صنایع مختلفی کاربرد دارد؛ از جمله ساختمانسازی، خودروسازی، کشتیسازی و صنایع نفت و گاز. از محصولات تولید شده به روش نورد گرم میتوان به ورق سیاه، تیرآهن، میلگرد، نبشی، ناودانی و لولههای فولادی اشاره کرد. با وجود برخی محدودیتها، این روش به دلیل سرعت بالا، کاهش هزینهها و قابلیت تولید در ابعاد و ضخامتهای گوناگون، همچنان یکی از پراهمیتترین روشهای شکلدهی فلزات در صنایع محسوب میشود.
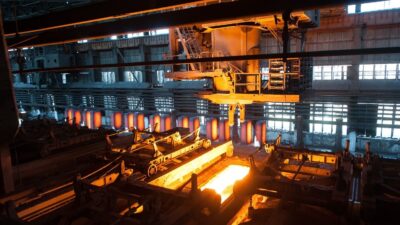
نورد گرم
تفاوت با نورد سرد
نورد گرم و نورد سرد دو روش اصلی در فرآیند شکلدهی فولاد هستند که تفاوت آنها بهطور عمده در دمای فرآیند و ویژگیهای محصول نهایی خلاصه میشود. در نورد گرم، دما به حدود ۱۱۰۰ تا ۱۳۰۰ درجه سانتیگراد میرسد که این شرایط باعث کاهش سختی و افزایش شکلپذیری فولاد میشود. در مقابل، نورد سرد معمولاً در دمای محیط یا کمی بالاتر انجام میشود و برای دستیابی به دقت ابعادی بالا و سطحی با کیفیت بهتر کاربرد دارد. این اختلاف دما تأثیر مستقیم بر ویژگیهای مکانیکی، ظاهر و دقت ابعادی محصول دارد. یکی از تفاوتهای برجسته این دو روش، سطح و دقت محصولات تولیدی است. محصولات حاصل از نورد گرم بهدلیل دمای بالا و خنککاری طبیعی، معمولاً سطحی زبر و پوستههای اکسیدی دارند. اما محصولات نورد سرد دارای سطحی صاف، براق و با دقت ابعادی بهتر هستند که برای کاربردهایی نظیر قطعات خودرو، لوازم خانگی و صنایع نیازمند دقت بالا مناسبتر است. همچنین، نورد سرد استحکام نهایی فلز را افزایش میدهد، زیرا این فرآیند سبب سختکاری بیشتر فولاد میشود. از منظر هزینه و کاربردهای صنعتی نیز تفاوتهای قابلتوجهی میان این دو روش وجود دارد. نورد گرم، باتوجه به مصرف انرژی کمتر و پیچیدگی کمتر فرآیند، هزینه تولید پایینتری داشته و برای تولید مقاطع بزرگ فولادی مانند ورق سیاه، میلگرد و تیرآهن مناسب است. از سوی دیگر، نورد سرد هزینه بیشتری دارد اما محصولاتی با کیفیت و دقت بالاتر تولید میکند که برای ساخت قطعات دقیق، پروفیلهای ظریف و ورقهای روغنی به کار میروند. بهطور کلی، انتخاب بین این دو روش به نیازهای صنعتی، بودجه و ویژگیهای مکانیکی مورد انتظار از محصول نهایی بستگی دارد.
ویژگی | نورد گرم | نورد سرد |
دمای فرایند | ۱۱۰۰-۱۳۰۰°C | دمای اتاق |
کیفیت سطح | زبر و دارای اکسید | صاف و براق |
دقت ابعادی | کمتر | بیشتر |
استحکام نهایی | متوسط | بیشتر |
قیمت | ارزان تر | گران تر |
کاربرد ها | ساختمان . خودرو . مخازن نفت | قطعات دقیق . لوازم خانگی |
تاریخچه و تکامل
نورد گرم بهعنوان یکی از قدیمیترین روشهای شکلدهی فلزات، ریشه در اعماق تاریخ دارد. اولین نشانههای کاربرد این روش به قرن هفدهم میلادی بازمیگردد، زمانی که از غلتکهای دستی برای کاهش ضخامت ورقهای طلا و نقره استفاده میشد. با انقلاب صنعتی در قرون هجدهم و نوزدهم، فناوری نورد دچار تحولی چشمگیر شد. در این دوران، صنعتگران اروپایی از ماشینهای نورد ساختهشده از چدن و فولاد برای تولید ورقها و میلههای فلزی بهره میبردند. همچنین، کورههای زغالی بهعنوان منبع حرارتی برای گرم کردن فلزات به کار گرفته میشدند و فرآیند نورد عمدتاً بهصورت دستی یا نیمهاتوماتیک انجام میشد. با ورود ماشینهای بخار و سپس نیروی الکتریسیته در قرن نوزدهم و اوایل قرن بیستم، نورد گرم به شکل یک فرآیند صنعتی گسترده جایگاه خود را تثبیت کرد. استفاده از کورههای گازی و الکتریکی امکان کنترل دقیق دمای فلزات را فراهم ساخت و در نتیجه، کیفیت تولید به طور قابلتوجهی افزایش یافت. توسعه نورد چندمرحلهای و غلتکهای هیدرولیکی در همین دوره امکان تولید مقاطع فولادی با اندازهها و ضخامتهای متنوع را به وجود آورد. این پیشرفتها نیازهای صنایع مختلف مانند ساختمانسازی، راهسازی و خودروسازی را پاسخ داد و نورد گرم را به یک روش کلیدی در تولید قطعات فولادی بدل کرد. در نیمه دوم قرن بیستم و اوایل قرن بیستویکم، با ظهور فناوریهای پیشرفته در زمینه اتوماسیون و کنترل کامپیوتری، دقت و بهرهوری در فرآیند نورد گرم به سطحی بیسابقه رسید. فناوریهایی نظیر کورههای القایی، حسگرهای دیجیتال و سیستمهای کنترل هوشمند باعث شدند که دمای فلزات، میزان کاهش ضخامت و کیفیت محصول نهایی با دقت بیشتری تنظیم شود. امروزه کارخانههای مدرن نورد گرم قادرند محصولات فولادی را با حجم بالا و حداقل میزان ضایعات تولید کنند. این دستاوردها، نورد گرم را به یک فرآیند بنیادین در صنعت فولاد جهان تبدیل کرده است که همچنان در مسیر پیشرفت و بهبود قرار دارد.
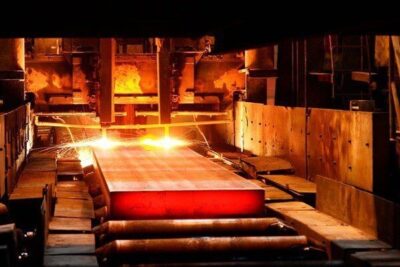
نورد گرم
مراحل فرایند نورد گرم
فرآیند نورد گرم با انتخاب و آمادهسازی مواد اولیه آغاز میشود، که معمولاً شامل شمش، بیلت یا اسلب است. این مواد از طریق ذوب فولاد در کورههای صنعتی تولید میشوند و در ابتدا بهصورت قطعات جامد و بزرگ هستند. پیش از انتقال به مرحله نورد، این قطعات باید به دمای مشخصی برسند. انتخاب دقیق ماده اولیه نقش بسزایی در کیفیت نهایی محصول دارد و تأثیر مستقیمی بر خواص مکانیکی آن برجای میگذارد. پس از انتخاب ماده اولیه، قطعات فلزی برای پیشگرم شدن وارد کورههای ویژه میشوند. بسته به نوع فلز، این کورهها میتوانند گازی، القایی یا الکتریکی باشند. دمای این کورهها معمولاً بین ۱۱۰۰ تا ۱۳۰۰ درجه سانتیگراد تنظیم میشود. هدف از پیشگرمایش، افزایش انعطافپذیری فلز و کاهش مقاومت آن در برابر تغییر شکل است. توزیع یکنواخت دما در سراسر قطعه ضروری بوده تا از بروز ترکخوردگی و تنشهای داخلی جلوگیری شود. پس از دستیابی به دمای مطلوب، قطعات فلزی از میان غلتکهای فولادی عبور داده میشوند. در این مرحله، ضخامت فلز کاهش یافته و طول آن افزایش پیدا میکند. فرآیند نورد به دو بخش اولیه و نهایی تقسیم شده و بسته به نوع محصول شامل مراحل متفاوتی است. تنظیماتی مانند سرعت غلتکها، میزان فشار و تعداد دفعات عبور، تأثیر مستقیمی بر خواص مکانیکی و کیفیت محصول نهایی دارند. در گام بعدی و پس از اتمام نورد، محصول وارد مرحله خنککاری میشود. این فرایند بهطور معمول با جریانهای هوای کنترلشده یا پاشش آب انجام میگیرد. نرخ کنترلشده خنککاری اهمیت بالایی دارد؛ چرا که سرد شدن سریع ممکن است باعث ایجاد تنشهای داخلی یا ترکخوردگی شود. همزمان، در این مرحله اندازهها، سطح، سختی و سایر خواص مکانیکی محصول بررسی و در صورت نیاز اصلاحات لازم اعمال میشود. در پایان، محصول به اندازههای استاندارد برش خورده و بستهبندی میشود تا آماده عرضه به بازار شود. برش ممکن است به روشهایی مانند گیوتینی، حرارتی (برش پلاسما) یا مکانیکی انجام شود. سپس محصولات دستهبندی شده و برای حمل آماده میشوند. برخی از محصولات نورد گرم، نظیر ورق سیاه یا میلگرد، ممکن است پیش از عرضه تحت فرآیندهای تکمیلی مانند اسیدشویی، گالوانیزاسیون یا نورد سرد قرار گیرند تا دقت ابعادی و کیفیت سطحی آنها بهبود یابد.
تجهیزات و ماشینآلات مورد استفاده
فرآیند نورد گرم به تجهیزات پیشرفته و بادوامی وابسته است که بتوانند شرایط سخت دما، فشار بالا و تغییرات فیزیکی فلزات را تحمل کنند. از مهمترین این تجهیزات میتوان به کورههای پیشگرم اشاره کرد که برای رساندن فلز به دمای مناسب ( بین ۱۱۰۰ تا ۱۳۰۰ درجه سانتیگراد) مورد استفاده قرار میگیرند. این کورهها، بسته به طراحی، ممکن است گازی، الکتریکی یا القایی باشند و نقش کلیدی در یکنواختسازی دمای فلز ایفا میکنند. افزون بر این، سیستمهای کنترل حرارت و سنسورهای دما به طور مؤثری دما را تنظیم کرده و از اکسید شدن سطح فلز جلوگیری میکنند. از دیگر اجزای اصلی در فرآیند نورد گرم میتوان به غلتکهای نورد اشاره کرد که مسئولیت کاهش ضخامت و شکلدهی فلز را بر عهده دارند. غلتکها معمولاً از فولاد آلیاژی سختشده ساخته میشوند تا مقاومت لازم در برابر فشار و حرارت بالا را داشته باشند. بسته به نوع محصول نهایی، مراحل نورد اولیه (Roughing Mill) و نورد نهایی (Finishing Mill) انجام میشود. برخی کارخانهها نیز از فناوریهای مدرن مانند سیستمهای هیدرولیکی و اتوماسیون پیشرفته بهره میگیرند تا سرعت و فشار غلتکها را با دقت کنترل کرده و کیفیت و یکنواختی محصول را بهبود بخشند. در ادامه این فرآیند، تجهیزاتی مانند سیستمهای خنککاری، دستگاههای برش و واحدهای بستهبندی نقش حیاتی در تکمیل تولید دارند. سیستمهای خنککاری شامل نازلهای آب یا جریانهای هوای کنترلشده هستند که سرعت خنکشدن فلز را مدیریت کرده و از مشکلاتی نظیر تغییر شکل یا ترکخوردگی جلوگیری میکنند. در انتهای خط تولید، دستگاههای برشی مانند گیوتین، ابزارهای برش حرارتی (پلاسما یا لیزر) و ابزارهای مکانیکی برای آمادهسازی محصولات در اندازههای دلخواه استفاده میشوند. تجهیزات حملونقل مانند جرثقیل سقفی، نوار نقاله و رباتهای صنعتی نیز برای جابهجایی قطعات سنگین و بستهبندی نهایی به کار گرفته میشوند که موجب افزایش بهرهوری خطوط تولید میشوند.
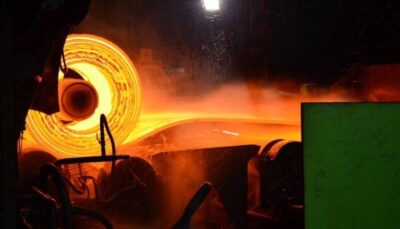
نورد گرم
مزایا و معایب نورد گرم
نورد گرم یکی از رایجترین روشهای تولید محصولات فولادی است که به دلایل متعدد در صنعت کاربرد گستردهای دارد. از جمله مزایای برجسته این روش، هزینه تولید پایینتر نسبت به نورد سرد است. به دلیل انجام فرآیند در دماهای بالا، فلز بهراحتی شکلپذیر شده و نیروی کمتری برای عبور از میان غلتکها مورد نیاز است. همچنین، این روش امکان تولید در مقیاس وسیع را فراهم میکند، که نه تنها بهرهوری را افزایش میدهد، بلکه به کاهش قابلتوجه هزینهها نیز منجر میشود. علاوه بر این، نورد گرم به بهبود ساختار دانهبندی فلز کمک کرده و استحکام آن را برای بسیاری از کاربردهای صنعتی ارتقا میبخشد. با این حال، این فرآیند بدون نقص نیست و محدودیتهایی نیز دارد. یکی از چالشهای اصلی نورد گرم، اکسید شدن سطح فلز در اثر دمای بالا است، که منجر به ایجاد پوستههای اکسیدی روی سطح محصول میشود. این مسئله میتواند کیفیت نهایی محصول را تحت تأثیر قرار دهد و گاه نیاز به فرآیندهایی نظیر اسیدشویی یا پرداخت سطحی را افزایش دهد. همچنین، کنترل دقیق ابعاد و تلرانسها در این روش مشکلتر است؛ زیرا فلز طی خنک شدن دچار انقباض و تغییرات جزئی در شکل میشود که به کاهش دقت ابعادی منجر میشود. یکی دیگر از جنبههای قابل توجه نورد گرم، نیاز به خنککاری مناسب و کنترلشده است. در صورتی که خنککاری با سرعت بالا انجام شود، احتمال ایجاد تنشهای داخلی یا ترکهای حرارتی در فلز وجود دارد، که میتواند کیفیت محصول را کاهش دهد. علاوه بر این، محصولاتی که طی فرآیند نورد گرم تولید میشوند معمولاً برای کاربردهای حساس و دقیق مناسب نیستند و ممکن است نیازمند فرآیندهای تکمیلی نظیر نورد سرد، سنگزنی یا پوششدهی باشند. با وجود این محدودیتها، به دلیل مزیتهایی چون سرعت، کاهش هزینه و تولید در مقیاس بالا، نورد گرم یکی از کلیدیترین روشهای تولید فولاد در صنایع مختلف باقی مانده است.
چالش ها و آینده
یکی از چالشهای اساسی در فرآیند نورد گرم، مصرف بالای انرژی است. چرا که این روش مستلزم استفاده از دماهای بسیار بالا (بین ۱۱۰۰ تا ۱۳۰۰ درجه سانتیگراد) میباشد، و همین امر، هزینههای مرتبط با سوختهای فسیلی و برق در کورههای پیشگرم را به شدت افزایش میدهد و تأثیر مستقیمی بر قیمت نهایی محصول میگذارد. از سوی دیگر، تشدید قوانین زیستمحیطی جهانی باعث شده تا کارخانههای نورد گرم برای کاهش انتشار گازهای گلخانهای و بهینهسازی مصرف انرژی تحت فشار بیشتری قرار گیرند؛ موضوعی که به چالشی بزرگ برای صنایع فولادی تبدیل شده است. چالش دیگر این فرآیند، محدودیت در دستیابی به دقت ابعادی بالا و کیفیت مطلوب سطح محصولات است. دمای بالای عملیات باعث انقباض و تغییر شکل جزئی فلز در هنگام خنک شدن میشود، که کنترل دقیق اندازهها را دشوار میسازد. همچنین، تشکیل پوستههای اکسیدی بر سطح فلز در طول فرآیند نورد میتواند کیفیت سطحی را کاهش دهد و نیاز به فرآیندهای تکمیلی نظیر اسیدشویی، نورد سرد یا پوششدهی افزایش یابد. این اقدامات اضافی نه تنها به هزینههای تولید میافزاید، بلکه ممکن است برخی کاربردهای صنعتی را نیز با محدودیتهایی مواجه کند. با وجود این محدودیتها، روند توسعه در نورد گرم به سمت نوآوری و بهرهوری بیشتر ادامه دارد. پیشرفت در فناوریهایی نظیر اتوماسیون، هوش مصنوعی و حسگرهای دیجیتال موجب شده تا فرآیندها با دقت بیشتری کنترل شوند و میزان ضایعات کاهش یابد. علاوه بر این، استفاده از کورههای القایی با بازده انرژی بالاتر و سیستمهای بازیافت حرارت، نقش مؤثری در کاهش مصرف سوخت و هزینههای عملیاتی دارند. توسعه آلیاژهای پیشرفتهتر و ارتقای روشهای خنککاری نیز نه تنها کیفیت محصولات را افزایش داده، بلکه امکان استفاده از آنها را در کاربردهای متنوعتری فراهم کرده است. بنابراین، علیرغم چالشها، آینده نورد گرم با نوآوریهای فناوری همراه بوده و بهعنوان یکی از روشهای محوری در تولید فولاد، همچنان جایگاه خود را حفظ خواهد کرد.